Biochar is manufactured through processes like slow pyrolysis, fast pyrolysis, and gasification, with slow pyrolysis being the most feasible for producing high-quality biochar for agricultural use. The process involves preparing biomass by drying and mechanical comminution, followed by heating it to around 400 °C in an oxygen-limited environment for several hours. This results in the decomposition of biomass into biochar and bio-gas. The energy required for the process can be covered by combusting the gaseous by-products. The key variables in the production process are the highest treatment temperature (HTT) and residence time, which influence the quality and properties of the biochar.
Key Points Explained:
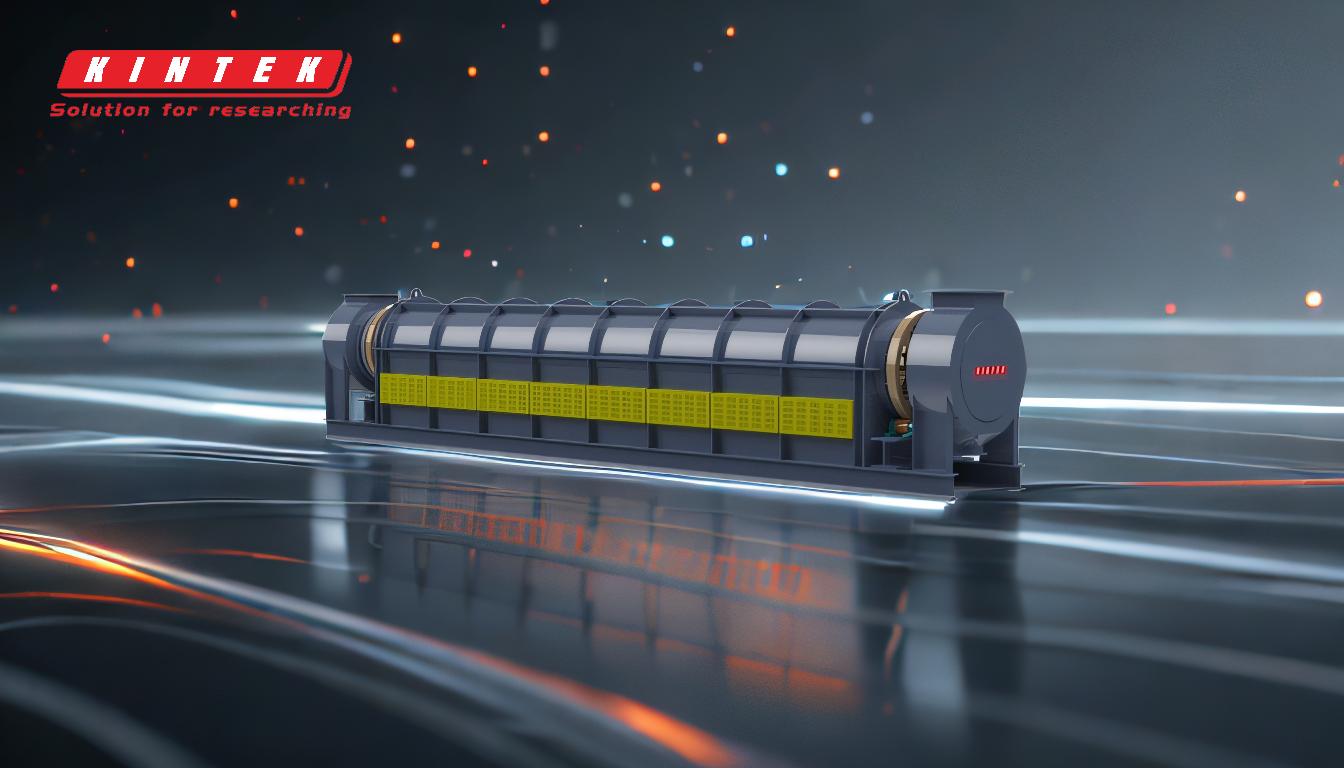
-
Types of Biochar Production Processes:
- Slow Pyrolysis: This is the most common method for producing high-quality biochar, especially for agricultural use. It involves heating biomass at lower temperatures (around 400 °C) for several hours in an oxygen-limited environment. The slow heating rate and longer residence time ensure a more consistent and reliable product.
- Fast Pyrolysis: This process involves higher heating rates and shorter residence times, typically producing more bio-oil and less biochar compared to slow pyrolysis.
- Gasification: In this process, biomass is heated at high temperatures with a controlled amount of oxygen, producing syngas (a mixture of hydrogen and carbon monoxide) along with biochar. The biochar yield is generally lower compared to pyrolysis.
-
Biomass Preparation:
- Drying: The biomass must be dried to reduce moisture content, which is essential for efficient pyrolysis. High moisture content can lead to incomplete decomposition and lower-quality biochar.
- Mechanical Comminution: The biomass is mechanically reduced in size to ensure uniform heating and efficient decomposition during pyrolysis.
-
Pyrolytic Decomposition:
- Temperature and Residence Time: During slow pyrolysis, the biomass is heated to around 400 °C for several hours. The lower temperature and longer residence time allow for the gradual breakdown of the biomass into biochar and bio-gas.
- Energy Requirements: The energy needed to reach the required temperatures can be supplied by combusting the gaseous by-products (bio-gas) generated during the process.
-
Key Variables in Biochar Production:
- Highest Treatment Temperature (HTT): The temperature at which the biomass is treated significantly affects the properties of the biochar, such as its carbon content, porosity, and stability.
- Residence Time: The duration for which the biomass is subjected to the pyrolysis process influences the degree of decomposition and the quality of the biochar.
-
Applications and Quality Considerations:
- Agricultural Use: Biochar produced through slow pyrolysis is particularly suitable for agricultural applications due to its consistent quality and beneficial properties, such as improved soil fertility and carbon sequestration.
- Environmental Impact: The process of biochar production is considered environmentally friendly, as it utilizes renewable biomass and can help reduce greenhouse gas emissions by sequestering carbon in the soil.
By understanding these key points, potential buyers and users of biochar can make informed decisions about the production process and the quality of biochar needed for specific applications.
Summary Table:
Aspect | Details |
---|---|
Production Processes | Slow Pyrolysis, Fast Pyrolysis, Gasification |
Optimal Method | Slow Pyrolysis (400 °C, oxygen-limited, several hours) |
Biomass Preparation | Drying and Mechanical Comminution |
Key Variables | Highest Treatment Temperature (HTT), Residence Time |
Energy Source | Combustion of gaseous by-products (bio-gas) |
Applications | Agricultural use, soil fertility improvement, carbon sequestration |
Environmental Impact | Reduces greenhouse gas emissions, utilizes renewable biomass |
Interested in high-quality biochar for your agricultural needs? Contact us today to learn more!