Infrared (IR) pellets are essential for sample analysis in spectroscopy, particularly for preparing solid samples in a form suitable for IR transmission measurements. The process involves several key steps, including milling or grinding the sample to achieve the desired fineness, mixing it with a binder, and compressing the mixture into a pellet using a die under high pressure. This method ensures a homogeneous and stable pellet that can be analyzed effectively.
Key Points Explained:
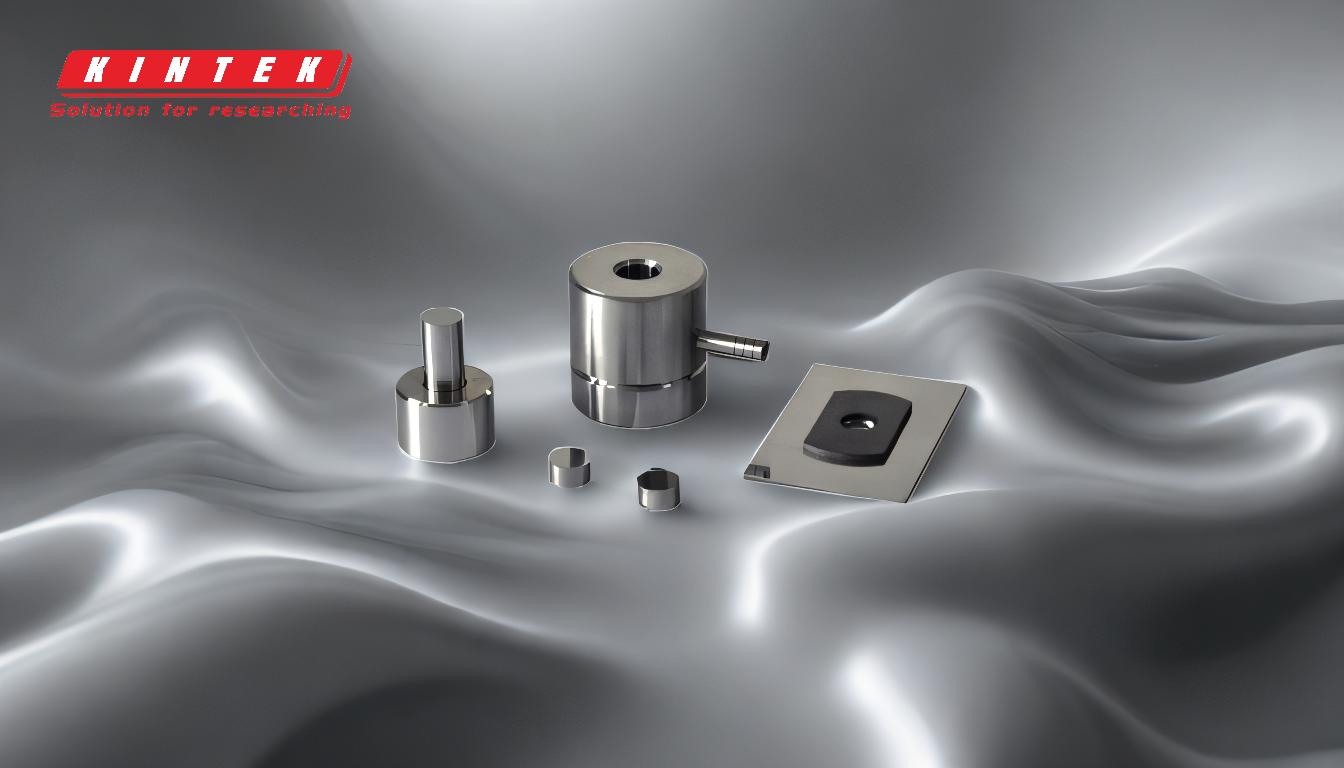
-
Milling/Grinding the Sample:
- The first step in making IR pellets is to ensure the sample is finely ground. This is crucial because the particle size of the sample affects the quality of the IR spectrum. Larger particles can scatter light, leading to poor spectral resolution.
- A ball mill or mortar and pestle can be used to grind the sample to a fine powder. The goal is to achieve a uniform particle size, typically in the micrometer range, to ensure even distribution in the pellet.
-
Mixing with a Binder:
- After grinding, the powdered sample is mixed with a binder. Commonly used binders include potassium bromide (KBr) or other x-ray powder materials. The binder acts as a matrix that holds the sample particles together and ensures transparency in the IR region.
- The typical ratio of sample to binder is around 1:100, meaning 1 mg of sample is mixed with 100 mg of binder. This ratio ensures that the sample is sufficiently diluted to avoid over-absorption of IR radiation.
-
Inserting the Mixture into a Pellet Die:
- The mixture of sample and binder is then placed into a pellet die. Pellet dies are specially designed to compress the powder into a solid, transparent disk.
- The die consists of a cylindrical cavity with a plunger that applies pressure to the mixture. The die must be clean and free of contaminants to avoid interference in the IR spectrum.
-
Compressing the Die:
- The final step is compressing the die under high pressure, typically between 15 and 40 tons. This pressure is necessary to form a solid, transparent pellet.
- The compression process should be done gradually to ensure even distribution of pressure and to avoid cracking or unevenness in the pellet. The resulting pellet should be thin (usually around 1-2 mm) and uniform in thickness.
-
Quality Control:
- After the pellet is formed, it should be inspected for clarity and uniformity. Any cracks, cloudiness, or unevenness can affect the IR spectrum.
- The pellet is then ready for IR spectroscopy analysis. It is placed in the spectrometer, and the IR beam is passed through the pellet to obtain the spectrum of the sample.
By following these steps, you can create high-quality IR pellets suitable for accurate and reliable spectroscopic analysis. The process requires precision and attention to detail to ensure the integrity of the sample and the quality of the resulting spectrum.
Summary Table:
Step | Details |
---|---|
1. Milling/Grinding | Grind sample to fine powder (micrometer range) using a ball mill or mortar. |
2. Mixing with Binder | Mix sample with binder (e.g., KBr) at a 1:100 ratio for transparency. |
3. Inserting into Die | Place mixture into a clean pellet die for compression. |
4. Compressing Die | Apply 15-40 tons of pressure to form a thin, transparent pellet. |
5. Quality Control | Inspect pellet for clarity, uniformity, and absence of cracks. |
Need help creating high-quality IR pellets? Contact our experts today for tailored guidance!