Thin films are created through a variety of deposition techniques, broadly categorized into chemical and physical methods. These methods allow precise control over the thickness, composition, and properties of the films, making them suitable for applications ranging from semiconductors to flexible electronics. The primary methods include Physical Vapor Deposition (PVD) and Chemical Vapor Deposition (CVD), with specific techniques like sputtering, thermal evaporation, spin coating, and atomic layer deposition (ALD) being widely used. Each method has its own advantages and is chosen based on the material properties and application requirements.
Key Points Explained:
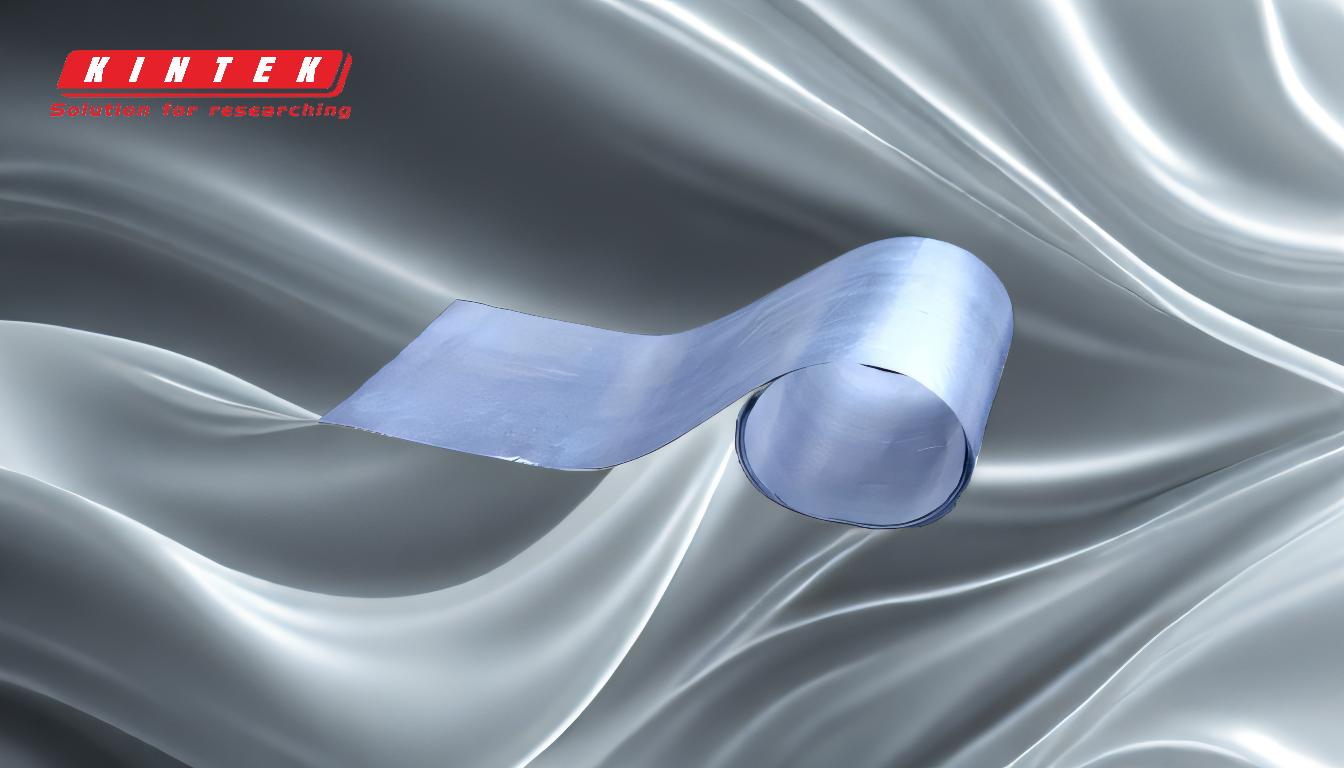
-
Overview of Thin Film Deposition:
- Thin film deposition involves the controlled synthesis of materials onto a substrate to form layers that can be as thin as a single atom.
