Aluminum casting requires precise temperature control to ensure the metal flows properly into the mold without causing defects. The ideal temperature range for aluminum casting typically falls between 1,100°F (593°C) and 1,300°F (704°C), depending on the specific alloy and casting method. Proper temperature management is critical to avoid issues like porosity, shrinkage, or incomplete filling of the mold. Factors such as alloy composition, mold type, and cooling rates also influence the optimal casting temperature. Maintaining this temperature range ensures the aluminum remains in a liquid state long enough to fill the mold while avoiding overheating, which can degrade the metal's properties.
Key Points Explained:
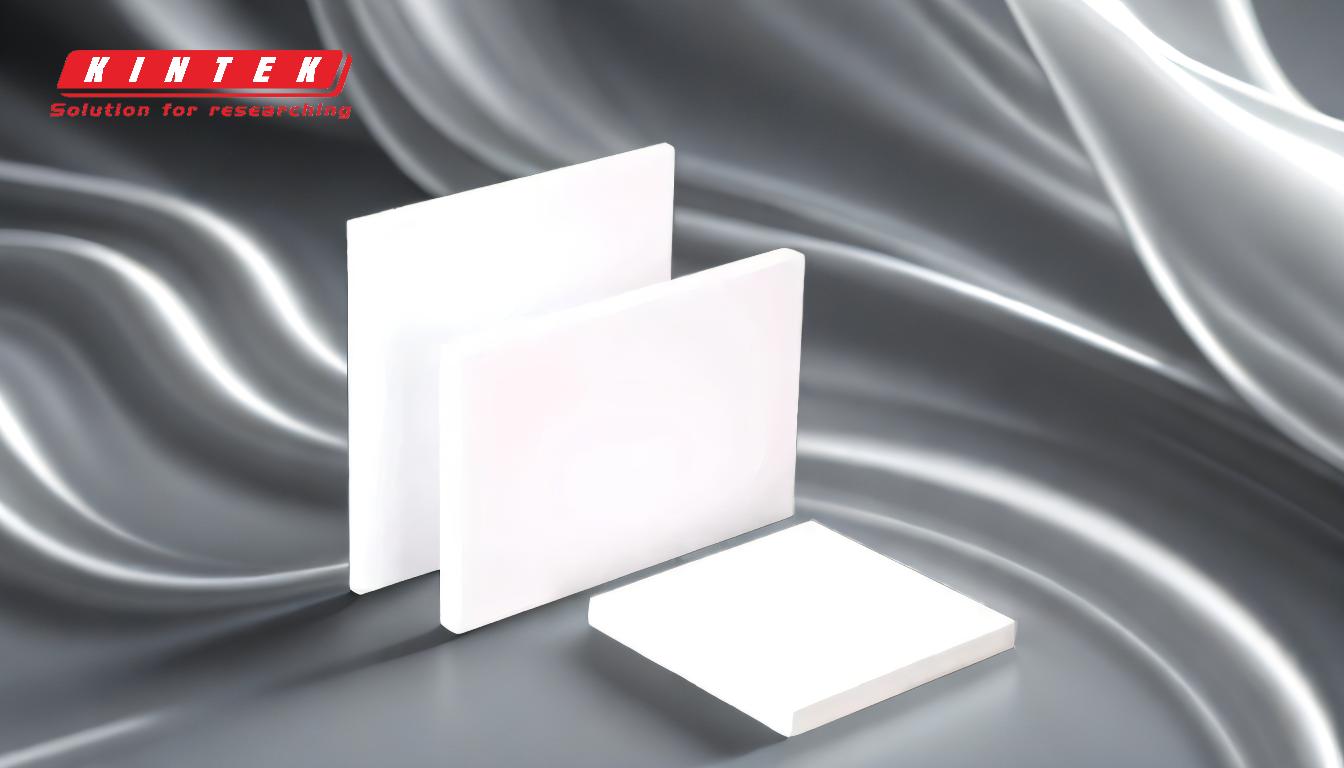
-
Optimal Temperature Range for Aluminum Casting
- The ideal temperature for casting aluminum is typically between 1,100°F (593°C) and 1,300°F (704°C).
- This range ensures the aluminum remains molten and flows smoothly into the mold.
- Temperatures below this range may result in incomplete filling, while excessive heat can lead to oxidation, gas absorption, or degradation of the alloy's mechanical properties.
-
Factors Influencing Casting Temperature
- Alloy Composition: Different aluminum alloys have varying melting points and fluidity. For example, aluminum-silicon alloys may require slightly higher temperatures due to their higher silicon content.
- Casting Method: Methods like sand casting, die casting, or investment casting may require adjustments in temperature to account for mold material and cooling rates.
- Mold Design: Complex molds with thin sections may require higher temperatures to ensure proper filling.
-
Importance of Temperature Control
- Defect Prevention: Proper temperature management minimizes defects such as porosity, shrinkage, and cold shuts.
- Surface Finish: Maintaining the correct temperature ensures a smooth surface finish and reduces the need for post-casting machining.
- Mechanical Properties: Overheating can weaken the aluminum, while insufficient heat can lead to incomplete bonding between metal grains.
-
Tools for Temperature Measurement
- Pyrometers: Used to measure the temperature of molten aluminum accurately.
- Thermocouples: Often integrated into furnaces to monitor and control temperature during the casting process.
- Infrared Thermometers: Provide non-contact temperature readings, useful for quick checks.
-
Cooling and Solidification
- After pouring, the aluminum must cool and solidify uniformly to avoid internal stresses or cracks.
- Controlled cooling rates are essential, especially for alloys prone to thermal cracking.
-
Safety Considerations
- Molten aluminum poses significant safety risks, including burns and fire hazards.
- Proper protective gear, such as heat-resistant gloves, aprons, and face shields, is essential.
- Adequate ventilation is necessary to avoid inhalation of fumes released during the casting process.
By adhering to these guidelines, you can achieve high-quality aluminum castings with minimal defects and optimal mechanical properties.
Summary Table:
Key Aspect | Details |
---|---|
Optimal Temperature Range | 1,100°F (593°C) to 1,300°F (704°C) |
Factors Influencing Temp | Alloy composition, casting method, mold design |
Importance of Control | Prevents defects, ensures smooth surface finish, maintains metal properties |
Tools for Measurement | Pyrometers, thermocouples, infrared thermometers |
Safety Considerations | Use protective gear, ensure proper ventilation |
Need help achieving the perfect casting temperature? Contact our experts today for tailored solutions!