Heating a pyrolysis reactor is a critical step in ensuring efficient and effective thermal decomposition of materials. The process involves supplying heat through various methods, depending on the reactor type, the desired product yields, and the scale of operation. The primary methods include direct heat exchange using solid heat carriers or hot gas streams, indirect heat exchange through reactor walls or built-in tubes, and partial combustion within the reactor. These methods are tailored to suit different reactor designs, such as fluidized beds, fixed beds, and rotary systems, and are chosen based on factors like heating rate, temperature control, and energy efficiency.
Key Points Explained:
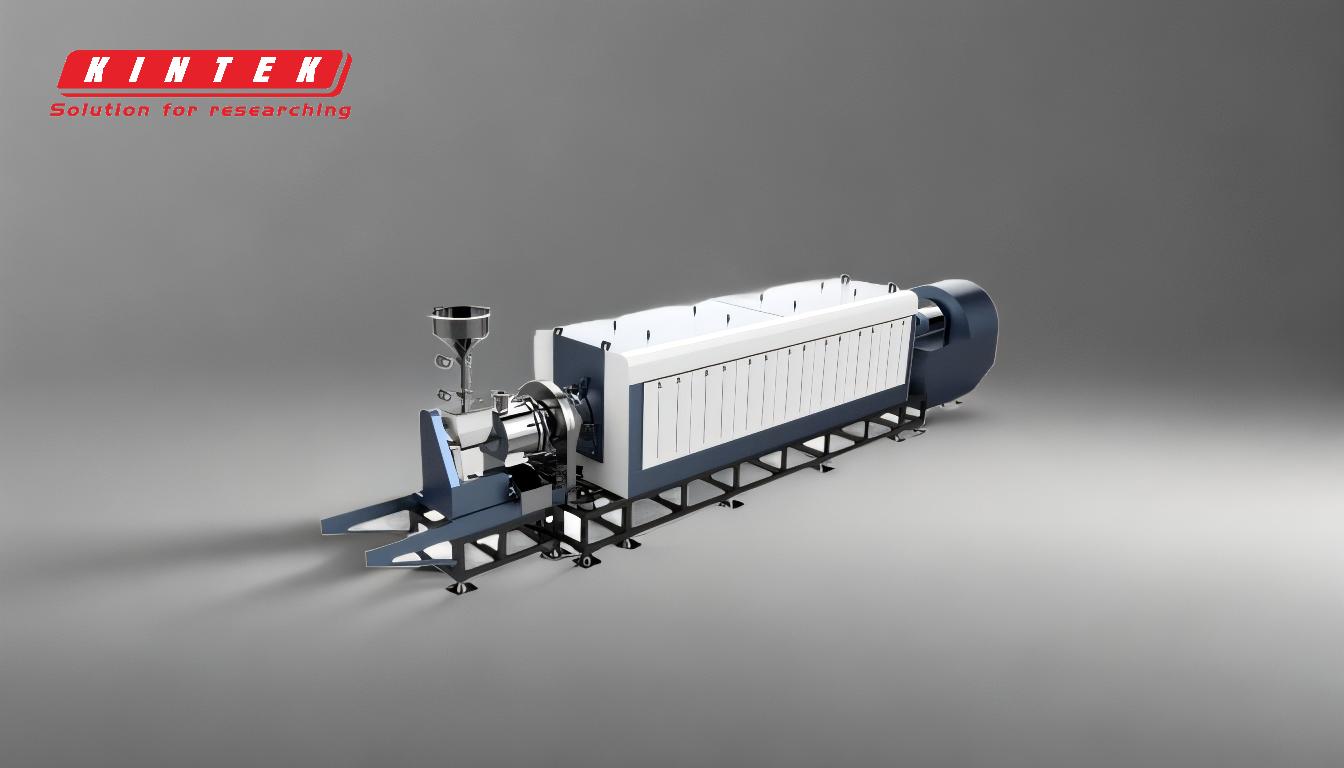
-
Methods of Heat Supply in Pyrolysis Reactors
-
Direct Heat Exchange:
- Involves using a solid heat carrier (e.g., sand) or a hot gas stream to transfer heat directly to the feedstock.
- Suitable for fast heating rates, which are essential for processes targeting high gas or liquid yields.
- Commonly used in fluidized bed reactors, where the heat carrier ensures uniform temperature distribution.
-
Indirect Heat Exchange:
- Heat is supplied through the reactor walls or built-in tubes/plates, avoiding direct contact between the heat source and the feedstock.
