Wood pellets are a type of biomass fuel made from compressed wood or other organic materials. They are widely used for heating, cooking, and even as animal bedding. The process of pressing wood pellets involves several steps, including raw material preparation, drying, grinding, pelletizing, cooling, and packaging. Each step is crucial to ensure the quality and efficiency of the final product. The key to successful pellet production lies in selecting the right raw materials, maintaining proper moisture content, and using high-quality pelletizing equipment. Below is a detailed explanation of the process and key considerations.
Key Points Explained:
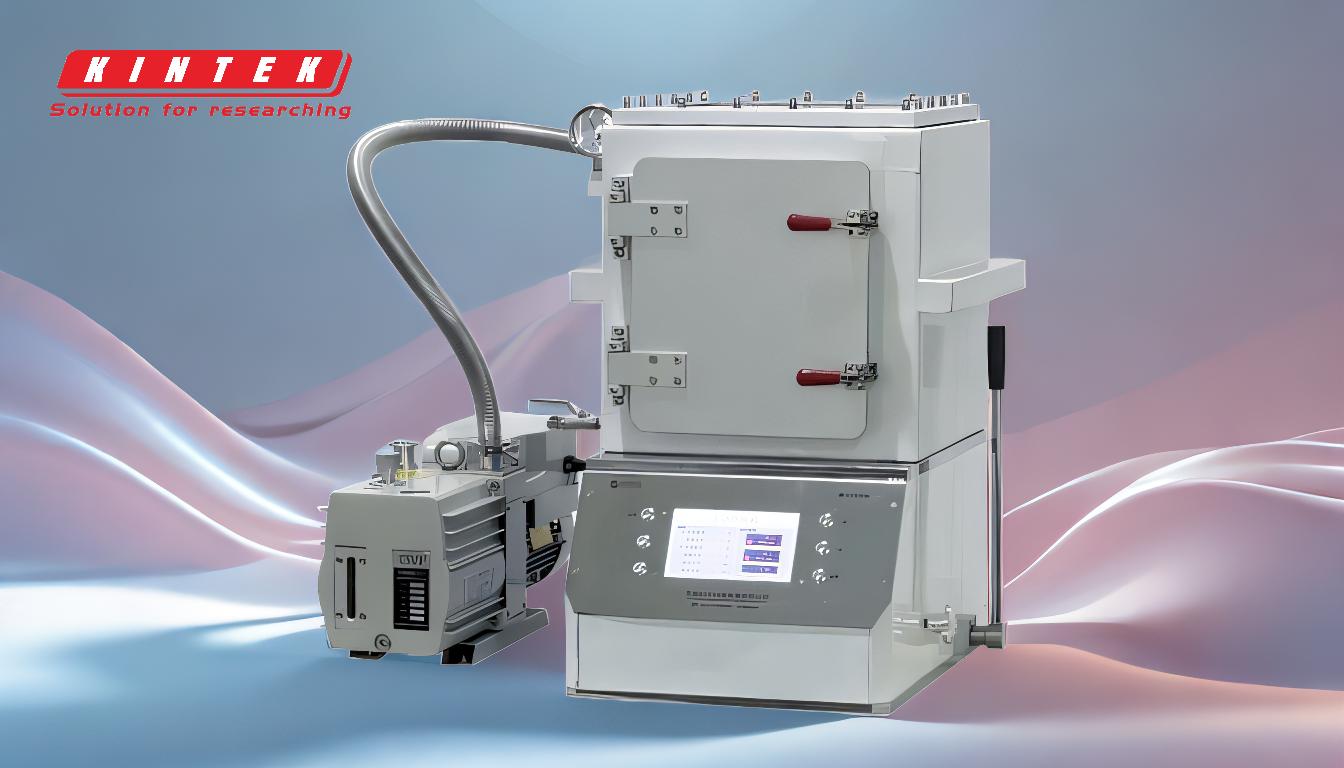
-
Raw Material Selection and Preparation:
- Material Types: Wood pellets can be made from various raw materials, including sawdust, wood shavings, wood chips, and even agricultural residues like straw or corn stalks. Hardwoods and softwoods are both suitable, but hardwoods generally produce denser pellets.
- Preparation: The raw material must be clean and free from contaminants like metal, stones, or plastic. It is then reduced to a uniform size, typically through chipping or grinding, to ensure consistent pellet quality.
-
Drying the Raw Material:
- Moisture Content: The ideal moisture content for pelletizing is between 10% and 15%. Excess moisture can lead to poor pellet quality, while insufficient moisture can make the material difficult to compress.
- Drying Process: A rotary dryer or belt dryer is commonly used to reduce the moisture content. Proper drying ensures the material binds well during pelletizing.
-
Grinding the Material:
- Particle Size: After drying, the material is further ground into a fine powder. The particle size should be small enough to pass through a 3-5 mm sieve. This step ensures uniformity and improves the efficiency of the pelletizing process.
-
Pelletizing:
- Pellet Mill: The ground material is fed into a pellet mill, where it is compressed under high pressure and forced through a die with small holes. The friction and heat generated during this process cause the lignin in the wood to soften and act as a natural binder.
- Die and Roller Design: The die and rollers are critical components of the pellet mill. The die determines the size and shape of the pellets, while the rollers apply the necessary pressure. Proper maintenance of these parts is essential for consistent pellet quality.
-
Cooling and Screening:
- Cooling: Freshly pressed pellets are hot and soft, so they need to be cooled to harden and stabilize. A pellet cooler, often a counterflow cooler, is used to reduce the temperature and moisture content.
- Screening: After cooling, the pellets are screened to remove fines and broken pieces. This ensures only high-quality pellets are packaged and sold.
-
Packaging and Storage:
- Packaging: The final pellets are typically packaged in bags or stored in bulk. Proper packaging protects the pellets from moisture and contamination.
- Storage: Pellets should be stored in a dry, well-ventilated area to maintain their quality and prevent degradation.
-
Quality Control:
- Density and Durability: High-quality pellets should have a high density and durability to withstand handling and transportation without breaking.
- Ash Content and Calorific Value: The ash content should be low, and the calorific value should be high to ensure efficient combustion.
-
Environmental and Economic Considerations:
- Sustainability: Using waste wood or sustainable forestry practices ensures the environmental friendliness of wood pellets.
- Cost Efficiency: Proper equipment selection and maintenance can reduce production costs and improve profitability.
By following these steps and considerations, wood pellets can be efficiently and effectively produced, providing a sustainable and renewable energy source.
Summary Table:
Step | Key Details |
---|---|
Raw Material Prep | Clean, uniform size; hardwoods preferred for denser pellets. |
Drying | Moisture content: 10-15%; rotary or belt dryer used. |
Grinding | Ground to 3-5 mm particle size for uniformity. |
Pelletizing | High-pressure compression in pellet mill; die and roller design critical. |
Cooling & Screening | Cooled to harden; screened to remove fines and broken pieces. |
Packaging & Storage | Packaged in bags or bulk; stored in dry, ventilated areas. |
Quality Control | High density, durability, low ash content, and high calorific value. |
Sustainability | Uses waste wood or sustainable practices; cost-efficient production. |
Ready to produce high-quality wood pellets? Contact our experts today for tailored solutions!