Pyrolysis efficiency is influenced by a variety of factors, including the type of biomass or waste material, its moisture content, temperature, residence time, pressure, and particle size. Higher temperatures generally increase gas production, while lower temperatures favor solid products. Proper control of these factors is crucial for optimizing the yield and quality of pyrolysis products, such as bio-oil, syngas, and biochar. The efficiency of specific pyrolysis reactors, like rotary-kiln systems, also depends on heat supply and rotational speed. Overall, achieving high efficiency requires balancing these variables to match the desired end products and operational goals.
Key Points Explained:
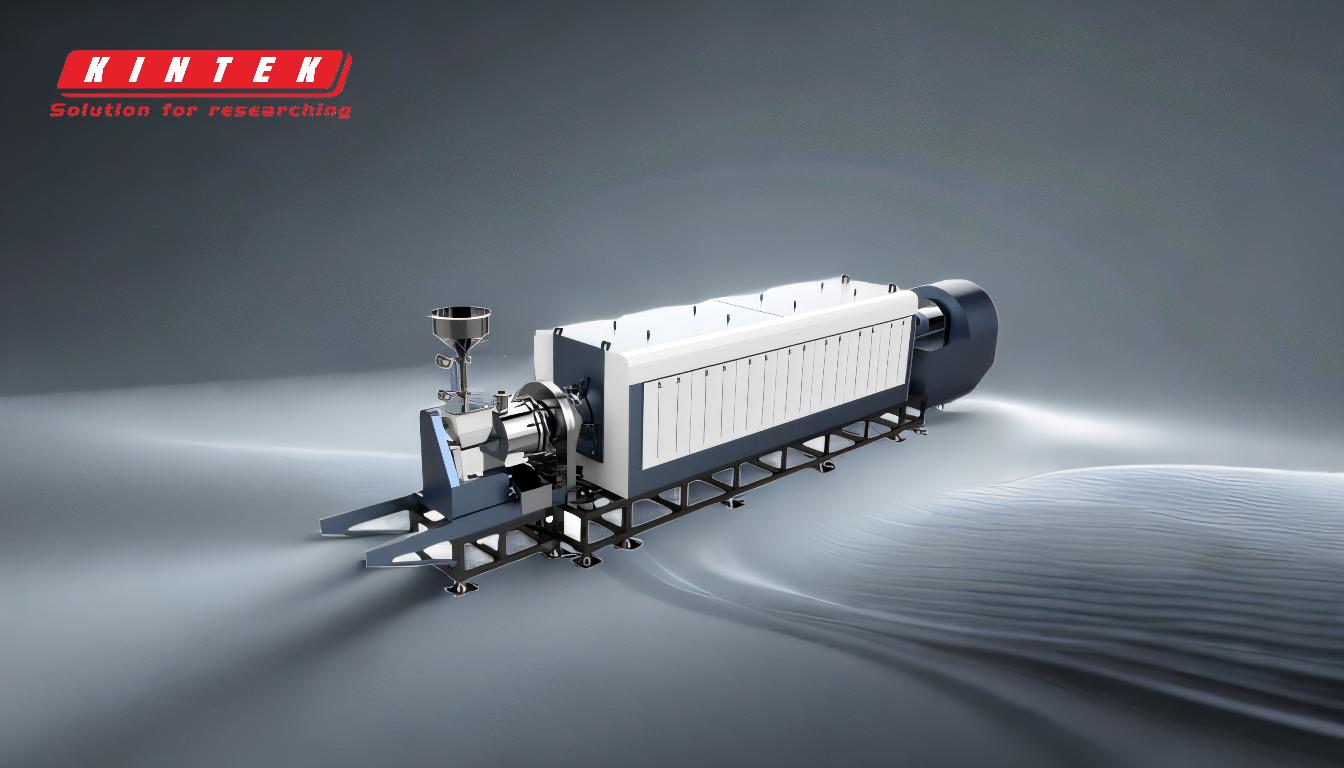
-
Factors Affecting Pyrolysis Efficiency:
- Biomass/Waste Composition: The type of material being pyrolyzed (e.g., wood, agricultural waste, plastics) significantly impacts the process. Different materials decompose at varying temperatures, affecting the yield and quality of products.
