Diamond-like carbon (DLC) coating is applied using advanced deposition techniques that ensure a strong, durable, and high-performance coating. The most common methods include Physical Vapor Deposition (PVD) and Chemical Vapor Deposition (CVD), with variations such as radio-frequency plasma-assisted CVD (RF PECVD) and hot-filament CVD. These methods involve creating a controlled environment in a vacuum chamber, where carbon atoms are activated and deposited onto the substrate. The choice of method depends on the substrate material, desired coating properties, and application requirements. DLC coatings are typically thin (0.5 to 2.5 microns) and provide excellent wear resistance, low friction, and enhanced durability.
Key Points Explained:
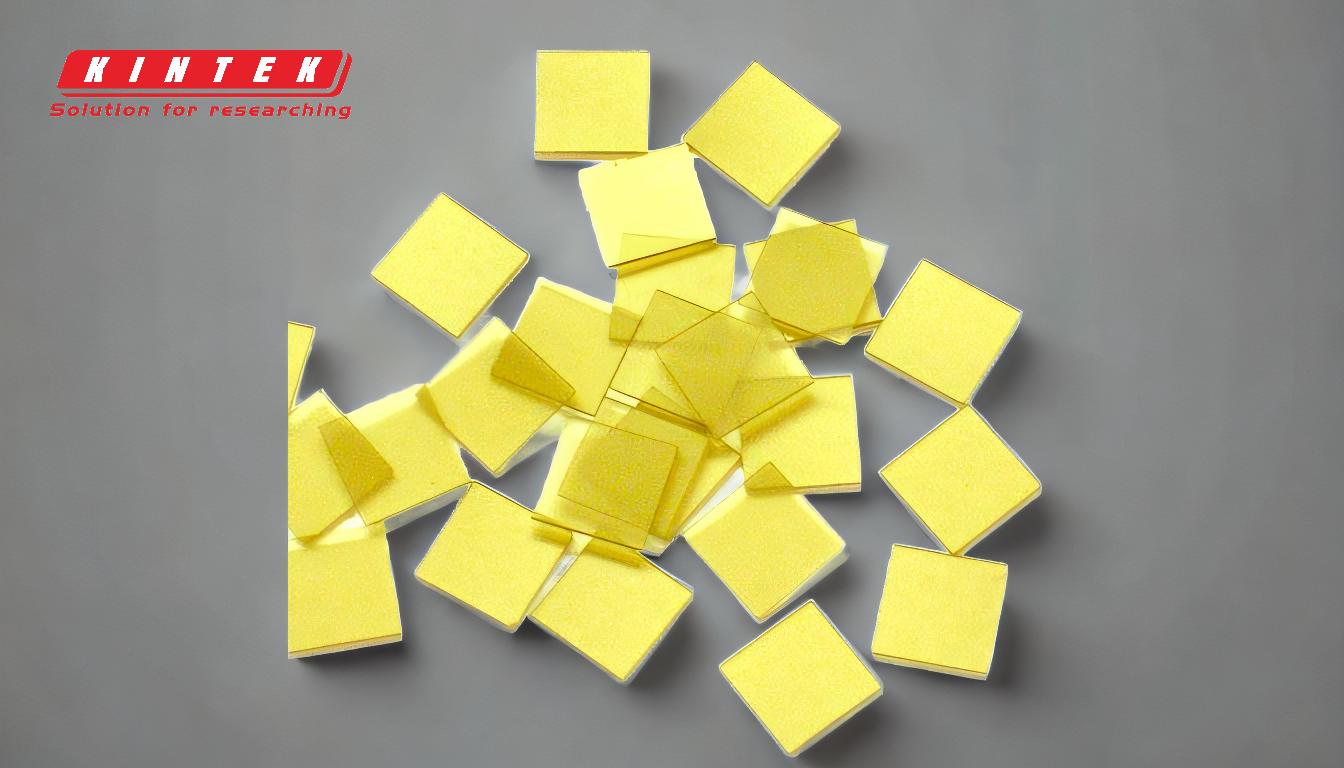
-
Overview of DLC Coating Application
- DLC coatings are applied using advanced deposition techniques to create a thin, durable layer of carbon with a significant proportion of sp3 bonds.
- The coating process is tailored to the substrate material and the intended application, ensuring optimal performance.
-
Common Deposition Methods
-
Physical Vapor Deposition (PVD):
- Involves evaporating a source material and allowing it to condense onto the substrate.
- Suitable for applying DLC coatings on carbide tools, with a typical thickness of 0.5 to 2.5 microns.
- Advantages include precise control over coating thickness and uniformity.
-
Chemical Vapor Deposition (CVD):
- Involves depositing carbon atoms from a gas phase (e.g., hydrogen and methane) onto the substrate.
- Common techniques include hot-filament CVD, radio-frequency plasma-assisted CVD (RF PECVD), and microwave plasma CVD (MPCVD).
- Requires high temperatures (over 750°C) to activate the gas molecules and form a diamond film.
-
Physical Vapor Deposition (PVD):
-
Step-by-Step Process for CVD Coating
-
Preparation:
- The substrate (e.g., tungsten carbide tools) is cleaned and prepared to ensure proper adhesion of the coating.
-
Loading into Chamber:
- The prepared tools are placed in a vacuum chamber containing hydrogen and methane gases.
-
Activation of Gas Molecules:
- Tungsten wires heated to over 2,300°C provide the energy to break up the gas molecules and heat the tools to over 750°C.
-
Deposition of Carbon Atoms:
- Activated carbon atoms recombine on the tool surface to form a pure diamond film.
-
Cooling and Removal:
- After deposition, the tools are cooled and removed from the chamber, ready for use.
-
Preparation:
-
Advantages of Different Methods
-
PVD:
- Lower processing temperatures, making it suitable for temperature-sensitive substrates.
- High precision and uniformity in coating thickness.
-
CVD:
- Produces high-quality, pure diamond films with excellent adhesion.
- Ideal for high-temperature applications and substrates that can withstand extreme conditions.
-
PVD:
-
Applications of DLC Coatings
-
Cutting Tools:
- Enhances wear resistance and extends tool life.
-
Automotive Components:
- Reduces friction and improves fuel efficiency in engine parts.
-
Medical Devices:
- Provides biocompatibility and wear resistance for surgical instruments.
-
Electronics:
- Improves durability and performance of components like hard drives and sensors.
-
Cutting Tools:
-
Considerations for Equipment and Consumable Purchasers
-
Substrate Compatibility:
- Ensure the chosen method is compatible with the substrate material (e.g., carbide, steel, or ceramics).
-
Coating Thickness and Uniformity:
- Evaluate the required thickness and uniformity for the specific application.
-
Cost and Scalability:
- Consider the cost-effectiveness and scalability of the chosen method for large-scale production.
-
Environmental and Safety Factors:
- Assess the environmental impact and safety requirements of the deposition process.
-
Substrate Compatibility:
By understanding these key points, equipment and consumable purchasers can make informed decisions about the best DLC coating method for their specific needs, ensuring optimal performance and cost-effectiveness.
Summary Table:
Aspect | Details |
---|---|
Common Methods | PVD, CVD (RF PECVD, Hot-Filament CVD) |
Coating Thickness | 0.5 to 2.5 microns |
Key Benefits | Wear resistance, low friction, durability |
Applications | Cutting tools, automotive parts, medical devices, electronics |
Substrate Compatibility | Carbide, steel, ceramics |
Temperature Range | PVD: Lower temps; CVD: Over 750°C |
Environmental Factors | Vacuum chamber, controlled gas environment |
Discover the ideal DLC coating solution for your needs—contact our experts today!