Biochar pyrolysis is a process that converts organic materials, such as agricultural waste, wood, or manure, into biochar through thermal decomposition in the absence of oxygen. This process is highly efficient for carbon sequestration, soil improvement, and waste management. The key steps involve selecting the right feedstock, using a pyrolysis reactor to heat the material, controlling temperature and oxygen levels, and collecting the resulting biochar. The process can be tailored to produce biochar with specific properties, depending on the feedstock and pyrolysis conditions. Below, we’ll break down the process into key steps and explain the critical factors involved.
Key Points Explained:
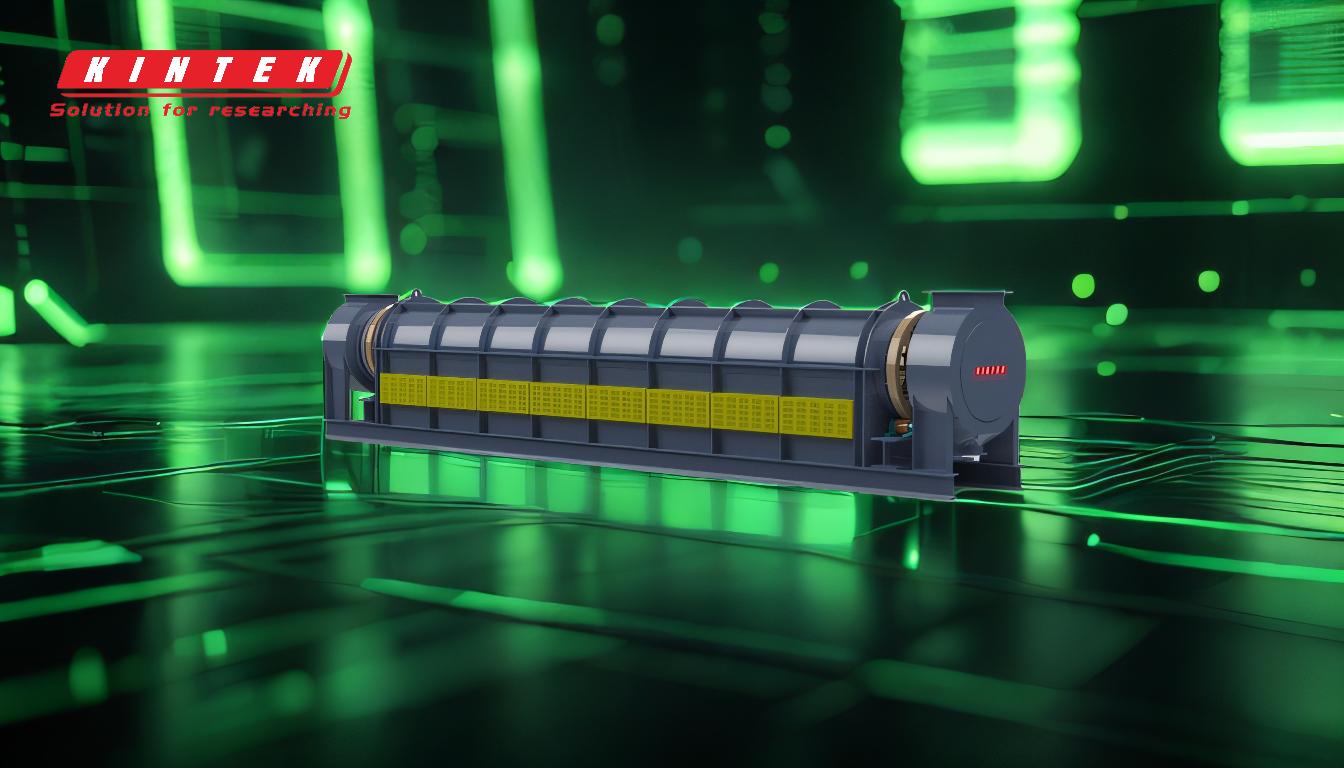
-
Feedstock Selection:
- The choice of feedstock is crucial as it determines the quality and properties of the biochar. Common feedstocks include wood chips, crop residues, manure, and other organic waste materials.
