To increase your sputtering rate, you need to optimize several factors that influence the sputtering process, such as ion energy, plasma ionization, target material properties, and system parameters like chamber pressure and power source type. By increasing the sputtering yield (number of atoms ejected per incident ion) and enhancing the ionization degree of the plasma, you can achieve a higher sputtering rate. This involves adjusting parameters like ion energy, target material mass, and surface binding energy, as well as effectively utilizing secondary electrons to improve plasma ionization. Additionally, selecting the appropriate power source (DC or RF) and ensuring precise control of system conditions can further enhance the sputtering rate.
Key Points Explained:
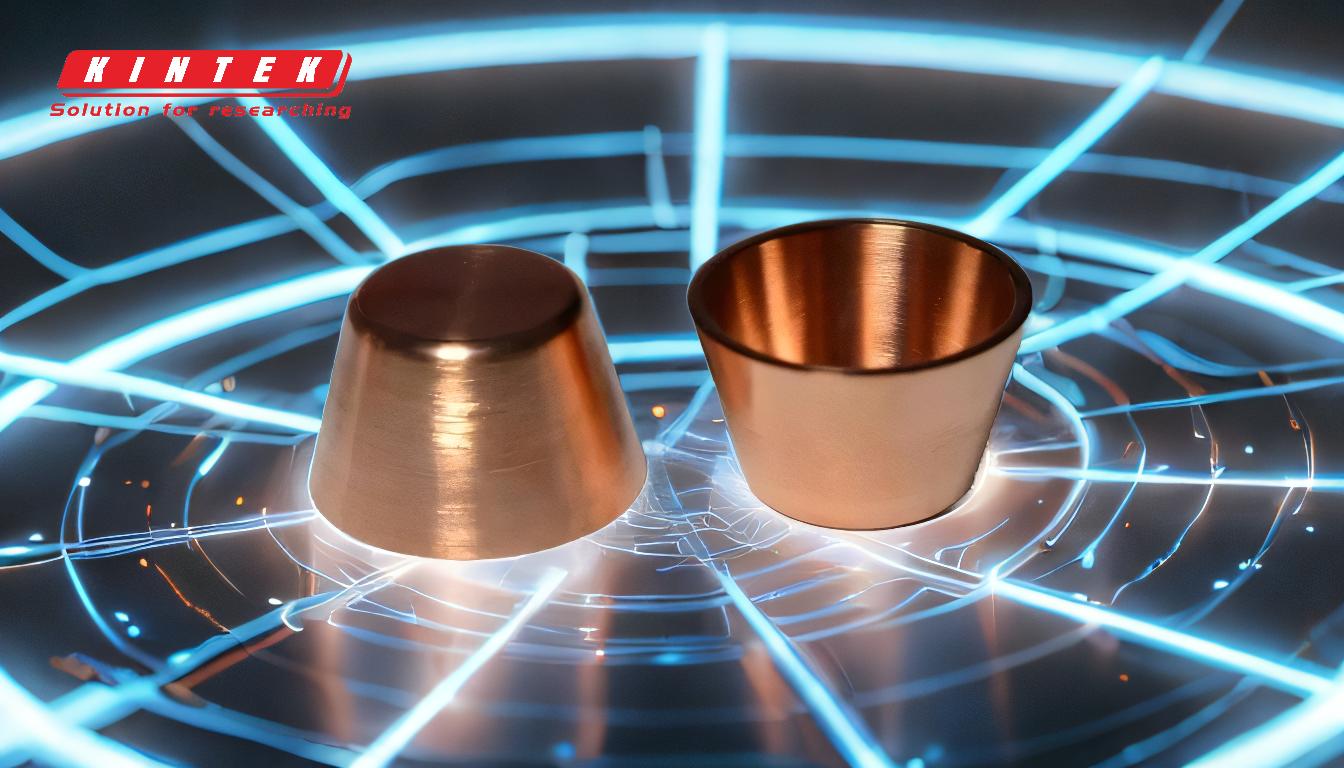
-
Increase Ion Energy:
- The sputtering yield (number of atoms ejected per incident ion) is directly influenced by the energy of the incident ions. Higher ion energy increases the likelihood of target atoms being ejected.
