Physical Vapor Deposition (PVD) and Chemical Vapor Deposition (CVD) are two widely used thin-film deposition techniques, each with distinct processes, applications, and characteristics. PVD involves vaporizing a solid material and condensing it onto a substrate, relying solely on physical processes without chemical reactions. In contrast, CVD involves chemical reactions between gaseous precursors and the substrate to form a solid thin film. PVD is environmentally friendly, operates at lower temperatures, and produces durable, smooth coatings, while CVD can handle a wider range of materials, operates at higher temperatures, and often results in thicker, rougher coatings. CVD equipment is more complex and deals with toxic byproducts, whereas PVD has minimal environmental impact.
Key Points Explained:
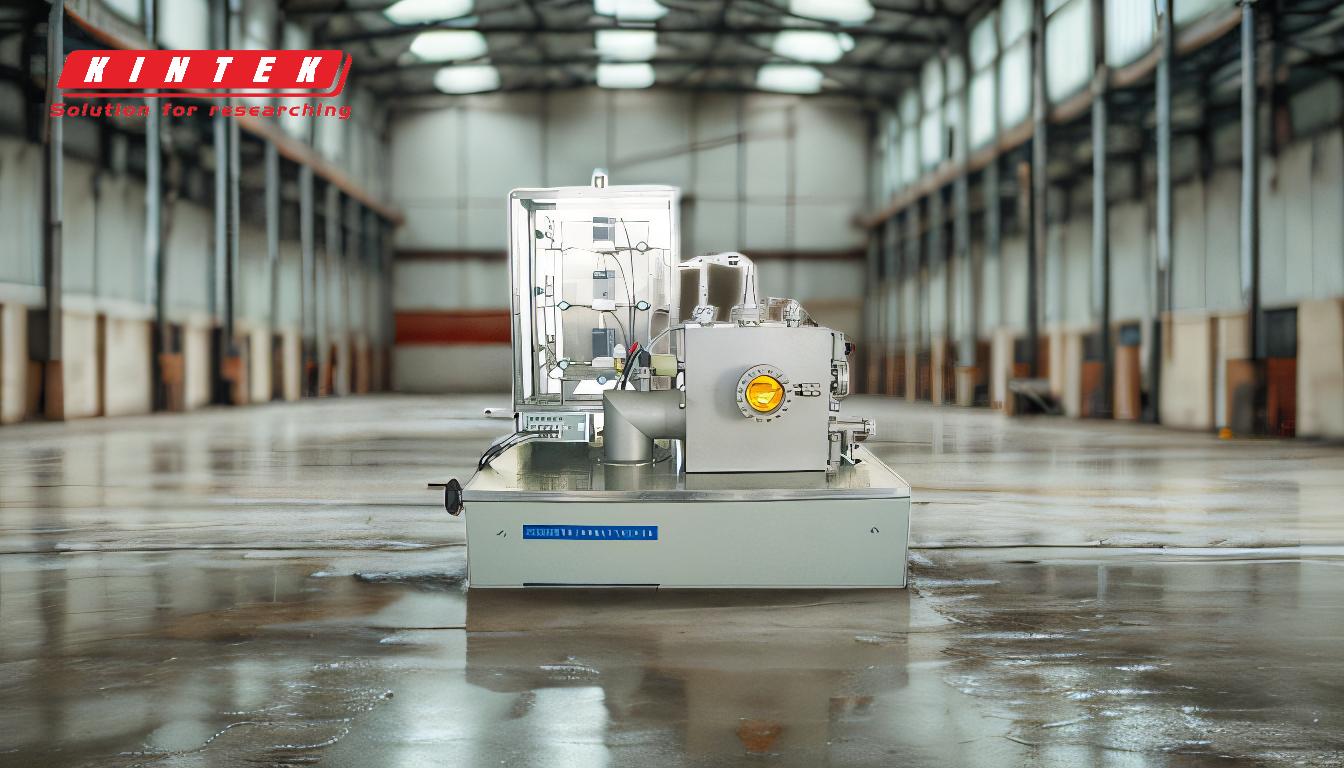
-
Process Mechanism:
- PVD: Involves physical processes such as evaporation, sputtering, or ion plating to vaporize a solid material, which then condenses onto the substrate. No chemical reactions occur during PVD.
- CVD: Relies on chemical reactions between gaseous precursors and the substrate surface to form a solid thin film. This process involves polymerization and coating phases occurring simultaneously.
-
Material State:
- PVD: Uses a solid coating material that is vaporized and then deposited onto the substrate.
- CVD: Utilizes gaseous coating materials that react chemically with the substrate to form the thin film.
-
Deposition Temperature:
- PVD: Operates at relatively low temperatures, typically between 250°C and 450°C.
- CVD: Requires higher temperatures, ranging from 450°C to 1050°C, to facilitate the chemical reactions necessary for deposition.
-
Coating Characteristics:
- PVD: Produces thin, smooth, and durable coatings that can withstand high temperatures. The coatings are typically more uniform and have excellent adhesion.
- CVD: Results in thicker and sometimes rougher coatings. The process can be applied to a wider range of materials, including those that are difficult to coat using PVD.
-
Environmental Impact:
- PVD: Environmentally friendly, as it does not involve chemical reactions or produce harmful byproducts. The process is clean and has minimal environmental impact.
- CVD: Can produce toxic byproducts due to the chemical reactions involved. The equipment is more specialized and requires additional measures to handle and dispose of these byproducts safely.
-
Equipment and Complexity:
- PVD: Equipment is generally simpler and more straightforward, focusing on physical vaporization and deposition processes.
- CVD: Equipment is more complex, designed to handle gaseous precursors and chemical reactions. The process requires precise control of temperature, pressure, and gas flow rates.
-
Applications:
- PVD: Commonly used for applications requiring high durability, such as cutting tools, decorative coatings, and wear-resistant layers.
- CVD: Suitable for applications needing thicker coatings or those involving complex geometries, such as semiconductor manufacturing, optical coatings, and protective layers on various substrates.
By understanding these key differences, equipment and consumable purchasers can make informed decisions based on the specific requirements of their applications, whether they prioritize environmental considerations, coating durability, or material compatibility.
Summary Table:
Aspect | PVD | CVD |
---|---|---|
Process Mechanism | Physical vaporization of solid material (no chemical reactions) | Chemical reactions between gaseous precursors and substrate |
Material State | Solid coating material | Gaseous coating materials |
Deposition Temperature | 250°C - 450°C | 450°C - 1050°C |
Coating Characteristics | Thin, smooth, durable, and uniform coatings | Thicker, sometimes rougher coatings; wider material compatibility |
Environmental Impact | Minimal; no toxic byproducts | Produces toxic byproducts; requires specialized handling |
Equipment Complexity | Simpler equipment | More complex equipment |
Applications | Cutting tools, decorative coatings, wear-resistant layers | Semiconductor manufacturing, optical coatings, protective layers |
Need help choosing between PVD and CVD for your application? Contact our experts today for personalized guidance!