Nanotubes, particularly carbon nanotubes (CNTs), have emerged as a promising material for catalytic applications due to their unique structural, electronic, and mechanical properties. Their high surface area, tunable surface chemistry, and excellent electrical conductivity make them ideal candidates for catalysis. Nanotubes can be used as catalysts in various ways, including acting as catalyst supports, directly participating in catalytic reactions, or being functionalized to enhance their catalytic activity. Their applications span across fields such as energy conversion, environmental remediation, and chemical synthesis. Below, we explore the key mechanisms and applications of nanotubes in catalysis.
Key Points Explained:
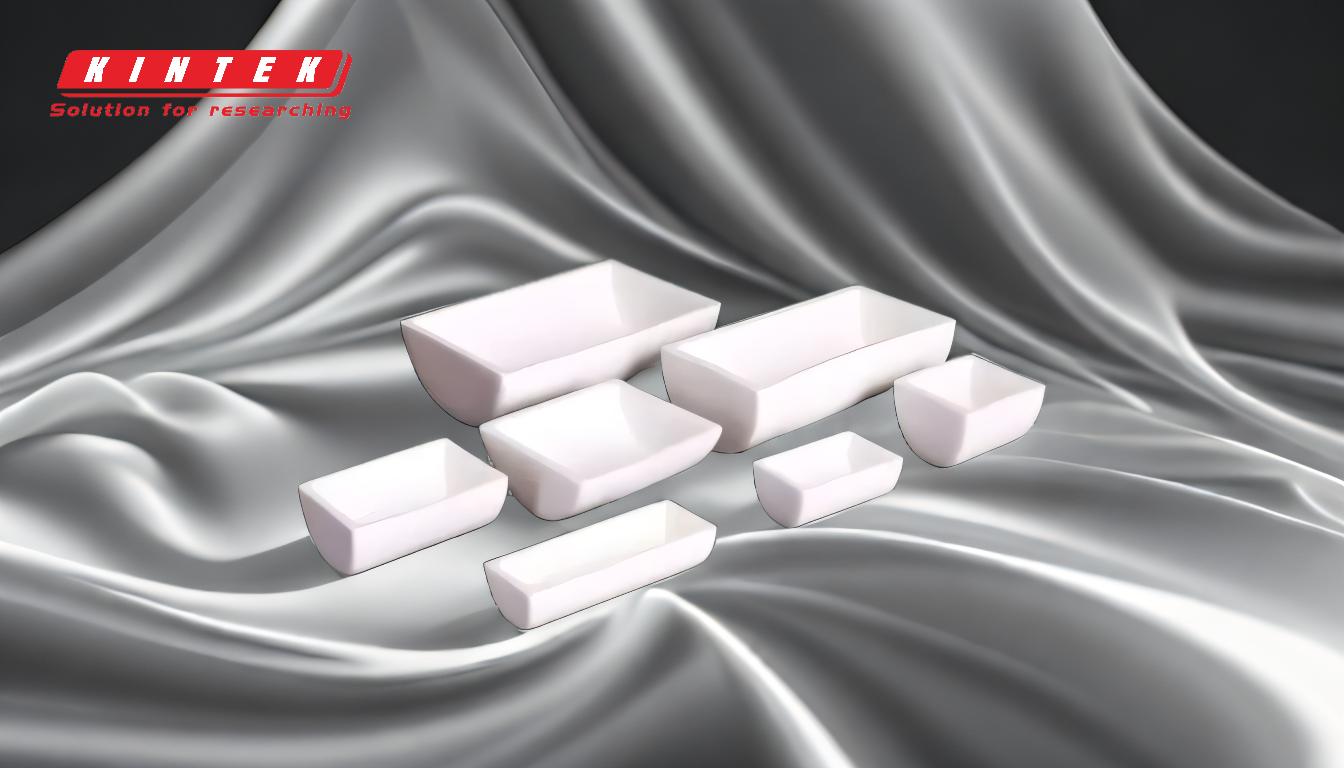
-
High Surface Area and Porosity
- Nanotubes, especially carbon nanotubes, possess a high surface area-to-volume ratio, which is crucial for catalytic applications. This allows for a greater number of active sites where reactions can occur.
