Sintering time plays a critical role in determining the density of a sintered material. Longer sintering times generally allow for greater particle diffusion and bonding, which reduces porosity and increases density. However, excessive sintering times can lead to grain growth and defects, potentially degrading material properties. The relationship between sintering time and density is influenced by factors such as initial porosity, sintering temperature, particle size, and material composition. Optimal sintering time must balance densification with avoiding over-sintering to achieve the desired material properties.
Key Points Explained:
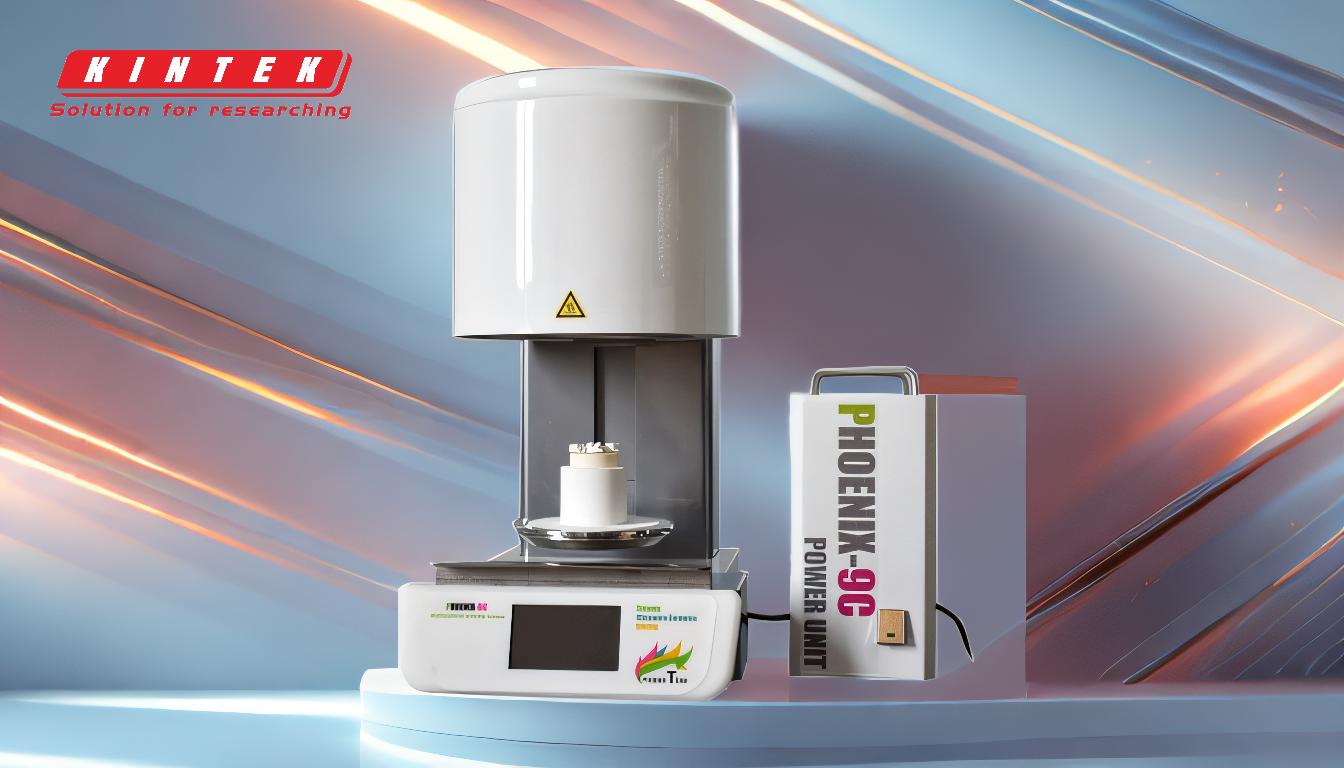
-
Sintering Time and Porosity Reduction:
- Longer sintering times enable greater particle diffusion, which reduces porosity by filling voids between particles.
- The initial porosity of the green compact significantly influences the extent of porosity reduction during sintering.
- For materials like pure oxide ceramics, longer sintering times are often necessary due to slower solid-state diffusion.
-
Temperature and Sintering Time Interaction:
- Sintering temperature and time are interdependent variables. Higher temperatures can accelerate densification, potentially reducing the required sintering time.
- However, excessively high temperatures or prolonged sintering times can lead to grain growth, which may reduce density and mechanical properties.
-
Material-Specific Considerations:
- Different materials respond differently to sintering time. For example, materials with smaller particle sizes and homogeneous compositions tend to densify more effectively with appropriate sintering times.
- Applying pressure during sintering can enhance densification and reduce the required sintering time.
-
Over-Sintering Risks:
- Excessive sintering times can lead to defects such as abnormal grain growth, which negatively impacts density and material properties.
- Over-sintering may also cause degradation in strength, hardness, and other mechanical properties.
-
Optimization of Sintering Time:
- The optimal sintering time must be determined experimentally for each material and application, considering factors like initial porosity, particle size, and desired final properties.
- Balancing sintering time with temperature and pressure is crucial to achieving high density without compromising material performance.
-
Practical Implications for Equipment and Consumable Purchasers:
- Understanding the relationship between sintering time and density is essential for selecting appropriate sintering equipment and consumables.
- Purchasers should consider materials with smaller particle sizes and homogeneous compositions to achieve better densification with shorter sintering times.
- Equipment capable of precise temperature and time control is critical for optimizing sintering processes and ensuring consistent product quality.
By carefully controlling sintering time and other variables, manufacturers can achieve the desired density and material properties, ensuring high-quality sintered products.
Summary Table:
Factor | Impact on Sintering |
---|---|
Sintering Time | Longer times reduce porosity but may cause grain growth if excessive. |
Temperature | Higher temps accelerate densification but risk grain growth if too high. |
Particle Size | Smaller particles enhance densification, reducing required sintering time. |
Material Composition | Homogeneous materials densify more effectively with appropriate sintering times. |
Over-Sintering Risks | Excessive time leads to grain growth, defects, and degraded material properties. |
Optimal Sintering | Balance time, temperature, and pressure for high density and performance. |
Optimize your sintering process for better material properties—contact our experts today!