PVD (Physical Vapor Deposition) coating is a highly effective and versatile method for enhancing the durability, appearance, and performance of watch components. It offers several advantages, such as high hardness, corrosion resistance, and wear resistance, making it ideal for watch applications. However, it also has some limitations, including high costs and challenges in coating complex geometries. Overall, PVD coating is a reliable choice for watches, providing a balance between aesthetic appeal and functional durability.
Key Points Explained:
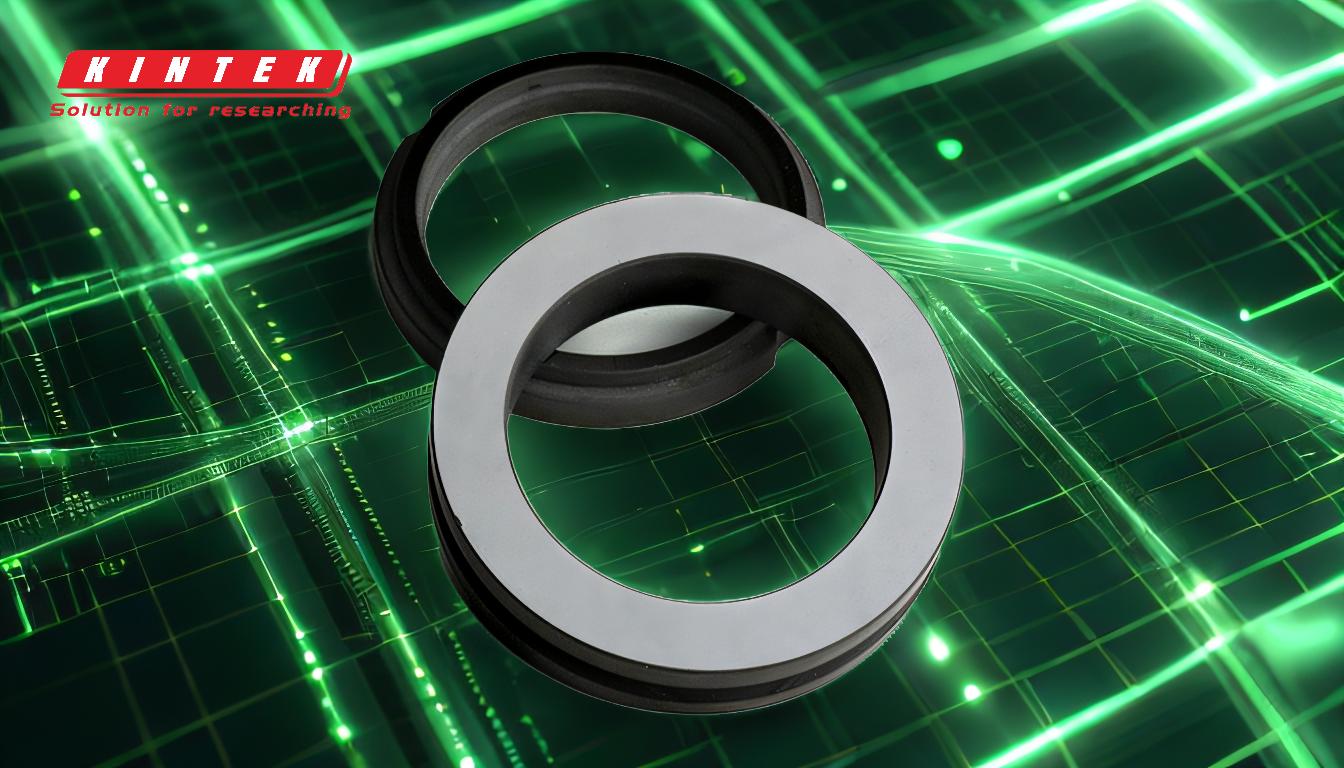
-
Advantages of PVD Coating for Watches:
- High Hardness and Durability: PVD coatings are known for their exceptional hardness, which makes them highly resistant to scratches and wear. This is particularly beneficial for watch components like bezels, cases, and bracelets, which are frequently exposed to physical contact.
- Corrosion Resistance: PVD coatings provide excellent protection against corrosion, ensuring that watches maintain their appearance and functionality even in harsh environments.
- Aesthetic Appeal: The thin, uniform coatings (typically 0.02-5 microns) produced by PVD processes enhance the visual appeal of watches, offering a range of colors and finishes, including black, gold, and rose gold.
- Lower Process Temperatures: PVD operates at relatively low temperatures (around 500 °C), reducing the risk of thermal damage to the watch components. This is crucial for maintaining the integrity of delicate parts.
- Environmental Friendliness: Compared to other coating methods like CVD (Chemical Vapor Deposition), PVD is more environmentally friendly, as it involves fewer harmful chemicals and emissions.
-
Disadvantages of PVD Coating:
- High Cost: The PVD process is more expensive than some alternative coating methods, which can increase the overall cost of the watch.
- Line of Sight Process: PVD is a 'line of sight' process, meaning it is challenging to coat areas that are not directly exposed to the coating source. This can limit its effectiveness for coating complex or hidden parts of a watch.
- Time-Consuming: The PVD process can be time-consuming, which may affect production timelines, especially for high-volume manufacturing.
-
Suitability for Watch Components:
- Precision and Complexity: PVD is well-suited for coating precision components with tight tolerances, such as watch gears and springs. However, coating parts with complex geometric shapes can be challenging, although advancements in PVD technology have largely mitigated this issue.
- Thin and Uniform Coatings: The ability to deposit thin, uniform coatings is particularly advantageous for watch components, as it preserves the sharpness and precision of small parts without adding significant bulk.
-
Operational Considerations:
- Computer-Controlled Systems: Modern PVD coating machines are computer-controlled, allowing for precise control over the coating process. This enhances the consistency and quality of the coatings, which is essential for high-end watch manufacturing.
- Cooling Systems: The PVD process requires cooling water circulation systems to dissipate heat and prevent damage to the coating system components. This adds to the complexity and cost of the process but is necessary for maintaining the quality of the coatings.
-
Applications in the Watch Industry:
- Aesthetic and Functional Benefits: PVD coatings are widely used in the watch industry to enhance both the aesthetic appeal and functional durability of watch components. The ability to produce a variety of colors and finishes makes PVD a popular choice for luxury and high-end watches.
- Wear Resistance: The high hardness and wear resistance of PVD coatings ensure that watches can withstand daily wear and tear, maintaining their appearance and functionality over time.
In summary, PVD coating is an excellent choice for watches, offering a combination of durability, aesthetic appeal, and environmental benefits. While it has some limitations, such as higher costs and challenges in coating complex geometries, the advantages far outweigh the disadvantages, making it a preferred method in the watch industry.
Summary Table:
Aspect | Details |
---|---|
Advantages | High hardness, corrosion resistance, aesthetic appeal, low process temperatures, eco-friendly. |
Disadvantages | High cost, line of sight process, time-consuming. |
Suitability | Ideal for precision components; challenges with complex geometries. |
Operational Features | Computer-controlled systems, cooling water circulation. |
Applications | Enhances durability and aesthetics for luxury and high-end watches. |
Want to learn more about PVD coating for your watch components? Contact us today for expert advice!