- Their porous structure facilitates the diffusion of reactants and products, enhancing reaction efficiency.
- Example: In hydrogenation reactions, the high surface area of CNTs provides more sites for reactant adsorption, improving catalytic performance.
-
Tunable Surface Chemistry
- The surface of nanotubes can be chemically modified to introduce functional groups or attach metal nanoparticles, enhancing their catalytic properties.
- Functionalization with oxygen, nitrogen, or sulfur groups can alter the electronic structure, making nanotubes more reactive.
- Example: Nitrogen-doped carbon nanotubes exhibit improved catalytic activity in oxygen reduction reactions (ORR) for fuel cells.
-
Excellent Electrical Conductivity
- Carbon nanotubes are highly conductive, making them ideal for electrocatalytic applications where electron transfer is critical.
- This property is particularly useful in electrochemical reactions, such as water splitting or carbon dioxide reduction.
- Example: CNTs are used as supports for platinum nanoparticles in proton exchange membrane fuel cells (PEMFCs) to enhance electron transfer and reduce catalyst loading.
-
Catalyst Support
- Nanotubes are often used as supports for metal or metal oxide nanoparticles, which act as the primary catalysts.
- The strong interaction between the nanoparticles and the nanotube surface prevents aggregation and improves stability.
- Example: Palladium nanoparticles supported on CNTs show enhanced catalytic activity in hydrogenation and dehydrogenation reactions.
-
Direct Catalytic Activity
- Nanotubes themselves can act as catalysts due to their unique electronic structure and defect sites.
- Defects, such as vacancies or edge sites, can serve as active sites for catalytic reactions.
- Example: CNTs have been used as metal-free catalysts for the oxidative dehydrogenation of hydrocarbons.
-
Applications in Energy Conversion
- Nanotubes are widely used in energy-related catalytic processes, such as hydrogen production, fuel cells, and batteries.
- Their ability to facilitate electron transfer and stabilize reactive intermediates makes them valuable in these applications.
- Example: CNTs are employed in the oxygen reduction reaction (ORR) in fuel cells, where they enhance the efficiency of the reaction.
-
Environmental Remediation
- Nanotubes are used in catalytic processes for environmental cleanup, such as the degradation of pollutants or the conversion of harmful gases.
- Their high surface area and reactivity make them effective in breaking down organic pollutants or reducing nitrogen oxides.
- Example: CNTs functionalized with metal oxides are used to catalyze the reduction of NOx emissions from vehicles.
-
Challenges and Future Directions
- Despite their advantages, challenges such as scalability, cost, and potential toxicity need to be addressed for widespread adoption.
- Research is ongoing to develop more efficient and sustainable methods for nanotube synthesis and functionalization.
- Future applications may include the use of nanotubes in artificial photosynthesis or as catalysts for green chemistry processes.
In summary, nanotubes, particularly carbon nanotubes, offer a versatile platform for catalytic applications due to their unique properties. Their high surface area, tunable chemistry, and electrical conductivity make them suitable for a wide range of reactions, from energy conversion to environmental remediation. While challenges remain, ongoing research continues to unlock their full potential in catalysis.
Summary Table:
Property | Role in Catalysis | Example Application |
---|---|---|
High Surface Area | Provides more active sites for reactions, improving efficiency. | Hydrogenation reactions with CNTs. |
Tunable Surface Chemistry | Functionalization enhances reactivity and selectivity. | Nitrogen-doped CNTs in fuel cell ORR. |
Electrical Conductivity | Facilitates electron transfer in electrocatalytic reactions. | CNTs as supports in PEMFCs. |
Catalyst Support | Stabilizes metal nanoparticles, preventing aggregation. | Palladium nanoparticles on CNTs for hydrogenation. |
Direct Catalytic Activity | Defects and edge sites act as active sites for reactions. | Metal-free CNTs in oxidative dehydrogenation. |
Energy Conversion | Used in hydrogen production, fuel cells, and batteries. | CNTs in ORR for fuel cells. |
Environmental Remediation | Breaks down pollutants and reduces harmful emissions. | CNTs functionalized with metal oxides for NOx reduction. |
Discover how nanotubes can revolutionize your catalytic processes—contact our experts today!