Converting pyrolysis oil to diesel involves a series of refining and upgrading processes to transform the raw pyrolysis oil into a usable diesel-like fuel. Pyrolysis oil, derived from the thermal decomposition of organic materials, is often unstable, acidic, and contains impurities, making it unsuitable for direct use in engines. The conversion process typically involves hydrotreating, distillation, and other refining techniques to improve its quality, stability, and compatibility with diesel engines. Below is a detailed explanation of the key steps and considerations for converting pyrolysis oil to diesel.
Key Points Explained:
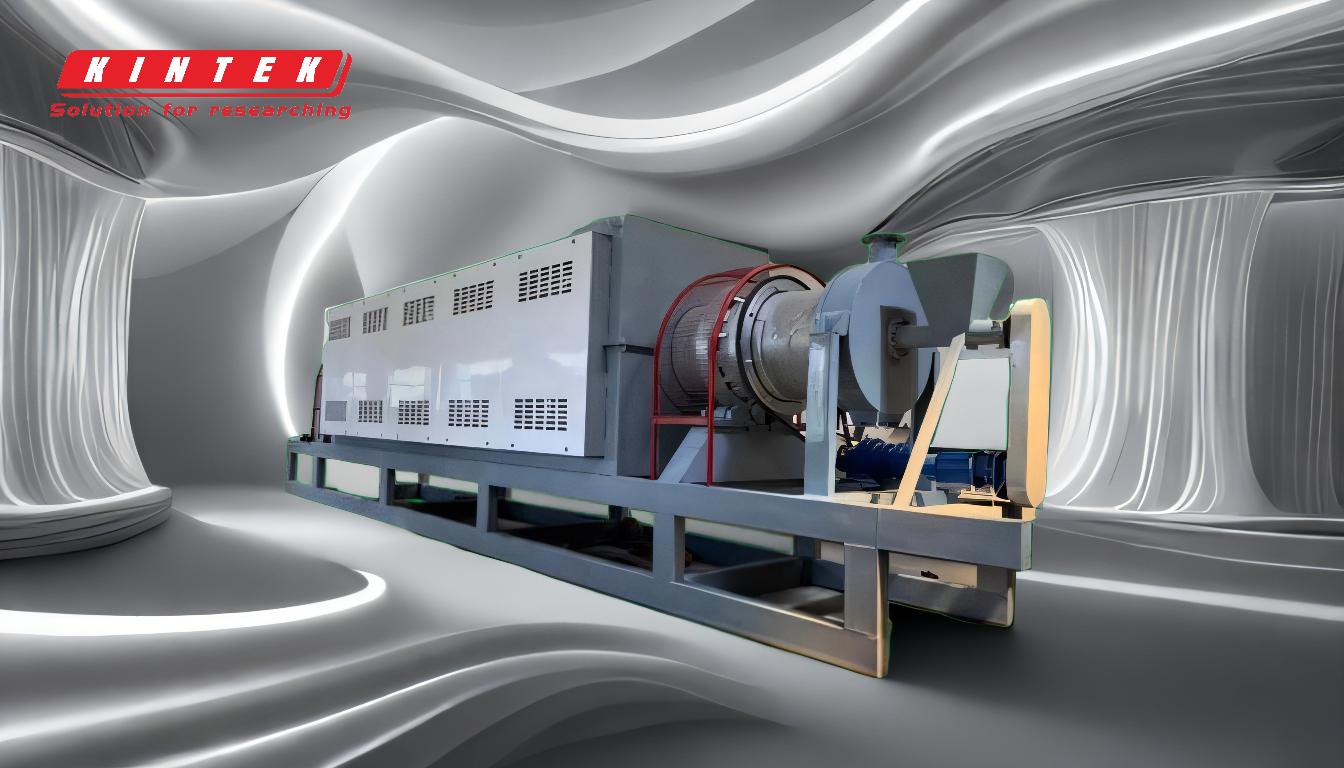
-
Understanding Pyrolysis Oil Composition
- Pyrolysis oil is a complex mixture of hydrocarbons, water, acids, and other organic compounds.
- It has a high oxygen content, which makes it unstable and corrosive.
- The presence of impurities, such as solid particles and heavy hydrocarbons, further limits its direct use as fuel.
-
Pre-Treatment of Pyrolysis Oil
- Filtration: Remove solid particles and debris to prevent clogging in downstream equipment.
- Dehydration: Reduce water content to improve the oil's energy density and stability.
- Acid Neutralization: Treat the oil with alkaline agents to neutralize acidic components and reduce corrosion risks.
-
Hydrotreating Process
- Hydrotreating is a critical step in upgrading pyrolysis oil to diesel.
- It involves reacting the oil with hydrogen under high temperature and pressure in the presence of a catalyst.
- This process removes oxygen, sulfur, and nitrogen compounds, converting them into water, hydrogen sulfide, and ammonia, respectively.
- The result is a more stable and hydrocarbon-rich oil with properties closer to conventional diesel.
-
Distillation and Fractionation
- After hydrotreating, the oil is subjected to fractional distillation to separate it into different fractions based on boiling points.
- The middle distillate fraction, which includes diesel-like hydrocarbons, is collected.
- Light fractions (e.g., gasoline) and heavy fractions (e.g., residual oil) are separated for further processing or blending.
-
Blending and Additives
- The distilled diesel fraction may need blending with additives to meet specific fuel standards.
- Additives can improve cetane number, lubricity, and cold flow properties.
- Blending with conventional diesel may also be necessary to achieve the desired fuel characteristics.
-
Quality Control and Testing
- The final product must undergo rigorous testing to ensure it meets diesel fuel standards (e.g., ASTM D975 or EN 590).
- Key parameters to test include viscosity, flash point, sulfur content, and cetane number.
- Compliance with environmental and safety regulations is essential for commercial use.
-
Applications of Converted Diesel
- The upgraded diesel can be used in standard diesel engines, generators, and industrial equipment.
- It offers a sustainable alternative to fossil-based diesel, reducing reliance on non-renewable resources.
- The process also contributes to waste management by converting waste materials into valuable fuel.
-
Challenges and Considerations
- High Capital Costs: Setting up a waste oil to diesel plant requires significant investment in equipment and infrastructure.
- Catalyst Deactivation: Catalysts used in hydrotreating may need frequent regeneration or replacement due to fouling.
- Feedstock Variability: The quality of pyrolysis oil can vary depending on the feedstock, requiring adjustments in processing conditions.
- Environmental Impact: Proper handling of by-products, such as hydrogen sulfide and ammonia, is necessary to minimize environmental harm.
By following these steps, pyrolysis oil can be effectively converted into a high-quality diesel fuel, offering a sustainable and economically viable solution for energy production and waste management.
Summary Table:
Step | Description |
---|---|
1. Pre-Treatment | Filtration, dehydration, and acid neutralization to remove impurities and stabilize the oil. |
2. Hydrotreating | React with hydrogen to remove oxygen, sulfur, and nitrogen compounds. |
3. Distillation | Fractional distillation to separate diesel-like hydrocarbons from other fractions. |
4. Blending | Additives and blending with conventional diesel to meet fuel standards. |
5. Quality Control | Rigorous testing to ensure compliance with diesel fuel standards (e.g., ASTM D975). |
6. Applications | Used in diesel engines, generators, and industrial equipment as a sustainable fuel. |
7. Challenges | High capital costs, catalyst deactivation, feedstock variability, and environmental considerations. |
Ready to explore sustainable fuel solutions? Contact our experts today to learn more about converting pyrolysis oil to diesel!