Thin film deposition is a critical process in various industries, including semiconductors, optics, and energy. It involves creating thin layers of material on a substrate, which can range from nanometers to micrometers in thickness. The methods used for thin film deposition are broadly categorized into chemical and physical methods. Chemical methods include techniques like chemical vapor deposition (CVD), atomic layer deposition (ALD), and sol-gel, while physical methods encompass physical vapor deposition (PVD), sputtering, and thermal evaporation. Each method has its own advantages and is chosen based on the material properties, desired film characteristics, and application requirements. Understanding these methods is essential for selecting the right deposition technique for specific applications.
Key Points Explained:
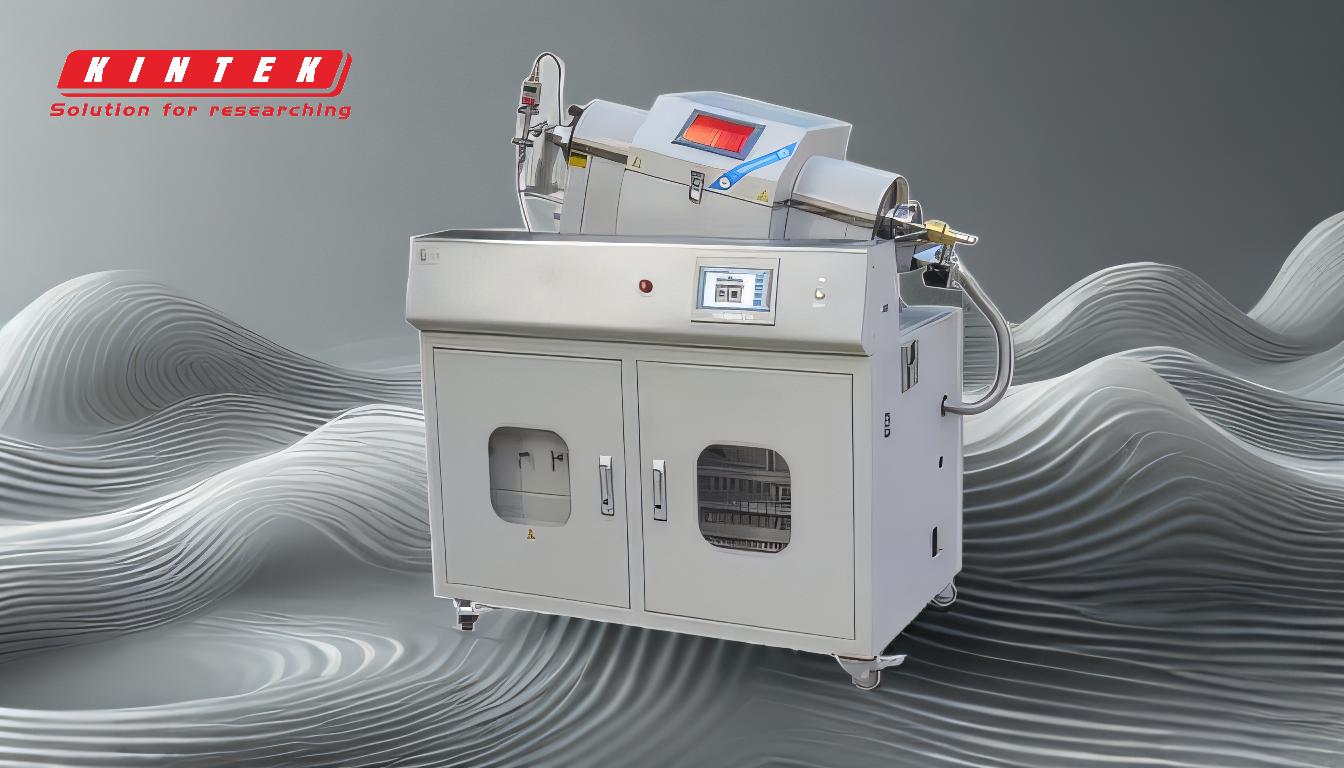
-
Chemical Deposition Methods:
- Chemical Vapor Deposition (CVD): This method involves the chemical reaction of gaseous precursors to form a solid thin film on a substrate. CVD is widely used in the semiconductor industry due to its ability to produce high-purity and high-quality films. It is particularly effective for depositing materials like silicon, silicon dioxide, and various metal oxides.
