An electron beam evaporator is a sophisticated tool used in thin-film deposition processes, particularly in industries like semiconductor manufacturing, optics, and nanotechnology. It works by generating a focused beam of high-energy electrons to heat and evaporate a target material, which then condenses onto a substrate to form a thin, uniform layer. The process involves several key components and steps, including electron beam generation, material heating, and deposition. This method offers precise control over film thickness, uniformity, and purity, making it ideal for applications requiring high-quality coatings. Below, the key points of how an electron beam evaporator works are explained in detail.
Key Points Explained:
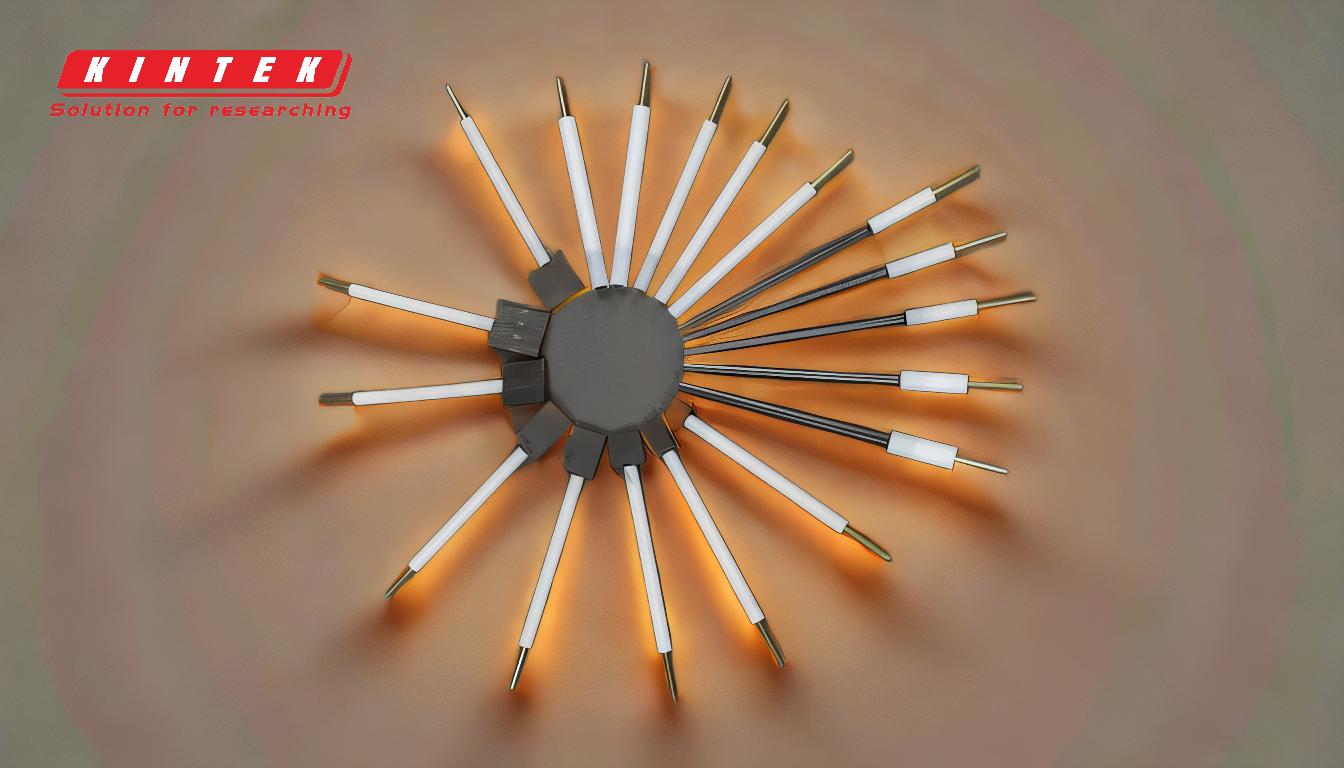
-
Electron Beam Generation:
- The core of the electron beam evaporator is the electron gun, which generates a high-energy electron beam. This is achieved by heating a filament (cathode) to emit electrons through thermionic emission.
- The electrons are then accelerated towards the target material using a high-voltage electric field, typically in the range of several kilovolts.
- Magnetic or electrostatic lenses focus the electron beam into a fine, concentrated spot on the target material, ensuring precise heating.
-
Material Heating and Evaporation:
- The focused electron beam strikes the target material, transferring its kinetic energy as heat. This localized heating causes the material to melt and eventually evaporate.
- The target material is often placed in a crucible, which is designed to withstand high temperatures and prevent contamination.
- The evaporation process occurs in a high-vacuum environment to minimize interactions with gas molecules, ensuring a pure and controlled deposition.
-
Deposition onto Substrate:
- The evaporated material forms a vapor cloud, which travels through the vacuum chamber and condenses onto a substrate placed above the target.
- The substrate is typically rotated or moved to ensure uniform coating thickness across its surface.
- The deposition rate and thickness are controlled by adjusting parameters such as electron beam power, target material properties, and substrate temperature.
-
Advantages of Electron Beam Evaporation:
- High Purity: The high-vacuum environment and localized heating minimize contamination, resulting in high-purity films.
- Precision Control: The ability to focus the electron beam allows for precise control over the deposition process, enabling the creation of ultra-thin and uniform coatings.
- Versatility: A wide range of materials, including metals, ceramics, and semiconductors, can be evaporated using this method.
- High Deposition Rates: The intense energy of the electron beam enables rapid heating and evaporation, making the process efficient for industrial applications.
-
Applications:
- Semiconductors: Used for depositing thin films in the fabrication of integrated circuits and other electronic components.
- Optics: Ideal for creating anti-reflective coatings, mirrors, and other optical components.
- Nanotechnology: Enables the deposition of nanoscale films for advanced materials research.
- Decorative Coatings: Used in industries like jewelry and automotive for applying durable and aesthetically pleasing coatings.
-
Challenges and Considerations:
- Complexity: The equipment and process are highly specialized, requiring skilled operation and maintenance.
- Cost: High initial investment and operational costs due to the need for high-vacuum systems and precision components.
- Material Limitations: Some materials may decompose or react under the intense heat of the electron beam, limiting their use in this process.
In summary, an electron beam evaporator is a powerful tool for thin-film deposition, offering unparalleled precision, purity, and versatility. Its operation relies on the generation of a focused electron beam to heat and evaporate target materials, which are then deposited onto substrates in a controlled, high-vacuum environment. While the process involves significant complexity and cost, its benefits make it indispensable in advanced manufacturing and research applications.
Summary Table:
Key Aspect | Details |
---|---|
Electron Beam Generation | High-energy electrons generated by an electron gun, focused using lenses. |
Material Heating | Localized heating via electron beam melts and evaporates target material. |
Deposition Process | Evaporated material condenses onto a substrate in a high-vacuum environment. |
Advantages | High purity, precision control, versatility, and high deposition rates. |
Applications | Semiconductors, optics, nanotechnology, and decorative coatings. |
Challenges | High complexity, cost, and material limitations. |
Interested in enhancing your thin-film deposition process? Contact us today to learn more about electron beam evaporators!