Chemical vapor deposition (CVD) is a widely used method for producing high-quality graphene. It involves the reaction of gaseous precursors, such as methane (CH₄), in a controlled environment to deposit a thin layer of graphene onto a substrate. The process typically occurs in a vacuum or low-pressure environment, which helps in controlling the reaction kinetics and ensuring uniform deposition. CVD is particularly advantageous for producing monolayer graphene over large areas, making it suitable for industrial applications. The process leverages the principles of thermal decomposition and surface adsorption, where carbon atoms from the precursor gas are deposited onto a substrate, forming a graphene layer.
Key Points Explained:
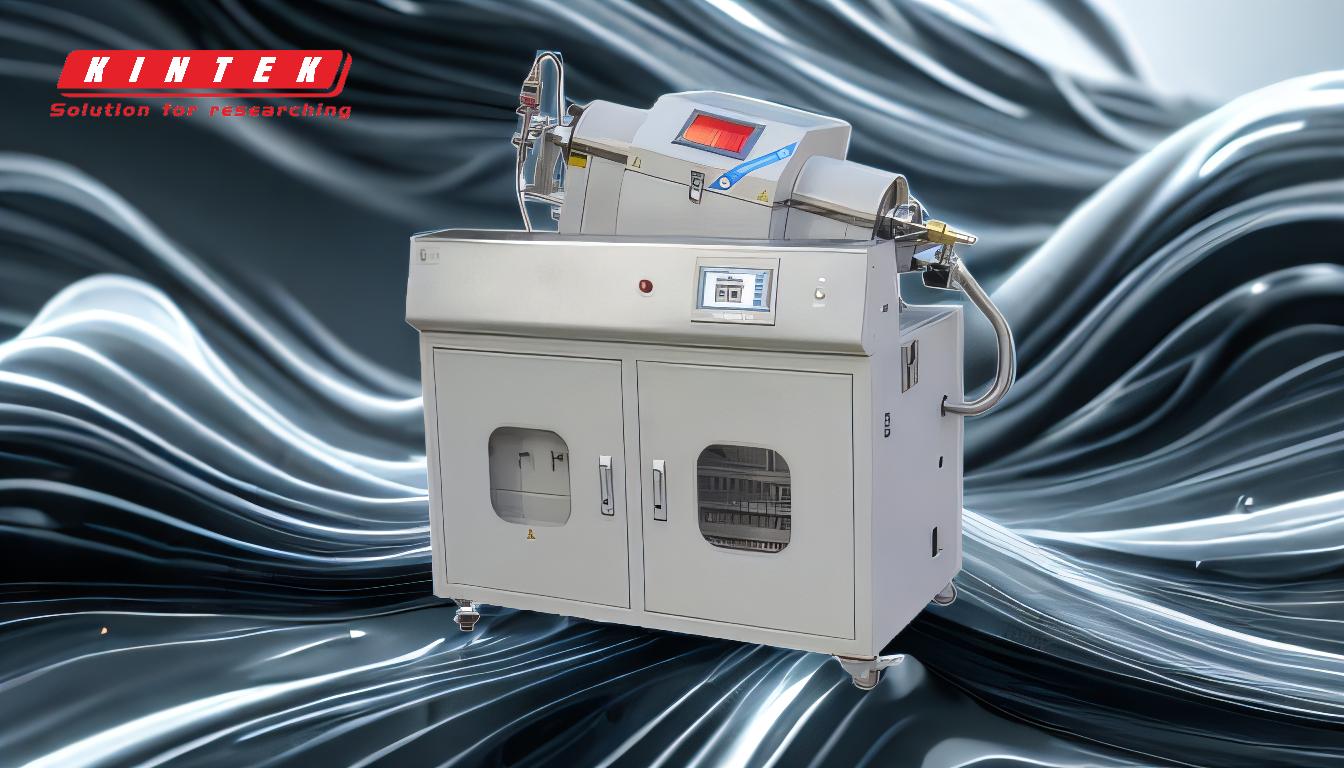
-
Introduction to CVD for Graphene Production:
- CVD is a process where gaseous precursors are introduced into a reaction chamber and thermally decomposed to form a thin film on a substrate.
- For graphene production, hydrocarbon gases like methane (CH₄) are commonly used as the carbon source.
- The process is conducted under vacuum or low-pressure conditions to ensure precise control over the reaction environment.
-
Role of Vacuum in CVD:
- Vacuum conditions reduce the atmospheric pressure inside the reaction chamber, which lowers the boiling point of the precursors and facilitates their decomposition.
- This is similar to the principles used in short path vacuum distillation, where vacuum reduces the boiling point of materials, making the process more efficient.
- In CVD, the vacuum helps in drawing the gaseous precursors into the chamber and ensures uniform deposition of the graphene layer.
-
Thermal Decomposition and Surface Adsorption:
- The substrate, often made of metals like nickel (Ni) or copper (Cu), is heated to high temperatures (typically 600°C to 1000°C).
- At these temperatures, the hydrocarbon gas decomposes, releasing carbon atoms that adsorb onto the substrate surface.
- In metals with high carbon solubility (e.g., Ni), carbon atoms diffuse into the substrate and segregate upon cooling to form graphene. In metals with low carbon solubility (e.g., Cu), carbon atoms directly adsorb onto the surface to form graphene.
-
Advantages of CVD for Graphene Production:
- Scalability: CVD can produce large-area graphene films, making it suitable for industrial applications.
- Cost-Effectiveness: Compared to other methods like mechanical exfoliation, CVD is relatively inexpensive.
- High Quality: The graphene produced via CVD is of high quality, with fewer defects and uniform thickness.
-
Challenges and Limitations:
- Filament Degradation: In hot filament CVD (HFCVD), the filament used to dissociate the precursor gas can degrade over time due to high temperatures and chemical reactions.
- Substrate Selection: The choice of substrate (e.g., Ni or Cu) affects the quality and uniformity of the graphene layer.
- Process Control: Precise control of temperature, pressure, and gas flow rates is essential to achieve consistent results.
-
Comparison with Other Graphene Production Methods:
- Mechanical Exfoliation: While this method produces high-quality graphene, it is not scalable and is limited to small-area production.
- Epitaxial Growth: This method involves growing graphene on silicon carbide (SiC) substrates but is expensive and less versatile than CVD.
- Reduction of Graphene Oxide: Although cost-effective, this method often results in graphene with more defects compared to CVD.
In summary, CVD is a highly effective method for producing graphene, leveraging vacuum conditions and thermal decomposition to deposit high-quality, large-area graphene films. Its scalability and cost-effectiveness make it a preferred choice for industrial applications, despite some challenges related to process control and substrate selection.
Summary Table:
Key Aspect | Details |
---|---|
Process | Gaseous precursors (e.g., methane) decompose in a vacuum or low-pressure environment. |
Substrate | Metals like nickel (Ni) or copper (Cu) are heated to high temperatures (600°C–1000°C). |
Mechanism | Carbon atoms adsorb onto the substrate, forming a graphene layer. |
Advantages | Scalable, cost-effective, and produces high-quality, large-area graphene. |
Challenges | Filament degradation, substrate selection, and precise process control. |
Want to learn more about CVD for graphene production? Contact our experts today!