Sintering tungsten carbide is a complex process that transforms powdered tungsten carbide into a dense, durable material through controlled heating and cooling. The process typically involves four main stages: removal of the molding agent and pre-burning, solid-phase sintering, liquid-phase sintering, and cooling. Each stage is critical for achieving the desired properties, such as hardness, toughness, and wear resistance. The process begins with powder preparation, blending, and compacting, followed by sintering in a controlled environment. The final product is a dense, homogeneous structure where tungsten carbide grains are fused into a cobalt matrix.
Key Points Explained:
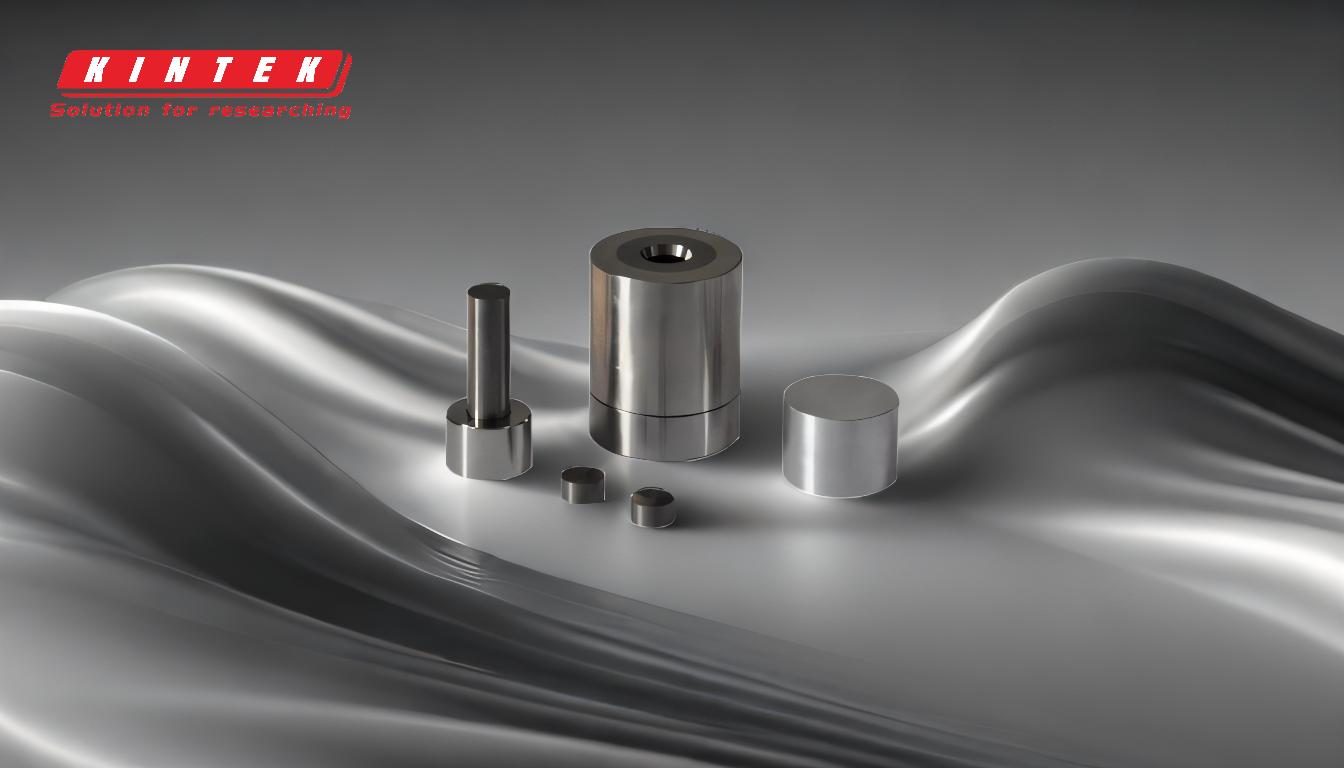
-
Powder Preparation and Blending:
- Tungsten carbide sintering starts with the preparation of fine tungsten carbide powder, often mixed with a binder like cobalt to enhance properties such as toughness.
- The powders are blended to ensure a uniform mixture, which is crucial for achieving consistent material properties in the final product.
-
Compacting:
- The blended powder is compacted into the desired shape using techniques like pressing or injection molding. This stage forms the "green" material, which is soft and not yet sintered.
- Proper compaction ensures the material retains its shape during sintering and achieves the required density.
-
Removal of Molding Agent and Pre-Burning:
- In this stage, the green material is heated to remove any molding agents or binders used during compacting. This process is essential to prevent defects in the final product.
- Pre-burning also helps in stabilizing the material before it undergoes higher-temperature sintering.
-
Solid-Phase Sintering:
- The material is heated to a temperature below its melting point, typically around 1,000°C to 1,300°C. During this stage, the particles bond through solid-state diffusion, forming a porous structure.
- This stage is critical for achieving initial densification and strength.
-
Liquid-Phase Sintering:
- The temperature is increased further, often to around 1,400°C to 1,500°C, causing the cobalt binder to melt and form a liquid phase.
- The liquid phase facilitates the rearrangement of tungsten carbide particles, filling voids and creating a dense, homogeneous structure.
- This stage is essential for achieving the final hardness and wear resistance of the material.
-
Cooling Stage:
- After sintering, the material is slowly cooled to room temperature. Controlled cooling prevents thermal stresses and ensures the material retains its desired properties.
- The cooling rate can influence the microstructure and mechanical properties of the final product.
-
Role of Cobalt Matrix:
- Cobalt acts as a binder, holding the tungsten carbide grains together. The amount of cobalt used affects the material's hardness and toughness.
- The sintering process ensures the cobalt matrix is evenly distributed, providing a balance between hardness and durability.
-
Importance of Controlled Environment:
- Sintering is typically performed in a controlled atmosphere, such as vacuum or inert gas, to prevent oxidation and contamination.
- A controlled environment ensures the material's purity and consistency.
-
Applications of Sintered Tungsten Carbide:
- Sintered tungsten carbide is widely used in cutting tools, wear-resistant parts, and industrial machinery due to its exceptional hardness and durability.
- The sintering process allows for the production of complex shapes with precise dimensions and properties.
-
Use of Tungsten Coil in Sintering:
- In some sintering processes, a tungsten coil may be used as a heating element due to its high melting point and resistance to oxidation.
- The tungsten coil provides uniform heating, which is essential for achieving consistent sintering results.
By carefully controlling each stage of the sintering process, manufacturers can produce high-quality tungsten carbide materials with tailored properties for specific applications. Understanding the role of each stage and the importance of factors like temperature, atmosphere, and cooling rate is crucial for achieving the desired results.
Summary Table:
Stage | Description | Key Details |
---|---|---|
Powder Preparation & Blending | Mixing tungsten carbide powder with cobalt binder | Ensures uniform mixture for consistent material properties |
Compacting | Pressing or molding blended powder into shape | Forms 'green' material, retains shape during sintering |
Removal of Molding Agent | Heating to remove binders and prevent defects | Stabilizes material before high-temperature sintering |
Solid-Phase Sintering | Heating to 1,000°C–1,300°C for particle bonding | Forms porous structure, initial densification |
Liquid-Phase Sintering | Heating to 1,400°C–1,500°C to melt cobalt binder | Creates dense, homogeneous structure for hardness and wear resistance |
Cooling | Controlled cooling to room temperature | Prevents thermal stresses, ensures desired properties |
Applications | Cutting tools, wear-resistant parts, industrial machinery | Produces complex shapes with precise dimensions |
Need expert advice on sintering tungsten carbide? Contact us today to optimize your process!