Thermal evaporation is a widely used physical vapor deposition (PVD) technique for preparing thin films. It involves heating a target material in a high-vacuum environment until it evaporates, forming a vapor stream that travels to a substrate, where it condenses and forms a thin film. The process relies on precise control of temperature, vacuum conditions, and deposition parameters to achieve uniform and high-quality films. Thermal evaporation is particularly suitable for depositing metals, semiconductors, and certain organic materials, making it a critical method in industries like electronics, optics, and energy.
Key Points Explained:
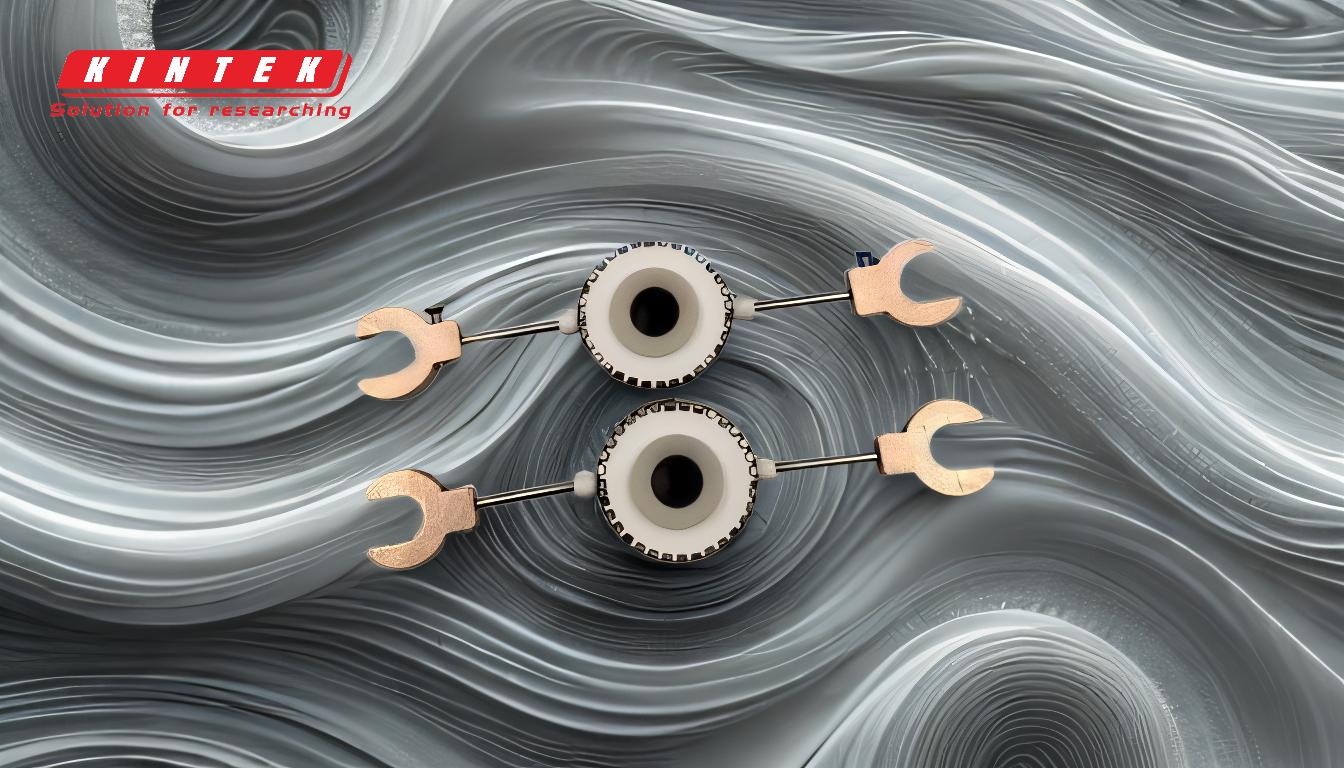
-
Principle of Thermal Evaporation:
- Thermal evaporation works by heating a target material until it reaches its evaporation point, converting it into a vapor.
- The vaporized material is transported through a high-vacuum chamber and deposits onto a substrate, where it condenses to form a thin film.
