Recycling rubber waste involves a variety of methods depending on the type of rubber and its intended reuse. Common techniques include cryogenic grinding, which freezes the rubber in liquid nitrogen before crushing it into fine particles, and mechanical grinding, which reduces rubber waste into smaller pieces. Other methods include restructuring waste tires into new products, using them as fuel through thermal decomposition, or blending them with other materials for civil engineering applications. The choice of method depends on the desired end product, whether it be rubber crumbs, powder, or composite materials. Each method has its own advantages and challenges, but all aim to reduce environmental impact and promote sustainability.
Key Points Explained:
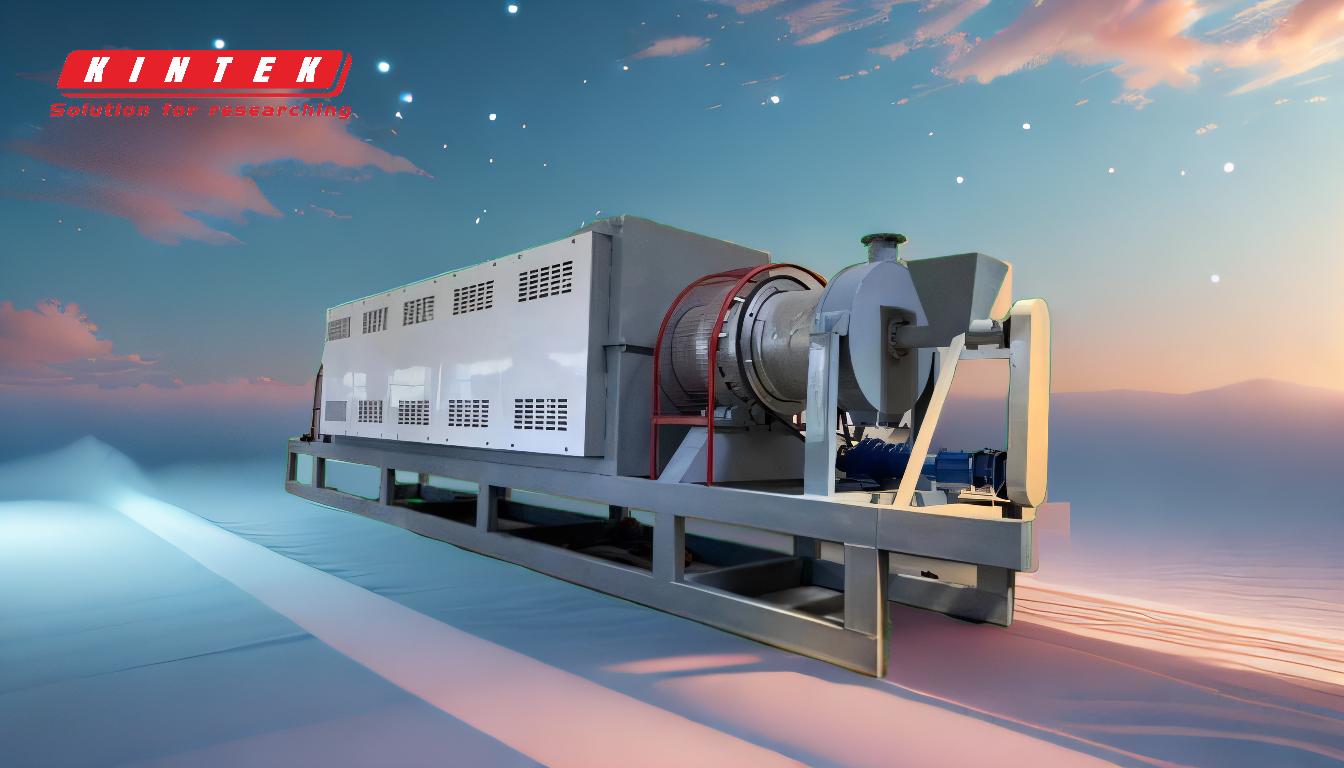
-
Cryogenic Grinding:
- Process: Rubber waste, such as discarded gloves or tires, is soaked in liquid nitrogen until it becomes brittle. It is then crushed using a cryogenic crusher to produce fine rubber crumbs.
