An induction forge, also known as an induction furnace, operates on the principle of electromagnetic induction to heat and melt metals. It works by converting electrical energy into heat energy without direct contact between the heating element (induction coil) and the metal. The process involves generating a high-frequency alternating current (AC) that flows through a copper coil, creating a rapidly reversing magnetic field. This magnetic field induces eddy currents within the conductive metal, generating heat through resistance (Joule heating). In ferromagnetic materials, additional heat is produced by magnetic hysteresis. The system is efficient, precise, and capable of melting a wide range of metals, including steel, copper, and aluminum, while maintaining compactness and energy efficiency.
Key Points Explained:
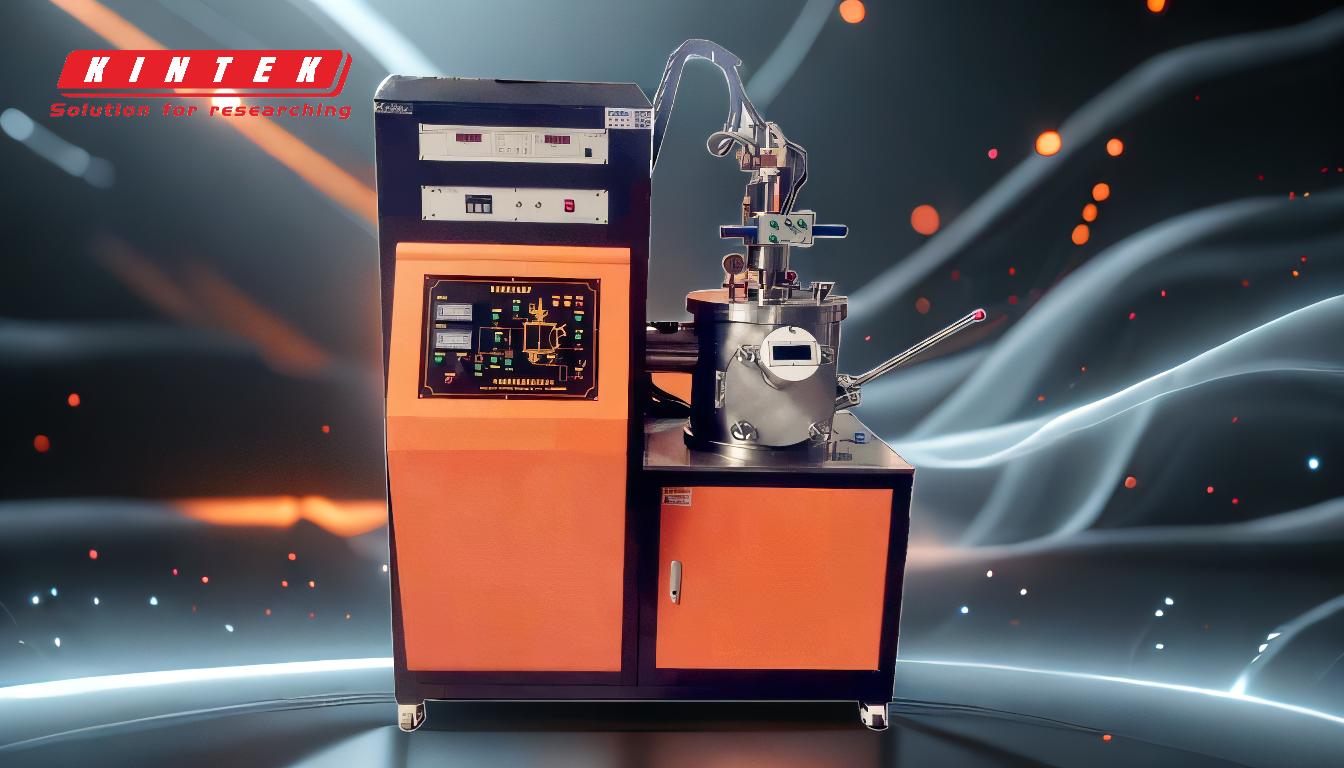
-
Electromagnetic Induction:
- The core principle behind an induction forge is electromagnetic induction. When an alternating current flows through the induction coil, it creates a rapidly changing magnetic field.
- This magnetic field penetrates the metal placed inside the coil, inducing eddy currents within the metal due to Faraday's law of induction.
-
Eddy Currents and Joule Heating:
- The induced eddy currents flow through the metal, encountering resistance. According to Joule's law, this resistance converts electrical energy into heat energy, raising the temperature of the metal.
- The heat generated is proportional to the square of the current and the resistance of the metal, ensuring efficient heating.
-
Magnetic Hysteresis (for Ferromagnetic Materials):
- In ferromagnetic materials like iron, additional heating occurs due to magnetic hysteresis. The alternating magnetic field causes the magnetic domains in the material to continuously realign, generating heat as a byproduct.
- This effect is most pronounced at lower frequencies and diminishes as the material reaches its Curie temperature.
-
Frequency Conversion:
- Induction forges typically operate at medium frequencies (300 Hz to 1000 Hz). The power supply converts standard 50 Hz or 60 Hz AC power into this higher frequency range.
- This conversion involves rectifying the AC into direct current (DC) and then inverting it back into adjustable medium-frequency AC using an inverter circuit.
-
Induction Coil and Magnetic Field:
- The induction coil, usually made of copper, is a critical component. It carries the high-frequency AC and generates the magnetic field necessary for induction heating.
- The coil is often water-cooled to prevent overheating and maintain efficiency during prolonged operation.
-
Non-Contact Heating:
- Unlike traditional furnaces, induction forges do not require direct contact between the heat source and the metal. This eliminates contamination and allows for precise temperature control.
- The non-contact nature also reduces wear and tear on the equipment, extending its lifespan.
-
Crucible and Metal Charge:
- The metal to be melted is placed inside a non-conductive crucible, which is surrounded by the induction coil.
- The crucible material must withstand high temperatures and not interfere with the electromagnetic process.
-
Applications and Advantages:
- Induction forges are widely used in melting carbon steel, alloy steel, special steel, and non-ferrous metals like copper, aluminum, lead, and zinc.
- They are compact, lightweight, energy-efficient, and capable of rapid melting with precise temperature control, making them ideal for industrial and small-scale applications.
-
Energy Efficiency and Productivity:
- Induction forges are highly energy-efficient because they directly heat the metal, minimizing heat loss to the surroundings.
- The rapid heating and melting process increases productivity, making them suitable for high-volume operations.
-
Safety and Environmental Benefits:
- The absence of open flames or combustion gases reduces the risk of accidents and environmental pollution.
- The enclosed design of the furnace also minimizes exposure to harmful fumes and particulates.
By leveraging these principles, induction forges provide a clean, efficient, and precise method for heating and melting metals, making them indispensable in modern metallurgy and manufacturing processes.
Summary Table:
Key Aspect | Details |
---|---|
Principle | Electromagnetic induction generates heat through eddy currents and hysteresis. |
Heating Method | Non-contact heating via induction coil, eliminating contamination. |
Frequency Range | Medium frequency (300 Hz to 1000 Hz) for efficient heating. |
Materials Heated | Steel, copper, aluminum, lead, zinc, and other metals. |
Advantages | Compact, energy-efficient, rapid melting, precise temperature control. |
Applications | Industrial and small-scale metal melting, high-volume operations. |
Safety Benefits | No open flames, reduced environmental pollution, enclosed design. |
Discover how an induction forge can revolutionize your metalworking process—contact us today to learn more!