- Moisture Content: High moisture content in biomass can reduce efficiency by requiring additional energy to evaporate water before pyrolysis begins. Dryer feedstocks generally lead to better thermal conversion.
- Temperature: Pyrolysis efficiency is highly temperature-dependent. Higher temperatures (typically above 500°C) favor the production of non-condensable gases (e.g., syngas), while lower temperatures (300–500°C) are better for producing biochar and bio-oil.
- Residence Time: The duration that material spends in the pyrolysis reactor affects the degree of thermal conversion. Longer residence times can lead to more complete decomposition but may also increase energy consumption.
- Pressure: Operating pressure influences the distribution of pyrolysis products. Lower pressures often favor the production of gases, while higher pressures can enhance liquid yields.
- Particle Size: Smaller particles heat more uniformly and decompose faster, leading to higher yields of pyrolysis oil. Larger particles may result in incomplete decomposition and lower efficiency.
-
Impact of Operating Conditions:
- Heating Rate: Faster heating rates can improve the yield of bio-oil by minimizing secondary reactions that degrade the primary pyrolysis products.
- Reactor Design: The type of reactor (e.g., fixed-bed, fluidized-bed, rotary-kiln) plays a critical role in determining efficiency. For example, rotary-kiln reactors rely on heat supply and rotational speed to optimize performance.
- Heat Transfer: Efficient heat transfer within the reactor ensures uniform temperature distribution, which is essential for consistent product quality and yield.
-
Product Distribution:
- Biochar: Produced at lower temperatures, biochar is a valuable solid product used in soil amendment and carbon sequestration.
- Bio-Oil: A liquid product obtained at moderate temperatures, bio-oil can be used as a renewable fuel or chemical feedstock.
- Syngas: Generated at higher temperatures, syngas (a mixture of hydrogen, carbon monoxide, and methane) is a versatile energy carrier.
-
Optimization Strategies:
- Feedstock Pre-Treatment: Drying and reducing particle size can improve pyrolysis efficiency by ensuring uniform heating and faster decomposition.
- Process Control: Precise control of temperature, residence time, and pressure is essential for maximizing yield and minimizing energy losses.
- Reactor Maintenance: Regular maintenance ensures consistent performance and safety, reducing downtime and operational inefficiencies.
-
Challenges and Considerations:
- Energy Input: Pyrolysis requires significant energy input, particularly for heating and maintaining reactor conditions. Balancing energy consumption with product yield is a key challenge.
- Product Quality: Achieving consistent product quality (e.g., bio-oil stability, biochar carbon content) requires careful control of process variables.
- Economic Viability: The cost of feedstock, reactor operation, and product separation must be balanced against the market value of the pyrolysis products.
In summary, pyrolysis efficiency is a complex interplay of feedstock properties, operating conditions, and reactor design. By carefully optimizing these factors, it is possible to achieve high yields of valuable products while minimizing energy consumption and operational costs.
Summary Table:
Factor | Impact on Pyrolysis Efficiency |
---|---|
Biomass/Waste Composition | Different materials decompose at varying temperatures, affecting yield and product quality. |
Moisture Content | High moisture reduces efficiency; dry feedstocks improve thermal conversion. |
Temperature | Higher temps favor gas production; lower temps favor biochar and bio-oil. |
Residence Time | Longer times improve decomposition but increase energy consumption. |
Pressure | Lower pressures favor gas production; higher pressures enhance liquid yields. |
Particle Size | Smaller particles heat uniformly and decompose faster, improving oil yields. |
Heating Rate | Faster rates improve bio-oil yield by minimizing secondary reactions. |
Reactor Design | Reactor type (e.g., rotary-kiln) and heat transfer efficiency are critical for optimal performance. |
Product Distribution | Biochar (low temps), bio-oil (moderate temps), and syngas (high temps) are key outputs. |
Ready to optimize your pyrolysis process? Contact our experts today for tailored solutions!