Fast pyrolysis is a thermochemical process that converts biomass into bio-oil, char, and gas. Its efficiency depends on several factors, including feedstock properties, operating conditions, and reactor design. The efficiency is typically measured in terms of product yield and energy recovery, with bio-oil being the primary target. Fast pyrolysis operates at moderate temperatures (400–600°C), high heating rates, and short residence times, optimizing bio-oil production. However, the process is influenced by feedstock moisture content, temperature control, residence time, and reactor pressure. Proper management of these factors ensures high efficiency and desired product distribution, making fast pyrolysis a promising technology for renewable energy and bio-based products.
Key Points Explained:
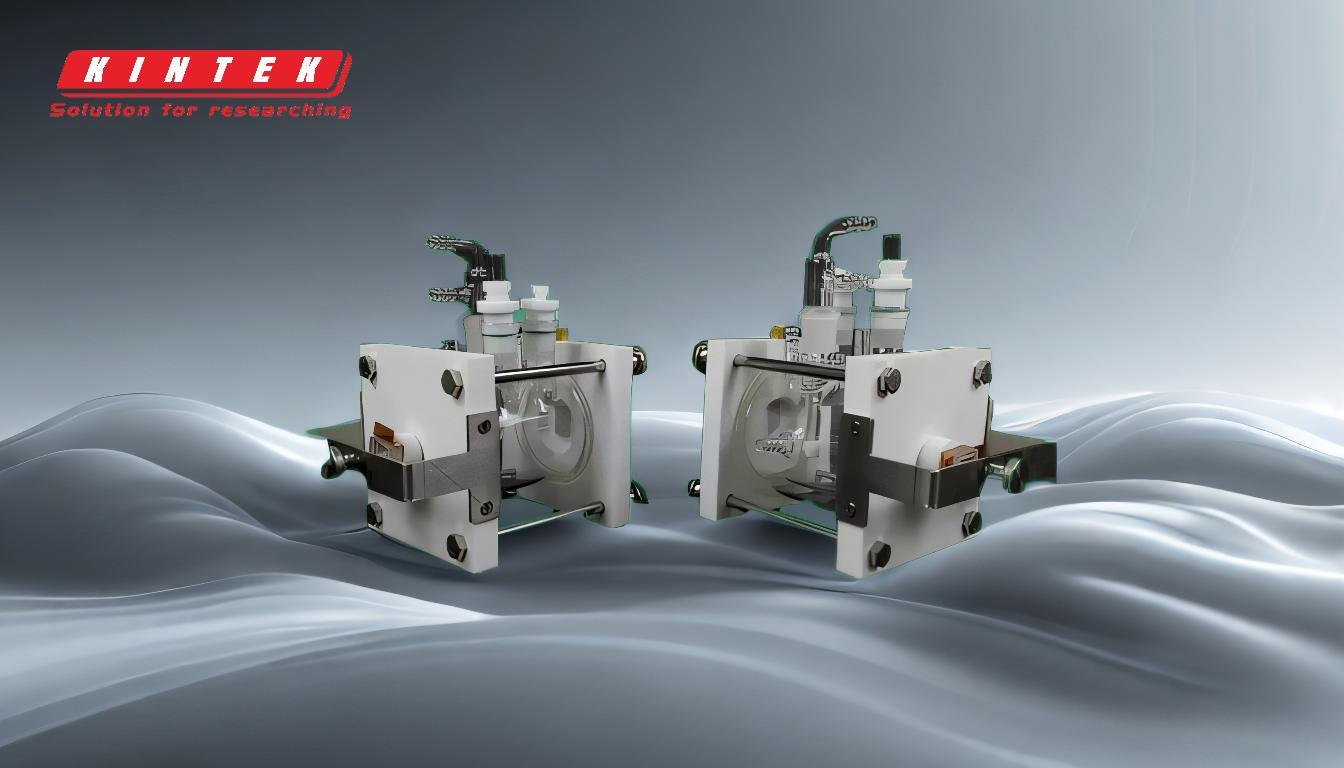
-
Definition and Purpose of Fast Pyrolysis:
- Fast pyrolysis is a thermal decomposition process that rapidly heats biomass in the absence of oxygen to produce bio-oil, char, and syngas.
- The primary goal is to maximize bio-oil yield, which is a liquid fuel substitute or feedstock for further refining.
-
Efficiency Metrics:
- Efficiency is evaluated based on product yield (bio-oil, char, gas) and energy recovery.
- Bio-oil yields can reach 60–75% under optimal conditions, making it a key indicator of process efficiency.
-
Key Factors Influencing Efficiency:
-
Feedstock Properties:
- Moisture content, particle size, and composition (volatile matter, fixed carbon, ash content) significantly impact pyrolysis outcomes.
- Low moisture content (<10%) is preferred to avoid energy loss from water evaporation.
-
Operating Conditions:
- Temperature: Moderate temperatures (400–600°C) are ideal for bio-oil production. Higher temperatures favor gas formation, while lower temperatures increase char yield.
- Heating Rate: High heating rates (100–1000°C/s) are essential for fast pyrolysis to achieve rapid biomass decomposition.
- Residence Time: Short residence times (0.5–2 seconds) prevent secondary reactions that degrade bio-oil quality.
- Pressure: Atmospheric pressure is commonly used, but slight variations can influence product distribution.
-
Feedstock Properties:
-
Product Distribution Optimization:
- Bio-Oil: Maximized at moderate temperatures (450–500°C), high heating rates, and short residence times.
- Char: Favored at lower temperatures (<400°C) and slower heating rates.
- Gas: Dominates at high temperatures (>600°C) and longer residence times.
-
Challenges and Limitations:
- Feedstock variability can lead to inconsistent product yields.
- Bio-oil quality issues, such as high oxygen content and instability, require post-processing.
- Energy input for heating and vapor condensation affects overall system efficiency.
-
Technological Advancements:
- Improved reactor designs (e.g., fluidized bed, circulating fluidized bed) enhance heat transfer and product yields.
- Catalytic pyrolysis and co-pyrolysis with other feedstocks (e.g., plastics) are being explored to improve bio-oil quality and process efficiency.
-
Applications and Benefits:
- Bio-oil can be used as a renewable fuel or refined into chemicals and materials.
- Char can serve as a soil amendment or carbon sequestration agent.
- Syngas can be utilized for heat and power generation.
-
Conclusion:
- Fast pyrolysis is an efficient and versatile process for converting biomass into valuable products.
- Optimizing feedstock selection, operating conditions, and reactor design is crucial for maximizing efficiency and achieving desired product distributions.
- Continued research and development are essential to address challenges and enhance the commercial viability of fast pyrolysis technology.
Summary Table:
Aspect | Details |
---|---|
Process | Thermal decomposition of biomass in the absence of oxygen. |
Primary Product | Bio-oil (60–75% yield under optimal conditions). |
Key Factors | Feedstock properties, temperature, heating rate, residence time, pressure. |
Optimal Conditions | 400–600°C, high heating rates (100–1000°C/s), short residence times (0.5–2s). |
Applications | Renewable fuel, chemicals, soil amendment, heat, and power generation. |
Challenges | Feedstock variability, bio-oil quality, energy input for heating. |
Discover how fast pyrolysis can revolutionize renewable energy—contact our experts today!