- Advantages: This method is efficient for producing uniform particles with a large surface area, which is ideal for blending with other materials or for use in industrial applications.
- Applications: Commonly used for recycling rubber gloves, tires, and other elastomeric materials.
-
Mechanical Grinding:
- Process: Rubber waste is mechanically ground at ambient temperatures to reduce its size. This can involve ambient, wet, or cryogenic grinding technologies.
- Advantages: Mechanical grinding is versatile and can handle a wide range of rubber waste types. It is less energy-intensive compared to cryogenic grinding.
- Applications: Produces ground tire rubber (GTR) used in asphalt, concrete, or as a filler in polymeric matrices.
-
Restructuring and Retreading:
- Process: Waste tires are restructured into new products or retreaded to extend their lifespan. This involves removing damaged treads and applying new ones.
- Advantages: Reduces the need for new raw materials and extends the life of tires, making it an environmentally friendly option.
- Applications: Retreaded tires are used in commercial vehicles, while restructured rubber can be used in construction or industrial applications.
-
Energy Recovery:
- Process: Waste tires are subjected to high-temperature heating or thermal decomposition to produce oil, combustible gas, or carbon.
- Advantages: Converts non-recyclable rubber waste into usable energy sources, reducing landfill dependency.
- Applications: Used in energy-intensive industries as an alternative fuel source.
-
Civil Engineering Applications:
- Process: Rubber waste is used as a filler in civil engineering materials like concrete, asphalt, or polymeric matrices.
- Advantages: Enhances the durability and flexibility of construction materials while recycling rubber waste.
- Applications: Commonly used in road construction, building materials, and composite products.
-
Powder Production:
- Process: Rubber waste is ground into fine powder, which can be blended with other materials or used as a raw material in manufacturing.
- Advantages: Provides a versatile material for various industrial applications, including coatings, adhesives, and composites.
- Applications: Used in the production of rubber-based products, such as mats, seals, and gaskets.
-
Separation of Materials:
- Process: Metallic and textile components are separated from rubber waste before processing.
- Advantages: Ensures that only rubber is processed, improving the quality of the recycled material.
- Applications: Essential for recycling tires, which contain steel belts and fabric layers.
-
Environmental and Economic Benefits:
- Reduction in Landfill Waste: Recycling rubber waste reduces the volume of material sent to landfills, mitigating environmental pollution.
- Resource Conservation: Reusing rubber waste conserves natural resources by reducing the demand for virgin rubber.
- Cost Savings: Recycling methods can be cost-effective compared to producing new rubber, especially when energy recovery or civil engineering applications are employed.
By understanding these key points, equipment and consumable purchasers can make informed decisions about the most suitable recycling methods for their specific needs, balancing environmental impact, cost, and application requirements.
Summary Table:
Method | Process | Advantages | Applications |
---|---|---|---|
Cryogenic Grinding | Freezes rubber in liquid nitrogen, then crushes into fine particles | Produces uniform particles; ideal for blending with other materials | Recycling gloves, tires, and elastomeric materials |
Mechanical Grinding | Grinds rubber at ambient temperatures to reduce size | Versatile, less energy-intensive, handles various rubber types | Produces ground tire rubber for asphalt, concrete, or polymeric matrices |
Restructuring | Restructures or retreads waste tires to extend lifespan | Reduces raw material demand; environmentally friendly | Retreaded tires for commercial vehicles; restructured rubber for construction |
Energy Recovery | High-temperature heating or thermal decomposition of rubber waste | Converts non-recyclable rubber into usable energy; reduces landfill dependency | Used as alternative fuel in energy-intensive industries |
Civil Engineering | Uses rubber waste as filler in construction materials | Enhances durability and flexibility of materials | Road construction, building materials, and composite products |
Powder Production | Grinds rubber waste into fine powder for blending or manufacturing | Provides versatile material for industrial applications | Used in coatings, adhesives, and rubber-based products |
Separation | Separates metallic and textile components from rubber waste | Improves recycled material quality | Essential for recycling tires with steel belts and fabric layers |
Ready to implement sustainable rubber recycling solutions? Contact us today to learn more!