- Ideal for processes requiring precise temperature control and minimal contamination of the pyrolysis products.
- Often used in fixed bed or rotary reactors.
-
Partial Combustion:
- A portion of the feedstock or a secondary fuel is burned inside the reactor to generate heat.
- Used in batch systems like charcoal kilns, where air admission facilitates combustion of part of the biomass.
- Requires careful control to avoid excessive oxidation of the feedstock.
-
Direct Heat Exchange:
-
Reactor Types and Heating Methods
-
Fluidized Bed Reactors:
- Use solid heat carriers (e.g., sand) or hot gas streams for direct heat exchange.
- Provide rapid and uniform heating, making them suitable for fast pyrolysis.
-
Fixed Bed Reactors:
- Rely on indirect heat exchange through reactor walls or internal heating elements.
- Commonly used for slow pyrolysis, where longer residence times are required.
-
Rotary Reactors:
- Utilize indirect heat exchange via heated walls or tubes.
- Suitable for continuous processes with consistent feedstock feeding.
-
Batch Systems (e.g., Charcoal Kilns):
- Employ partial combustion of the feedstock to generate heat.
- Simple and cost-effective but less efficient than continuous systems.
-
Fluidized Bed Reactors:
-
Industrial Heating Techniques
-
Inert Combustion Gases:
- Heat is supplied using inert gases (e.g., nitrogen) in the absence of oxygen.
- Ensures high efficiency and prevents unwanted oxidation of the feedstock.
- Commonly used in large-scale, continuous pyrolysis processes.
-
Solid Energy Carriers:
- Inert materials like sand are heated externally and then mixed with the feedstock.
- Ideal for fast pyrolysis, where rapid heating is critical for maximizing liquid or gas yields.
-
Inert Combustion Gases:
-
Factors Influencing Heating Method Selection
-
Feedstock Type:
- Biomass, plastics, and other materials may require different heating methods based on their thermal properties.
-
Desired Product Yields:
- Fast pyrolysis for liquids or gases favors direct heat exchange, while slow pyrolysis for char may use indirect methods.
-
Scale of Operation:
- Batch systems are simpler but less efficient, whereas continuous systems are better suited for industrial-scale operations.
-
Energy Efficiency:
- Indirect heat exchange often provides better control and efficiency but may require more complex reactor designs.
-
Feedstock Type:
-
Advantages and Limitations of Heating Methods
-
Direct Heat Exchange:
- Advantages: Rapid heating, uniform temperature distribution, suitable for fast pyrolysis.
- Limitations: Potential contamination of products by the heat carrier.
-
Indirect Heat Exchange:
- Advantages: Precise temperature control, minimal contamination, suitable for slow pyrolysis.
- Limitations: Slower heating rates, higher energy requirements.
-
Partial Combustion:
- Advantages: Simple and cost-effective, suitable for batch systems.
- Limitations: Risk of feedstock oxidation, lower efficiency compared to continuous systems.
-
Direct Heat Exchange:
-
Emerging Trends in Pyrolysis Reactor Heating
-
Integration with Renewable Energy:
- Using solar or waste heat to supply energy for pyrolysis, reducing reliance on fossil fuels.
-
Advanced Heat Carriers:
- Development of novel materials (e.g., ceramic beads) for improved heat transfer and durability.
-
Hybrid Heating Systems:
- Combining direct and indirect methods to optimize heating rates and energy efficiency.
-
Integration with Renewable Energy:
By understanding these key points, equipment and consumable purchasers can make informed decisions about the most suitable heating methods and reactor designs for their specific pyrolysis applications.
Summary Table:
Heating Method | Description | Advantages | Limitations |
---|---|---|---|
Direct Heat Exchange | Uses solid heat carriers or hot gas streams for rapid, uniform heating. | Fast heating, uniform temperature, ideal for fast pyrolysis. | Potential contamination of products by heat carrier. |
Indirect Heat Exchange | Heat supplied through reactor walls or tubes, avoiding direct contact. | Precise temperature control, minimal contamination, suitable for slow pyrolysis. | Slower heating rates, higher energy requirements. |
Partial Combustion | Burns part of the feedstock or secondary fuel to generate heat. | Simple, cost-effective, suitable for batch systems. | Risk of feedstock oxidation, lower efficiency compared to continuous systems. |
Ready to optimize your pyrolysis process? Contact our experts today for tailored solutions!