Carbonizing charcoal is a process that transforms organic material into charcoal through controlled heating in the absence of oxygen. This process involves several critical steps to ensure the material is properly carbonized without burning. The key steps include placing the material in a stove, sealing it to create an oxygen-free environment, allowing the carbonization to occur, and finally extracting the charcoal after cooling. Each step must be carefully managed to produce high-quality charcoal.
Key Points Explained:
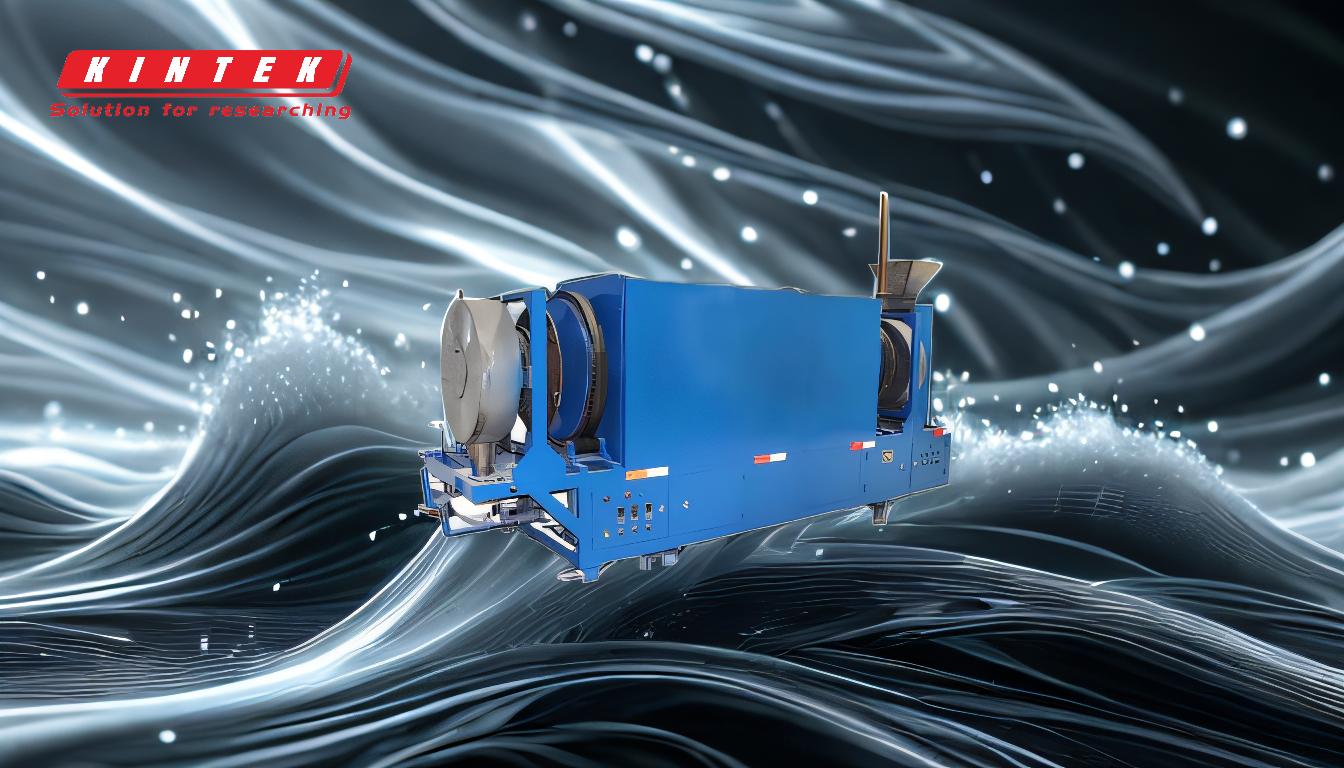
-
Placing the Material in the Stove
- The first step involves loading the organic material (such as wood, coconut shells, or agricultural waste) into a carbonization stove or kiln. The material should be arranged to allow even heating and airflow, which is crucial for uniform carbonization.
- Proper preparation of the material, such as cutting it into smaller pieces, can improve the efficiency of the process.
-
Sealing the Stove to Begin Carbonization
- Once the material is loaded, the stove or kiln is sealed to create an oxygen-free environment. This is essential because carbonization requires pyrolysis, a process that occurs in the absence of oxygen.
- Sealing prevents combustion, which would otherwise burn the material into ash instead of converting it into charcoal.
-
Heating and Carbonization Process
- The stove is heated to a specific temperature range (typically between 300°C and 500°C) to initiate pyrolysis. During this stage, volatile compounds, moisture, and gases are driven off, leaving behind carbon-rich charcoal.
- The duration of heating depends on the type and quantity of material being carbonized. Monitoring the process is crucial to avoid over- or under-carbonization.
-
Removing the Gasket After Carbonization
- Once the carbonization process is complete, the stove is allowed to cool. The gasket or seal is then removed to release any remaining gases and to prepare for the extraction of the charcoal.
- This step ensures that the charcoal is safe to handle and prevents the risk of spontaneous combustion.
-
Extracting the Charcoal After Cooling
- After the stove has cooled sufficiently, the charcoal is carefully extracted. The cooling process is critical to prevent the charcoal from igniting upon exposure to air.
- The final product is a stable, carbon-rich material that can be used for various applications, such as fuel, filtration, or soil amendment.
By following these steps meticulously, high-quality charcoal can be produced efficiently and safely. The process requires careful attention to temperature control, sealing, and cooling to achieve the desired results.
Summary Table:
Step | Key Actions | Purpose |
---|---|---|
Placing the Material in the Stove | Load organic material (wood, coconut shells, etc.) into the stove. Arrange for even heating. | Ensures uniform carbonization and efficient pyrolysis. |
Sealing the Stove | Seal the stove to create an oxygen-free environment. | Prevents combustion and ensures proper pyrolysis. |
Heating and Carbonization | Heat the stove to 300°C–500°C to drive off volatile compounds and moisture. | Converts organic material into carbon-rich charcoal. |
Removing the Gasket | Allow the stove to cool, then remove the gasket to release gases. | Ensures safety and prevents spontaneous combustion. |
Extracting the Charcoal | Carefully extract the cooled charcoal from the stove. | Produces stable, high-quality charcoal for various applications. |
Ready to produce high-quality charcoal? Contact us today for expert guidance and solutions!