Cleaning substrates for thin film deposition is a critical step to ensure high-quality film adhesion and prevent contamination. The process varies depending on the deposition method, such as Physical Vapor Deposition (PVD) or Chemical Vapor Deposition (CVD). Common cleaning methods include ultrasonic cleaning, preheating with high-energy electrons or infrared light, and advanced pre-cleaning techniques like RF glow plates, ion sources, and plasma pre-treaters. Each method has specific applications and benefits, tailored to the substrate's material and the deposition process requirements.
Key Points Explained:
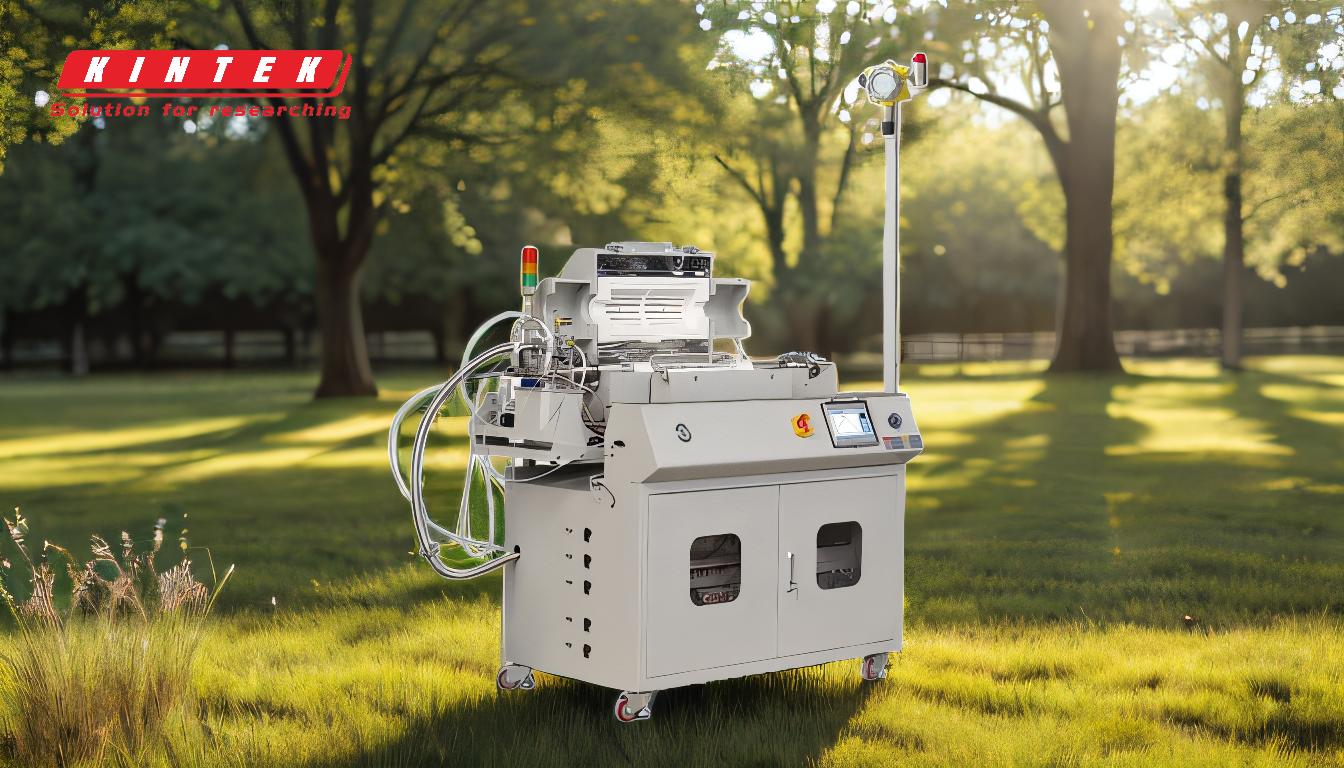
-
Importance of Substrate Cleaning
- Cleaning is essential to remove contaminants like dust, oils, and oxides that can negatively impact film adhesion and quality.
- The necessity of cleaning depends on the deposition method. For example, CVD requires thorough cleaning, while PVD may not always require it.
-
Ultrasonic Cleaning
- A widely used method where substrates are immersed in a cleaning solution and subjected to high-frequency sound waves.
- The ultrasonic waves create cavitation bubbles that dislodge contaminants from the substrate surface.
- Suitable for removing particulate matter and organic residues.
-
Preheating the Substrate
- Preheating can enhance film adhesion by increasing adatom–substrate and adatom–film diffusion.
- Methods include:
- Electron Gun: Focused high-energy electrons provide localized heating.
- Infrared Heater Lamps: Infrared light uniformly heats the substrate.
- Preheating helps overcome kinetic barriers, ensuring better film formation.
-
Advanced Pre-Cleaning Methods
- These methods are used for more rigorous cleaning, especially in high-precision applications.
- Techniques include:
- RF Glow Plate: Uses radiofrequency energy to generate a plasma that cleans the substrate.
- Gridded Ion Source: Directs ions to the substrate surface to remove contaminants.
- Gridless End-Hall Ion Source: Provides a broader ion beam for uniform cleaning.
- Plasma Pre-Treater: Utilizes plasma to clean and activate the substrate surface.
- RF or Microwave Plasma Pre-Treater: Combines plasma with RF or microwave energy for enhanced cleaning.
- Each method has specific benefits, such as improved surface activation or better removal of stubborn contaminants.
-
Deposition Method-Specific Cleaning Requirements
- PVD (Physical Vapor Deposition): Cleaning may not always be necessary, depending on the substrate and application. However, ultrasonic cleaning and preheating can still improve results.
- CVD (Chemical Vapor Deposition): Cleaning is mandatory to prevent contamination, as CVD involves chemical reactions that can be disrupted by impurities. Advanced pre-cleaning methods are often used here.
-
Choosing the Right Cleaning Method
- The choice of cleaning method depends on:
- The type of substrate material.
- The nature of contaminants.
- The specific requirements of the thin film deposition process.
- For example, plasma pre-treaters are ideal for polymeric substrates, while ion sources are better suited for metal or ceramic substrates.
- The choice of cleaning method depends on:
By carefully selecting and applying the appropriate cleaning method, you can ensure optimal substrate preparation, leading to high-quality thin film deposition and improved performance of the final product.
Summary Table:
Cleaning Method | Key Features | Applications |
---|---|---|
Ultrasonic Cleaning | High-frequency sound waves, removes particulate and organic residues | General cleaning for various substrates |
Preheating | Electron gun or infrared lamps, enhances adatom diffusion | Improves film adhesion |
RF Glow Plate | Radiofrequency plasma, removes stubborn contaminants | High-precision applications |
Gridded Ion Source | Focused ion beam, effective for metal/ceramic substrates | Rigorous cleaning for CVD processes |
Plasma Pre-Treater | Activates surface, removes contaminants with plasma | Ideal for polymeric substrates |
Ensure flawless thin film deposition—contact our experts today for tailored substrate cleaning solutions!