- To achieve this, you can increase the voltage or power supplied to the sputtering system, which will accelerate ions toward the target with greater kinetic energy.
- However, excessive ion energy can damage the target or substrate, so it’s important to find an optimal balance.
-
Optimize Plasma Ionization:
- A higher degree of plasma ionization means more ions are available to bombard the target, increasing the sputtering rate.
- Utilize secondary electrons effectively by using magnetic fields (e.g., magnetron sputtering) to trap electrons and enhance plasma density.
- Adjust the chamber pressure to maintain a stable plasma while avoiding excessive scattering of ions.
-
Select Appropriate Target Material:
- The sputtering yield depends on the mass of the target atoms and their binding energy. Materials with lower binding energy and higher atomic mass generally have higher sputtering yields.
- For example, heavy metals like gold or silver typically have higher sputtering rates compared to lighter materials like aluminum.
-
Control Chamber Pressure:
- Chamber pressure affects the mean free path of ions and the density of the plasma. Lower pressure can increase ion energy and reduce scattering, but too low a pressure may reduce plasma density.
- Optimal pressure ensures efficient ion bombardment while maintaining a stable plasma.
-
Use the Right Power Source:
- DC sputtering is suitable for conductive materials and provides a high deposition rate, while RF sputtering is better for insulating materials.
- Choose the power source based on the target material and desired sputtering rate. RF sputtering can also improve ionization in some cases.
-
Enhance Secondary Electron Utilization:
- Secondary electrons generated during sputtering can ionize more gas atoms, increasing plasma density.
- Techniques like magnetron sputtering use magnetic fields to confine electrons, improving ionization and sputtering efficiency.
-
Adjust Angle of Incidence:
- The angle at which ions collide with the target affects the sputtering yield. Off-normal angles often result in higher yields due to increased momentum transfer.
- Experiment with different angles to find the optimal configuration for your target material.
-
Monitor Ion Current Density:
- The sputtering rate is proportional to the ion current density (j). Increasing the current density (e.g., by increasing power or plasma density) can directly boost the sputtering rate.
- Ensure that the system can handle higher current densities without causing damage or instability.
-
Consider Target Crystallinity:
- If the target material has a crystalline structure, the orientation of its crystal axes relative to the surface can influence the sputtering yield.
- Align the target to maximize sputtering efficiency based on its crystal structure.
-
Use the Sputtering Rate Equation:
- The sputtering rate can be calculated using the equation:
Sputtering rate = (MSj)/(pNAe),
where:- M = molar weight of the target,
- S = sputter yield,
- j = ion current density,
- p = material density,
- NA = Avogadro number,
- e = electron charge.
- By optimizing these variables, you can systematically increase the sputtering rate.
- The sputtering rate can be calculated using the equation:
By carefully adjusting these factors and understanding their interplay, you can significantly increase your sputtering rate while maintaining the quality of the deposited film.
Summary Table:
Factor | Key Optimization |
---|---|
Ion Energy | Increase voltage or power for higher kinetic energy; avoid excessive energy. |
Plasma Ionization | Use magnetic fields (e.g., magnetron sputtering) to enhance plasma density. |
Target Material | Choose materials with lower binding energy and higher atomic mass (e.g., gold, silver). |
Chamber Pressure | Maintain optimal pressure for efficient ion bombardment and stable plasma. |
Power Source | Use DC for conductive materials; RF for insulating materials. |
Secondary Electrons | Confine electrons with magnetic fields to improve ionization. |
Angle of Incidence | Experiment with off-normal angles for higher sputtering yields. |
Ion Current Density | Increase current density (j) to boost sputtering rate. |
Target Crystallinity | Align target crystal structure for maximum efficiency. |
Sputtering Rate Equation | Use: Sputtering rate = (MSj)/(pNAe) to optimize variables. |
Ready to enhance your sputtering process? Contact our experts today for tailored solutions!