- Feedstocks with high lignin content, such as wood, tend to produce more stable biochar, while those with high cellulose content may yield biochar with different characteristics.
- The moisture content of the feedstock should ideally be below 20% to ensure efficient pyrolysis and reduce energy consumption.
-
Pyrolysis Reactor:
- A pyrolysis reactor is the core equipment used to heat the feedstock in the absence of oxygen. There are several types of reactors, including batch, continuous, and semi-continuous systems.
- The reactor design influences the heating rate, temperature control, and residence time, all of which affect the biochar yield and quality.
- Common reactor types include drum reactors, fluidized bed reactors, and retort systems. Each has its advantages depending on the scale and purpose of the operation.
-
Temperature Control:
- Pyrolysis typically occurs at temperatures between 300°C and 700°C. Lower temperatures (300°C–400°C) produce more biochar with higher volatile content, while higher temperatures (500°C–700°C) yield biochar with higher carbon content and stability.
- The heating rate also plays a role. Slow pyrolysis (low heating rates) maximizes biochar yield, while fast pyrolysis (high heating rates) favors the production of bio-oil and syngas.
-
Oxygen-Free Environment:
- Pyrolysis must occur in an oxygen-free or low-oxygen environment to prevent combustion. This is achieved by purging the reactor with inert gases like nitrogen or by sealing the reactor to exclude air.
- Maintaining an oxygen-free environment ensures that the organic material decomposes into biochar, bio-oil, and syngas rather than burning into ash.
-
Residence Time:
- Residence time refers to the duration the feedstock is exposed to pyrolysis conditions. Longer residence times generally result in more complete carbonization and higher biochar stability.
- The optimal residence time depends on the feedstock and reactor type but typically ranges from minutes to hours.
-
Biochar Collection and Cooling:
- After pyrolysis, the biochar must be cooled and collected. Rapid cooling can help preserve the biochar’s porous structure, which is beneficial for soil applications.
- The biochar may undergo additional processing, such as grinding or activation, to enhance its properties for specific uses.
-
Byproduct Management:
- Pyrolysis produces not only biochar but also bio-oil and syngas. These byproducts can be captured and used as energy sources or for other industrial applications.
- Proper management of byproducts is essential for maximizing the economic and environmental benefits of the pyrolysis process.
-
Applications of Biochar:
- Biochar is primarily used as a soil amendment to improve soil fertility, water retention, and carbon sequestration. It can also be used in water filtration, as a feed additive, or in industrial processes.
- The specific application depends on the biochar’s properties, which are influenced by the feedstock and pyrolysis conditions.
By carefully controlling these factors, biochar pyrolysis can be optimized to produce high-quality biochar tailored to specific needs. The process not only helps manage organic waste but also contributes to sustainable agriculture and climate change mitigation.
Summary Table:
Step | Key Details |
---|---|
1. Feedstock Selection | Choose organic materials like wood, crop residues, or manure with <20% moisture. |
2. Pyrolysis Reactor | Use batch, continuous, or semi-continuous reactors for efficient heating. |
3. Temperature Control | Maintain 300°C–700°C; lower temps yield more biochar, higher temps increase stability. |
4. Oxygen-Free Environment | Use inert gases or sealed reactors to prevent combustion. |
5. Residence Time | Adjust duration (minutes to hours) for optimal carbonization. |
6. Biochar Collection | Cool rapidly to preserve porous structure; grind or activate for specific uses. |
7. Byproduct Management | Capture bio-oil and syngas for energy or industrial use. |
8. Applications | Use biochar for soil improvement, water filtration, or industrial processes. |
Ready to optimize your biochar production? Contact our experts today for tailored solutions!