- This process is driven by thermal energy, typically generated using a resistive heating element (e.g., tungsten boat or coil) or an electron beam.
-
Key Components of the System:
- Vacuum Chamber: A high-vacuum environment is essential to minimize collisions between vaporized particles and gas molecules, ensuring a clean and uniform deposition.
- Heating Source: A resistive heating element (e.g., tungsten boat or coil) or an electron beam is used to heat the target material to its evaporation temperature.
- Substrate: The surface onto which the thin film is deposited. It is positioned above the evaporation source to allow the vaporized material to condense uniformly.
- Vacuum Pump: Maintains the high-vacuum environment, typically at pressures of 10^-5 to 10^-7 Torr, to ensure a free path for the vaporized particles.
-
Steps in the Thermal Evaporation Process:
-
Preparation:
- The target material is placed in the evaporation source (e.g., boat or coil).
- The substrate is cleaned and positioned in the vacuum chamber.
-
Evaporation:
- The target material is heated until it evaporates, forming a vapor cloud.
- The vapor pressure inside the chamber increases, creating a vapor stream.
-
Deposition:
- The vaporized material travels through the vacuum chamber and deposits onto the substrate.
- The material condenses and forms a thin film as it adheres to the substrate.
-
Cooling and Removal:
- After deposition, the substrate is cooled, and the vacuum chamber is vented to remove the coated substrate.
-
Preparation:
-
Advantages of Thermal Evaporation:
- High Purity: The high-vacuum environment minimizes contamination, resulting in pure and high-quality films.
- Versatility: Suitable for depositing a wide range of materials, including metals, semiconductors, and certain organic compounds.
- Precision: Allows precise control over film thickness and uniformity.
- Scalability: Can be scaled for both small-scale laboratory experiments and large-scale industrial production.
-
Limitations of Thermal Evaporation:
- Material Compatibility: Not all materials can be evaporated due to differences in melting and evaporation temperatures.
- High Energy Consumption: Requires significant energy to heat the target material and maintain the vacuum.
- Limited Adhesion: Some materials may exhibit poor adhesion to the substrate, requiring additional surface treatments.
-
Applications of Thermal Evaporation:
- Electronics: Used to deposit metal contacts and interconnects in semiconductor devices.
- Optics: Produces thin films for anti-reflective coatings, mirrors, and optical filters.
- Energy: Deposits materials for solar cells, batteries, and fuel cells.
- Flexible Electronics: Enables the production of thin films for flexible displays, organic light-emitting diodes (OLEDs), and flexible solar panels.
-
Comparison with Other Thin Film Deposition Techniques:
- Sputtering: Uses ionized gas to eject material from a target, offering better adhesion and compatibility with a wider range of materials.
- Chemical Vapor Deposition (CVD): Involves chemical reactions to deposit thin films, providing better conformal coverage on complex geometries.
- Spin Coating: A solution-based method for depositing thin films, typically used for polymers and organic materials.
-
Recent Advances in Thermal Evaporation:
- Development of advanced heating sources, such as electron beam evaporation, for higher evaporation rates and better control.
- Integration with other deposition techniques (e.g., sputtering or CVD) to create hybrid processes for multi-layer films.
- Exploration of new materials, such as 2D materials (e.g., graphene) and organic compounds, for emerging applications in flexible electronics and energy storage.
By understanding the principles, components, and steps involved in thermal evaporation, users can make informed decisions about its suitability for specific applications and optimize the process for desired film properties.
Summary Table:
Aspect | Details |
---|---|
Principle | Heating target material in a vacuum to evaporate and deposit onto a substrate. |
Key Components | Vacuum chamber, heating source, substrate, vacuum pump. |
Advantages | High purity, versatility, precision, scalability. |
Limitations | Material compatibility, high energy consumption, limited adhesion. |
Applications | Electronics, optics, energy, flexible electronics. |
Comparison | Better purity than sputtering, less conformal than CVD, simpler than spin coating. |
Recent Advances | Electron beam evaporation, hybrid processes, 2D materials. |
Discover how thermal evaporation can enhance your thin film processes—contact our experts today!