Biochar is a carbon-rich material produced through the pyrolysis of biomass, which involves heating organic materials in the absence of oxygen. The process can be carried out using various methods, such as slow pyrolysis, fast pyrolysis, and gasification, each with distinct temperature ranges, heating rates, and residence times. Slow pyrolysis is particularly favored for producing high-quality biochar for agricultural use due to its consistent product quality. The production process typically involves pre-treatment (drying and crushing the biomass), pyrolysis (heating the biomass to produce biochar and byproducts), discharging (cooling the biochar), and de-dusting (cleaning exhaust gases). Biochar's properties, such as porosity and the ability to sorb contaminants, depend on the feedstock, pyrolysis conditions, and post-processing.
Key Points Explained:
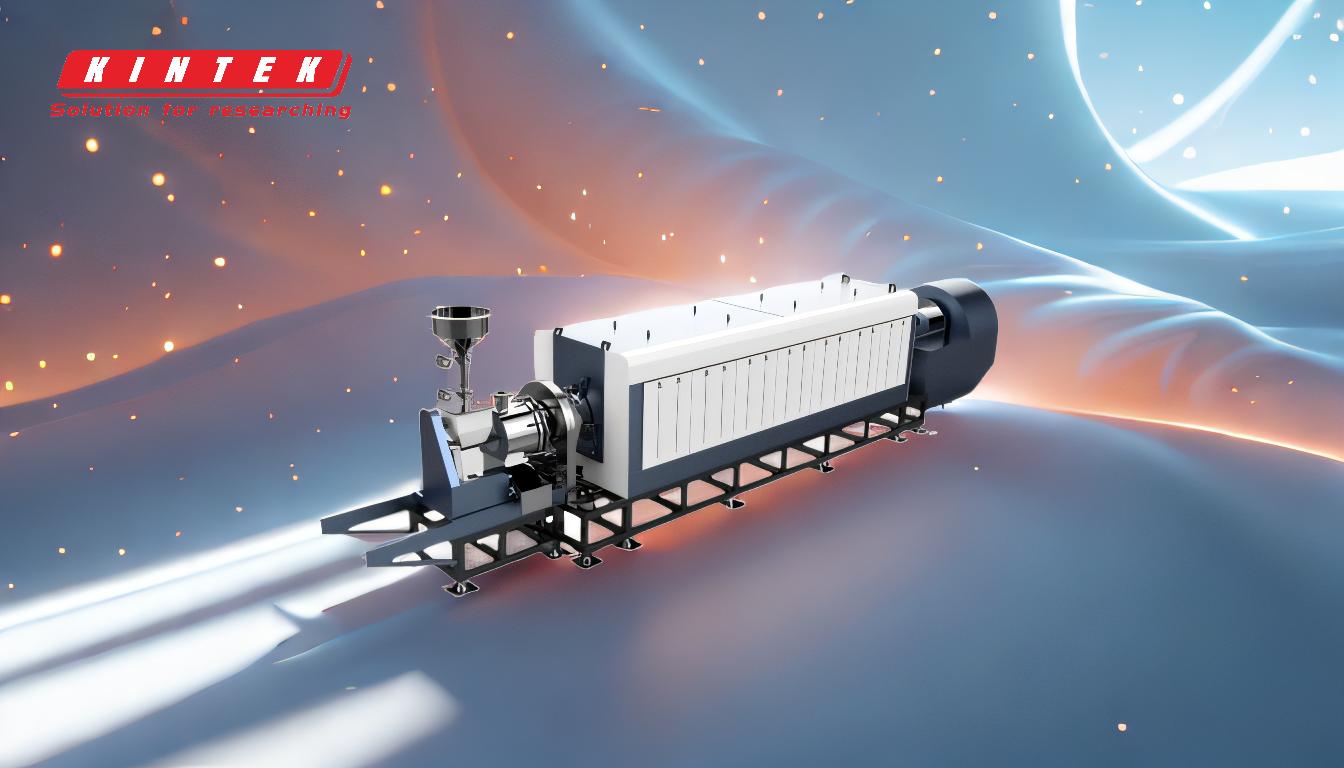
-
Definition and Purpose of Biochar:
- Biochar is a carbon-rich, black material produced through pyrolysis, a process that heats biomass in the absence of oxygen.
- It is used for carbon sequestration, as a soil amendment in agriculture, and as an additive in materials like concrete and plastic.
- Biochar is valued for its light, porous structure, which allows it to absorb contaminants, nutrients, water, and gases.
-
Types of Pyrolysis Processes:
- Slow Pyrolysis: Involves lower temperatures (around 400 °C) and longer residence times (several hours). It is the most common method for producing high-quality biochar for agricultural use due to its reliability and consistency.
- Fast Pyrolysis: Operates at higher temperatures and shorter residence times, producing more bio-oil and less biochar.
- Gasification: A process that converts biomass into syngas (a mixture of hydrogen and carbon monoxide) and a small amount of biochar.
-
Steps in Biochar Production:
-
Pre-treatment:
- Biomass is dried to reduce moisture content and crushed to a uniform size for efficient pyrolysis.
-
Pyrolysis:
- The biomass is heated in an oxygen-free environment. During slow pyrolysis, temperatures around 400 °C are maintained for several hours, leading to the decomposition of biomass into biochar and bio-gas.
-
Discharging:
- The biochar is cooled after pyrolysis to stabilize its structure and prepare it for use.
-
De-dusting:
- Exhaust gases are cleaned to remove harmful substances, ensuring environmental safety.
-
Pre-treatment:
-
Factors Influencing Biochar Quality:
- Feedstock: The type of biomass used (e.g., wood, agricultural residues) affects the biochar's properties.
- Pyrolysis Conditions: Temperature, heating rate, and residence time determine the biochar's porosity, carbon content, and stability.
- Post-processing: Conditioning and de-dusting can further refine the biochar's properties for specific applications.
-
Energy Considerations:
- The energy required for pyrolysis can be partially covered by combusting the gaseous byproducts (bio-gas), making the process more energy-efficient.
-
Applications of Biochar:
- Agriculture: Improves soil fertility, water retention, and nutrient availability.
- Carbon Sequestration: Stores carbon in a stable form, reducing greenhouse gas emissions.
- Industrial Uses: Used as an additive in materials like concrete and plastic, or as a replacement for fossil coal.
By following these steps and considerations, biochar can be effectively produced from biomass, offering a sustainable solution for waste management, carbon sequestration, and agricultural improvement.
Summary Table:
Aspect | Details |
---|---|
Definition | Carbon-rich material produced through pyrolysis of biomass. |
Production Methods | Slow pyrolysis, fast pyrolysis, gasification. |
Key Steps | Pre-treatment, pyrolysis, discharging, de-dusting. |
Applications | Agriculture, carbon sequestration, industrial uses. |
Benefits | Improves soil fertility, reduces emissions, enhances material properties. |
Discover how biochar can transform your agricultural and industrial processes—contact us today!