- This process is crucial for applications in semiconductors, solar cells, OLEDs, and other advanced technologies.
-
Categories of Deposition Methods:
-
Chemical Deposition Methods:
- Chemical Vapor Deposition (CVD): Involves the reaction of gaseous precursors to form a solid film on the substrate. Variations include Plasma-Enhanced CVD (PECVD) and Atomic Layer Deposition (ALD).
- Electroplating: Uses an electric current to reduce dissolved metal cations to form a coherent metal coating.
- Sol-Gel: A wet-chemical technique that involves the formation of a colloidal suspension (sol) that transitions into a gel-like state.
- Dip Coating and Spin Coating: Techniques where the substrate is dipped into a solution or spun at high speeds to create a thin, uniform layer.
-
Physical Deposition Methods:
-
Physical Vapor Deposition (PVD): Involves the physical transfer of material from a source to the substrate. Common techniques include:
- Sputtering: Energetic ions bombard a target material, causing atoms to be ejected and deposited onto the substrate.
- Thermal Evaporation: Material is heated to a high temperature in a vacuum, causing it to evaporate and condense on the substrate.
- Electron Beam Evaporation: Uses an electron beam to heat the material, causing it to evaporate.
- Molecular Beam Epitaxy (MBE): A highly controlled process where beams of atoms or molecules are directed at the substrate to grow thin films layer by layer.
- Pulsed Laser Deposition (PLD): A high-power laser pulse vaporizes the target material, which then deposits onto the substrate.
-
Physical Vapor Deposition (PVD): Involves the physical transfer of material from a source to the substrate. Common techniques include:
-
-
Specific Techniques and Their Applications:
- Magnetron Sputtering: A type of PVD that uses a magnetic field to enhance the sputtering process, commonly used for creating thin films in the semiconductor industry.
- Atomic Layer Deposition (ALD): A precise method that allows for the deposition of films one atomic layer at a time, ideal for applications requiring exact thickness control.
- Spin Coating: Often used in the production of polymer thin films for applications like flexible solar cells and OLEDs.
- Plasma-Enhanced CVD (PECVD): Utilizes plasma to enhance the chemical reaction rates, allowing for lower temperature deposition, which is beneficial for temperature-sensitive substrates.
-
Advantages and Considerations:
-
Chemical Methods:
- Precision: Techniques like ALD offer atomic-level control over film thickness.
- Versatility: Can deposit a wide range of materials, including polymers and metals.
- Complexity: Often requires precise control of chemical reactions and environmental conditions.
-
Physical Methods:
- High Purity: PVD techniques can produce very pure films due to the high vacuum environment.
- Scalability: Methods like sputtering are scalable for industrial production.
- Energy Consumption: Some PVD techniques, like electron beam evaporation, can be energy-intensive.
-
-
Selection of Deposition Method:
- The choice of deposition method depends on the specific requirements of the application, including the desired film properties, substrate material, and production scale.
- For example, CVD is often chosen for its ability to produce high-quality, uniform films, while PVD is preferred for its ability to deposit a wide range of materials with high purity.
-
Future Trends:
- Ongoing advancements in thin film technology are focused on improving deposition rates, reducing costs, and enhancing the performance of thin films for emerging applications like flexible electronics and energy storage.
- Techniques like ALD and PECVD are expected to play a significant role in the development of next-generation devices.
By understanding these key points, one can appreciate the complexity and versatility of thin film deposition techniques, which are essential for the advancement of modern technology.
Summary Table:
Category | Methods | Key Features | Applications |
---|---|---|---|
Chemical Methods | CVD, ALD, Electroplating, Sol-Gel, Spin Coating | Precision, versatility, complex chemical control | Semiconductors, solar cells, OLEDs |
Physical Methods | PVD, Sputtering, Thermal Evaporation, MBE, PLD | High purity, scalability, energy-intensive | Flexible electronics, energy storage, advanced coatings |
Discover the best thin film deposition method for your project—contact our experts today!