Plasma Enhanced Vapor Deposition (PVD) is a sophisticated technique used to deposit thin films onto substrates, enhancing their properties for various applications. This process involves the use of plasma to assist in the deposition, which can improve film quality and adhesion. The method typically operates in a vacuum environment to ensure the purity and integrity of the deposited material. By utilizing plasma, the process can achieve lower deposition temperatures and better control over film properties, making it suitable for sensitive substrates and complex applications.
Key Points Explained:
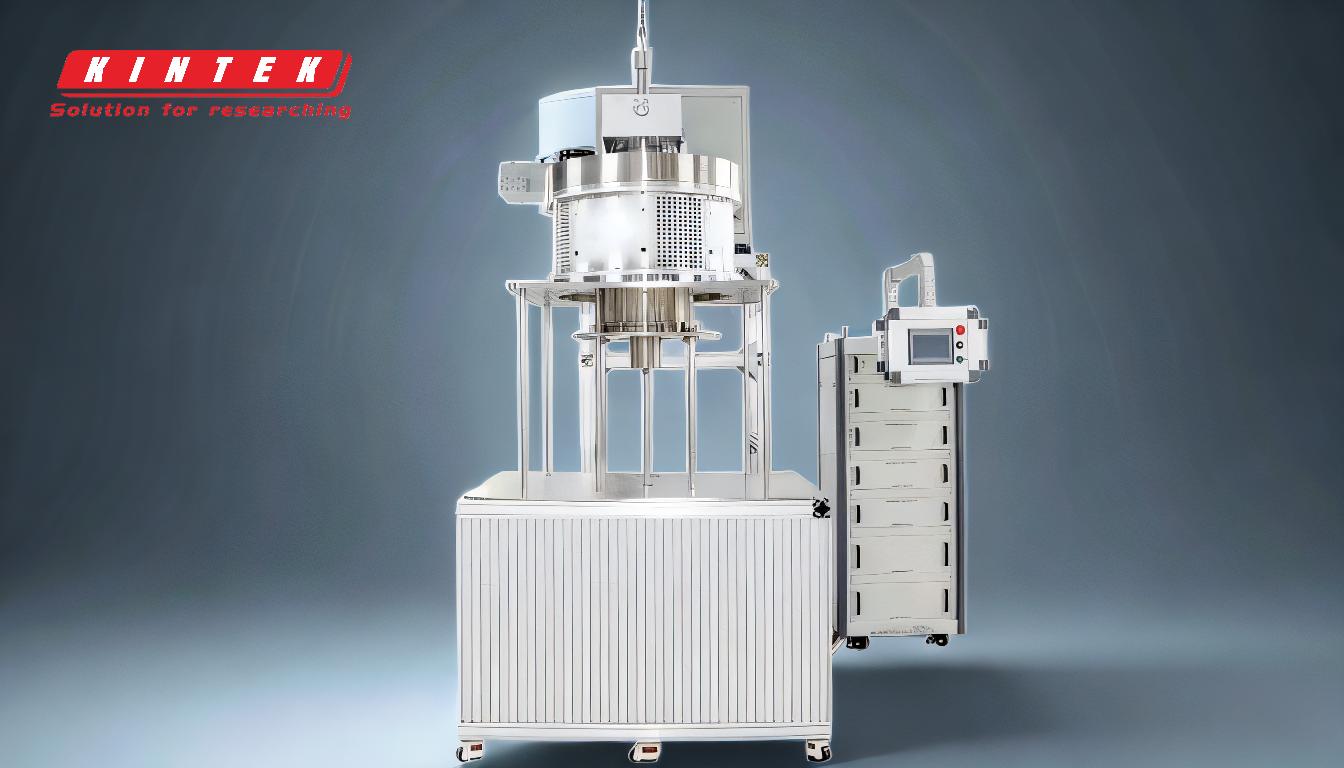
-
Vacuum Environment:
- The process takes place in a vacuum to eliminate any unwanted vapors and gases that could interfere with the deposition. This ensures that the material deposited is of high purity and adheres well to the substrate.
-
Evaporation of Source Material:
- A source material is heated until it evaporates. This evaporation is controlled to ensure a steady and consistent deposition rate. The evaporated particles travel directly to the substrate without interacting with background gases, which helps maintain the quality and uniformity of the film.
-
Role of Plasma:
- Plasma is introduced into the vacuum chamber to enhance the deposition process. The plasma consists of ionized gas particles that can interact with the evaporated material, increasing its energy and reactivity. This interaction can improve the adhesion of the film to the substrate and allow for deposition at lower temperatures.
-
Condensation on Substrate:
- The evaporated material condenses on the substrate, forming a thin film. The use of plasma can modify the properties of this film, such as its density, hardness, and chemical composition, by altering the energy and reactivity of the depositing particles.
-
Advantages of Plasma Enhanced PVD:
- Lower Deposition Temperatures: Suitable for temperature-sensitive substrates.
- Improved Film Properties: Enhanced adhesion, density, and uniformity.
- Versatility: Can be used with a wide range of materials and substrates.
-
Applications:
- This technology is widely used in the semiconductor industry, for coating tools and components, and in the production of optical and decorative coatings. The ability to precisely control the deposition process makes it invaluable for applications requiring high-performance thin films.
By integrating plasma into the vapor deposition process, manufacturers can achieve superior film properties and process efficiencies, making Plasma Enhanced Vapor Deposition a critical technology in modern material science and engineering.
Summary Table:
Key Aspect | Description |
---|---|
Vacuum Environment | Ensures high purity and adhesion by eliminating unwanted vapors and gases. |
Evaporation of Material | Source material is heated and evaporated for controlled deposition. |
Role of Plasma | Ionized gas enhances energy and reactivity, improving film adhesion and quality. |
Condensation on Substrate | Evaporated material forms a thin film with modified properties. |
Advantages | Lower deposition temperatures, improved film properties, and versatility. |
Applications | Used in semiconductors, tool coatings, and optical/decorative coatings. |
Learn how plasma enhanced vapor deposition can transform your material processes—contact us today for expert guidance!