Melting metal in a crucible involves heating the metal inside a crucible until it reaches its melting point, using a crucible furnace. The furnace is typically powered by natural gas, propane, or electricity, and the crucible is made of refractory materials to withstand high temperatures. The process requires precise temperature control to ensure the metal melts uniformly without overheating. Once molten, the metal is poured into a mold or container to achieve the desired shape. The choice of crucible and furnace design depends on the type of metal being melted, its melting point, and the required volume.
Key Points Explained:
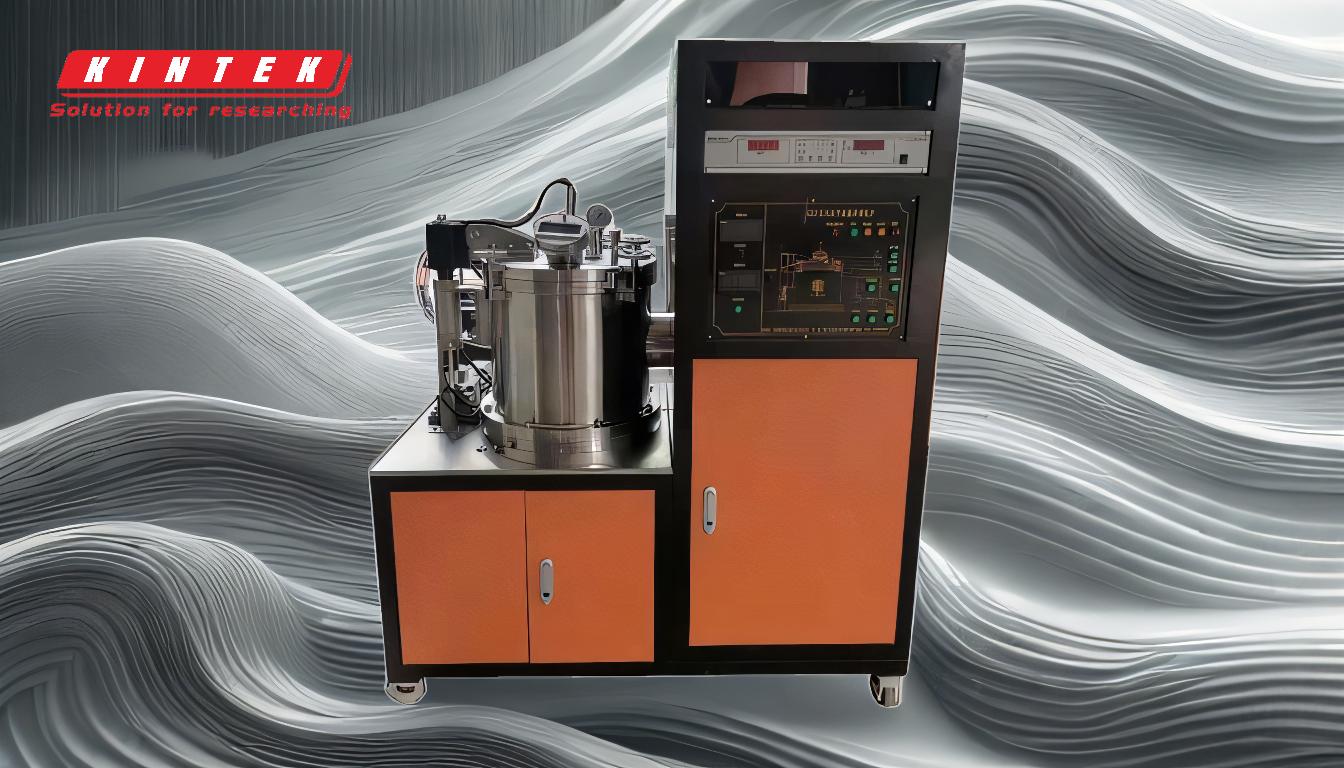
-
Understanding the Crucible Furnace:
- A crucible furnace is designed to melt metals by heating them inside a crucible until they reach their melting point.
- The furnace chamber is made of refractory materials to withstand high temperatures, and the crucible, which holds the metal, is placed inside this chamber.
- The furnace can be powered by natural gas, propane, or electricity, depending on the setup and the type of metal being melted.
-
Selecting the Right Crucible:
- Crucibles are made from materials that can withstand extreme temperatures and chemical reactions with molten metals.
- The choice of crucible depends on the type of metal being melted. For example, graphite crucibles are suitable for melting non-ferrous metals like aluminum, brass, and bronze, while clay-graphite crucibles are better for higher-temperature metals like cast iron.
- The size of the crucible should match the volume of metal to be melted, ensuring efficient heat transfer and uniform melting.
-
Heating the Crucible:
- The heating element of the furnace generates heat, which is transferred to the crucible and then to the metal inside.
- The temperature must be carefully controlled to ensure the metal reaches its melting point without overheating. Overheating can damage the crucible or cause the metal to degrade.
- A temperature control system is often used to monitor and adjust the heat, ensuring a consistent melting process.
-
Melting the Metal:
- As the crucible heats up, the metal inside begins to absorb the heat and eventually melts.
- The melting point varies depending on the type of metal. For example, aluminum melts at around 660°C (1220°F), while cast iron melts at approximately 1200°C (2192°F).
- Once the metal becomes molten, it is ready to be poured into a mold or container.
-
Pouring the Molten Metal:
- After the metal has fully melted, it is carefully poured into a mold or container to take the desired shape.
- Proper handling is crucial to avoid spills or accidents, as molten metal is extremely hot and can cause severe burns.
- The pouring process should be done quickly and efficiently to prevent the metal from cooling prematurely.
-
Safety Considerations:
- Melting metal in a crucible involves high temperatures and hazardous materials, so safety precautions are essential.
- Protective gear, such as heat-resistant gloves, aprons, and face shields, should be worn at all times.
- The workspace should be well-ventilated to avoid inhaling fumes, and a fire extinguisher should be readily available in case of emergencies.
-
Maintenance and Cleaning:
- After use, the crucible should be cleaned to remove any residual metal or slag.
- Regular maintenance of the furnace and crucible is necessary to ensure their longevity and efficiency.
- Inspect the crucible for cracks or damage before each use, as a damaged crucible can fail during the melting process, leading to dangerous situations.
-
Applications of Crucible Melting:
- Crucible furnaces are commonly used in small-scale metal casting, jewelry making, and laboratory settings.
- They are ideal for melting metals with low to medium melting points, such as aluminum, brass, bronze, and precious metals.
- The process is also used in foundries for producing small batches of castings or for specialized alloys.
By following these steps and considerations, you can effectively melt metal in a crucible while ensuring safety and achieving the desired results.
Summary Table:
Step | Key Considerations |
---|---|
1. Crucible Furnace Setup | Choose a furnace powered by natural gas, propane, or electricity. |
2. Selecting the Crucible | Use graphite for non-ferrous metals, clay-graphite for higher-temperature metals. |
3. Heating the Crucible | Ensure precise temperature control to avoid overheating and damage. |
4. Melting the Metal | Monitor the metal's melting point (e.g., aluminum: 660°C, cast iron: 1200°C). |
5. Pouring Molten Metal | Pour quickly into molds to prevent premature cooling. |
6. Safety Precautions | Wear protective gear, ensure ventilation, and keep a fire extinguisher nearby. |
7. Maintenance & Cleaning | Clean crucibles after use and inspect for damage regularly. |
8. Applications | Ideal for jewelry making, small-scale casting, and laboratory use. |
Ready to melt metal safely and efficiently? Contact our experts today for personalized advice!