Controlling pressure in a hydraulic system is essential for ensuring its efficient and safe operation. This involves using various components and techniques to regulate, maintain, and adjust the pressure within the system. Key methods include the use of pressure relief valves, pressure regulators, accumulators, and variable displacement pumps. Understanding how these components work together helps in designing and maintaining hydraulic systems that meet specific performance requirements while preventing damage due to excessive pressure.
Key Points Explained:
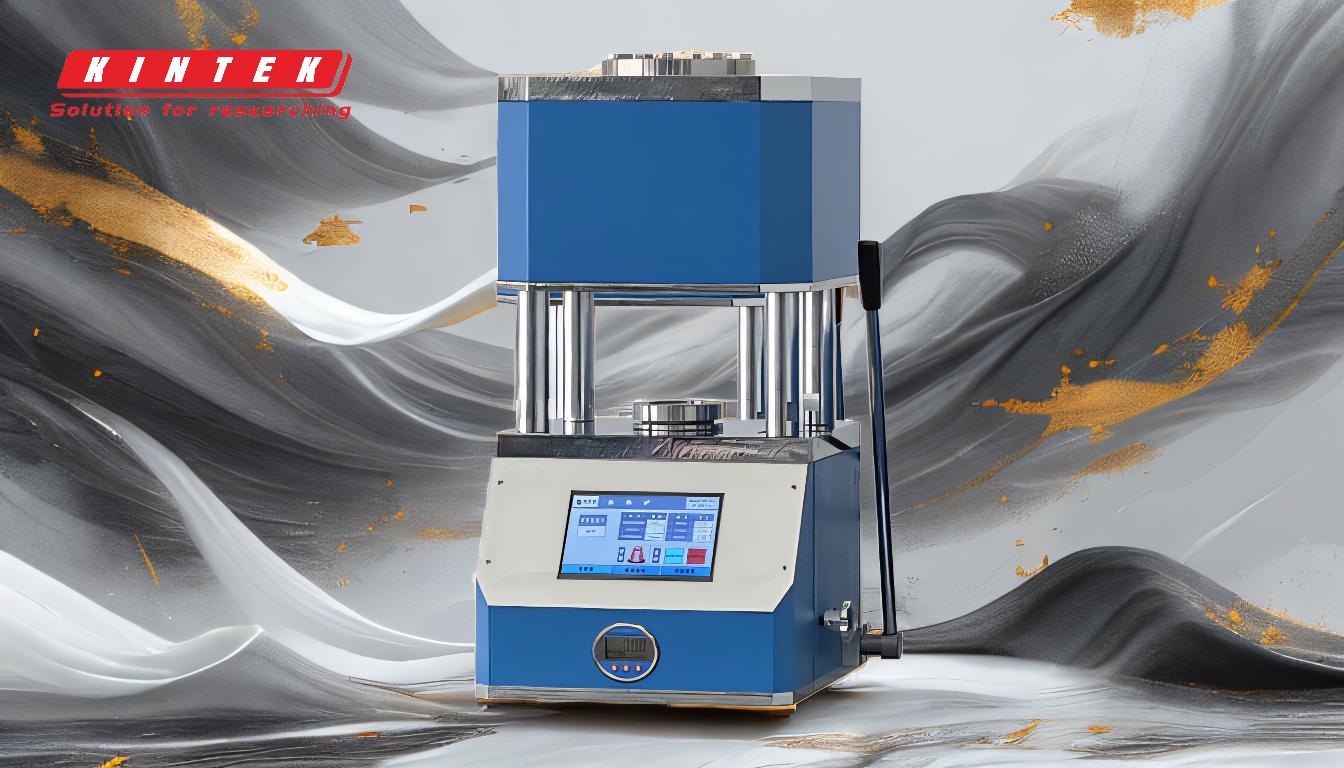
-
Pressure Relief Valves
- Function: Pressure relief valves are safety devices designed to limit the maximum pressure in a hydraulic system. They open when the pressure exceeds a set limit, allowing fluid to bypass the system and return to the reservoir.
- Importance: These valves protect the system from damage caused by overpressure, which can lead to component failure or catastrophic accidents.
- Application: Commonly used in systems where pressure spikes are expected, such as in heavy machinery or industrial equipment.
-
Pressure Regulators
- Function: Pressure regulators maintain a constant output pressure regardless of fluctuations in input pressure or flow demand. They adjust automatically to ensure consistent performance.
- Types: There are two main types: direct-acting and pilot-operated regulators. Direct-acting regulators are simpler and suitable for smaller systems, while pilot-operated regulators are used in larger, more complex systems.
- Usage: Ideal for applications requiring precise pressure control, such as in hydraulic presses or injection molding machines.
-
Accumulators
- Function: Accumulators store hydraulic energy in the form of pressurized fluid, which can be released when needed to maintain system pressure or absorb pressure surges.
- Types: Common types include bladder, piston, and diaphragm accumulators. Each type has specific advantages depending on the application.
- Benefits: They help stabilize pressure, reduce pump wear, and provide emergency power in case of pump failure.
-
Variable Displacement Pumps
- Function: These pumps adjust their output flow to match the system's demand, thereby controlling pressure more efficiently than fixed displacement pumps.
- Mechanism: By varying the displacement volume, the pump can reduce or increase flow without relying solely on pressure relief valves.
- Advantages: They improve energy efficiency and reduce heat generation, making them suitable for systems with varying load requirements.
-
Pressure Sensors and Feedback Systems
- Role: Pressure sensors monitor the system's pressure in real-time and provide feedback to control systems, enabling automatic adjustments.
- Integration: Often used in conjunction with electronic control units (ECUs) or programmable logic controllers (PLCs) to create closed-loop control systems.
- Benefits: Enhances precision and responsiveness, ensuring optimal performance under varying conditions.
-
System Design Considerations
- Load Requirements: The system must be designed to handle the maximum expected load while maintaining safe pressure levels.
- Component Sizing: Proper sizing of valves, pumps, and accumulators is critical to ensure effective pressure control.
- Maintenance: Regular inspection and maintenance of pressure control components are necessary to prevent failures and ensure long-term reliability.
-
Common Challenges and Solutions
- Pressure Spikes: Caused by sudden changes in load or flow, pressure spikes can be mitigated using accumulators or shock absorbers.
- Leakage: Hydraulic fluid leaks can lead to pressure drops, which can be addressed by ensuring proper sealing and regular maintenance.
- Cavitation: Occurs when the pressure drops too low, causing vapor bubbles to form and collapse, damaging components. This can be prevented by maintaining adequate inlet pressure and avoiding excessive pump speeds.
By understanding and implementing these methods, hydraulic system operators can effectively control pressure, ensuring safe and efficient operation across various applications.
Summary Table:
Component | Function | Key Benefits |
---|---|---|
Pressure Relief Valves | Limit maximum pressure by releasing excess fluid to prevent system damage. | Protects against overpressure, preventing component failure and accidents. |
Pressure Regulators | Maintain constant output pressure despite input fluctuations. | Ensures precise pressure control for consistent performance. |
Accumulators | Store pressurized fluid to stabilize pressure and absorb surges. | Reduces pump wear, stabilizes pressure, and provides emergency power. |
Variable Displacement Pumps | Adjust flow to match demand, controlling pressure efficiently. | Improves energy efficiency and reduces heat generation. |
Pressure Sensors | Monitor pressure in real-time and enable automatic adjustments. | Enhances precision and responsiveness for optimal system performance. |
Need expert advice on controlling pressure in your hydraulic system? Contact us today for tailored solutions!