- Atomic Layer Deposition (ALD): ALD is a highly controlled process that allows for the deposition of films one atomic layer at a time. This precision makes it ideal for applications requiring ultra-thin and uniform coatings, such as in microelectronics and nanotechnology.
- Sol-Gel and Dip Coating: These methods involve the formation of a gel from a liquid precursor, which is then coated onto a substrate and cured to form a thin film. These techniques are often used for creating optical coatings and protective layers.
-
Physical Deposition Methods:
- Physical Vapor Deposition (PVD): PVD techniques involve the physical transfer of material from a source to a substrate in a vacuum environment. Common PVD methods include sputtering and thermal evaporation. PVD is known for producing high-purity coatings and is widely used in the production of thin films for electronics, optics, and decorative coatings.
- Sputtering: In sputtering, high-energy ions bombard a target material, causing atoms to be ejected and deposited onto a substrate. This method is versatile and can be used to deposit a wide range of materials, including metals, alloys, and ceramics.
- Thermal Evaporation: This method involves heating a material in a vacuum until it evaporates, and then condensing it onto a substrate. It is commonly used for depositing metals and organic materials.
-
Electron Beam and Ion Beam Techniques:
- Electron Beam Evaporation: This technique uses a focused electron beam to heat and evaporate a target material, which is then deposited onto a substrate. It is particularly useful for depositing high-melting-point materials and is often used in the production of optical coatings and semiconductor devices.
- Ion Beam Sputtering: This method uses an ion beam to sputter material from a target, which is then deposited onto a substrate. It offers precise control over film thickness and is used in applications requiring high-quality optical coatings.
-
Emerging and Specialized Methods:
- Molecular Beam Epitaxy (MBE): MBE is a highly controlled process used to grow epitaxial films, layer by layer, under ultra-high vacuum conditions. It is primarily used in the production of semiconductor devices and quantum wells.
- Pulsed Laser Deposition (PLD): PLD involves using a high-power laser pulse to ablate material from a target, which is then deposited onto a substrate. This method is used for depositing complex materials, such as high-temperature superconductors and ferroelectric films.
-
Selection Criteria for Deposition Methods:
- Material Compatibility: The choice of deposition method depends on the material to be deposited. For example, CVD is suitable for depositing oxides and nitrides, while PVD is better for metals and alloys.
- Film Properties: Different methods offer varying levels of control over film thickness, uniformity, and purity. ALD, for instance, provides excellent control over film thickness at the atomic level.
- Application Requirements: The specific application, such as semiconductor manufacturing, optical coatings, or flexible electronics, will dictate the most appropriate deposition method. For example, ALD is often used in microelectronics for its precision, while sputtering is preferred for large-area coatings.
By understanding the various thin film deposition methods and their respective advantages, one can make informed decisions when selecting the appropriate technique for a given application. Each method offers unique benefits and is suited to different materials and film properties, making it essential to consider the specific requirements of the project at hand.
Summary Table:
Method | Category | Key Features | Applications |
---|---|---|---|
Chemical Vapor Deposition (CVD) | Chemical | High-purity, high-quality films; ideal for oxides and nitrides | Semiconductors, metal oxides |
Atomic Layer Deposition (ALD) | Chemical | Ultra-thin, uniform coatings; atomic-level precision | Microelectronics, nanotechnology |
Sol-Gel and Dip Coating | Chemical | Optical coatings, protective layers | Optics, protective coatings |
Physical Vapor Deposition (PVD) | Physical | High-purity coatings; versatile for metals and alloys | Electronics, optics, decorative coatings |
Sputtering | Physical | Versatile; deposits metals, alloys, and ceramics | Large-area coatings, electronics |
Thermal Evaporation | Physical | Deposits metals and organic materials | Metals, organic materials |
Electron Beam Evaporation | Physical | High-melting-point materials; precise deposition | Optical coatings, semiconductor devices |
Ion Beam Sputtering | Physical | Precise control over film thickness | High-quality optical coatings |
Molecular Beam Epitaxy (MBE) | Specialized | Ultra-high vacuum; layer-by-layer growth | Semiconductor devices, quantum wells |
Pulsed Laser Deposition (PLD) | Specialized | Deposits complex materials like superconductors | High-temperature superconductors, ferroelectric films |
Need help selecting the right thin film deposition method? Contact our experts today for tailored solutions!