An induction furnace melts metal by using electromagnetic induction to generate heat within the metal itself. This process involves passing an alternating current through a coil, which creates a rapidly changing magnetic field. When a conductive metal is placed inside this field, eddy currents are induced within the metal, causing it to heat up and eventually melt. The efficiency and speed of melting depend on factors such as the power input, the type of metal, and the design of the furnace. Modern induction furnaces, especially those using IGBT induction furnace technology, offer precise control over the melting process, making them highly efficient for industrial applications.
Key Points Explained:
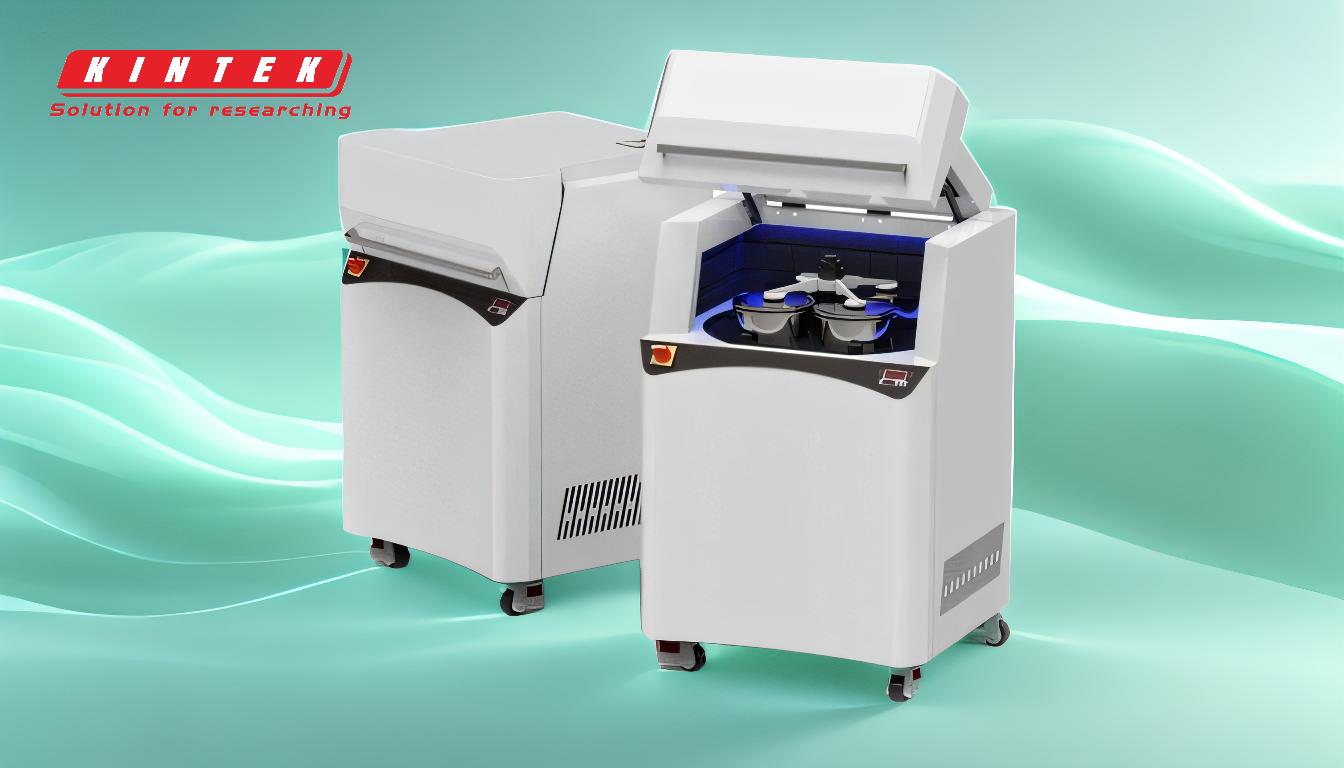
-
Principle of Electromagnetic Induction:
- Induction furnaces operate on the principle of electromagnetic induction. An alternating current (AC) is passed through a coil, creating a magnetic field. When a conductive metal is placed within this field, eddy currents are induced in the metal, generating heat due to electrical resistance. This heat is sufficient to melt the metal.
-
Role of the Coil and Magnetic Field:
- The coil, often made of copper, is a critical component of the induction furnace. The alternating current in the coil produces a rapidly changing magnetic field. This field penetrates the metal, inducing eddy currents that heat the metal from within. The efficiency of this process depends on the frequency of the alternating current and the design of the coil.
-
Factors Influencing the Melting Process:
- Temperature: The melting point of the metal determines the required temperature. Induction furnaces can reach very high temperatures, making them suitable for melting a wide range of metals.
- Pressure: While pressure is not a significant factor in induction melting, the absence of atmospheric contaminants is crucial for maintaining metal purity.
- Impurities and Slags: The presence of impurities can affect the melting process. Induction furnaces often include mechanisms to remove slags and impurities, ensuring a cleaner melt.
- Oxidants: The absence of oxidants is essential to prevent oxidation of the metal during the melting process. Induction furnaces typically operate in a controlled atmosphere to minimize oxidation.
-
Calculation of Melting Rate:
- The melting rate in an induction furnace can be calculated using the formula: [ \text{Melting Rate (kg/hour)} = \frac{\text{Power (kW)}}{\text{Standard Power Consumption (kWh/ton)}} ]
- For example, if the furnace operates at 325 kW and the standard power consumption is 0.625 kWh/kg, the melting rate would be: [ \frac{325 \text{ kW}}{0.625 \text{ kWh/kg}} = 520 \text{ kg/hour} ]
- This formula helps in determining the efficiency and capacity of the furnace for specific metals.
-
Advantages of IGBT Induction Furnaces:
- Precision Control: IGBT induction furnace technology allows for precise control over the power input, leading to better temperature regulation and energy efficiency.
- Energy Efficiency: IGBT-based furnaces are more energy-efficient compared to traditional induction furnaces, reducing operational costs.
- Compact Design: These furnaces are often more compact, making them suitable for a variety of industrial settings.
- Reduced Maintenance: The advanced technology in IGBT induction furnaces results in lower maintenance requirements and longer operational life.
-
Applications of Induction Furnaces:
- Induction furnaces are widely used in industries for melting metals such as steel, iron, aluminum, and copper. They are particularly valued for their ability to produce high-quality melts with minimal contamination, making them ideal for precision casting and alloy production.
In summary, induction furnaces, especially those utilizing IGBT induction furnace technology, offer a highly efficient and controlled method for melting metals. The process relies on electromagnetic induction to generate heat within the metal, ensuring a clean and precise melt. Factors such as temperature, impurities, and power input play crucial roles in determining the efficiency and quality of the melting process.
Summary Table:
Key Aspect | Details |
---|---|
Principle | Electromagnetic induction generates heat within the metal via eddy currents. |
Coil Role | Copper coil creates a magnetic field, inducing heat in the metal. |
Melting Factors | Temperature, impurities, oxidants, and power input affect melting efficiency. |
Melting Rate Formula | Melting Rate (kg/hour) = Power (kW) / Standard Power Consumption (kWh/kg). |
IGBT Furnace Advantages | Precise control, energy efficiency, compact design, and reduced maintenance. |
Applications | Used for melting steel, iron, aluminum, and copper in industrial settings. |
Ready to enhance your metal melting process? Contact us today to learn more about induction furnaces!