Chemical deposition and physical deposition are two distinct techniques used in thin-film fabrication, each with unique processes, advantages, and limitations. Chemical deposition, such as chemical vapor deposition (CVD), relies on chemical reactions to form thin films, often requiring high temperatures and potentially leading to impurities. In contrast, physical deposition, like physical vapor deposition (PVD), involves the physical transfer of material onto a substrate, typically at lower temperatures and without corrosive byproducts. Understanding these differences is crucial for selecting the appropriate method based on the desired film properties, substrate compatibility, and application requirements.
Key Points Explained:
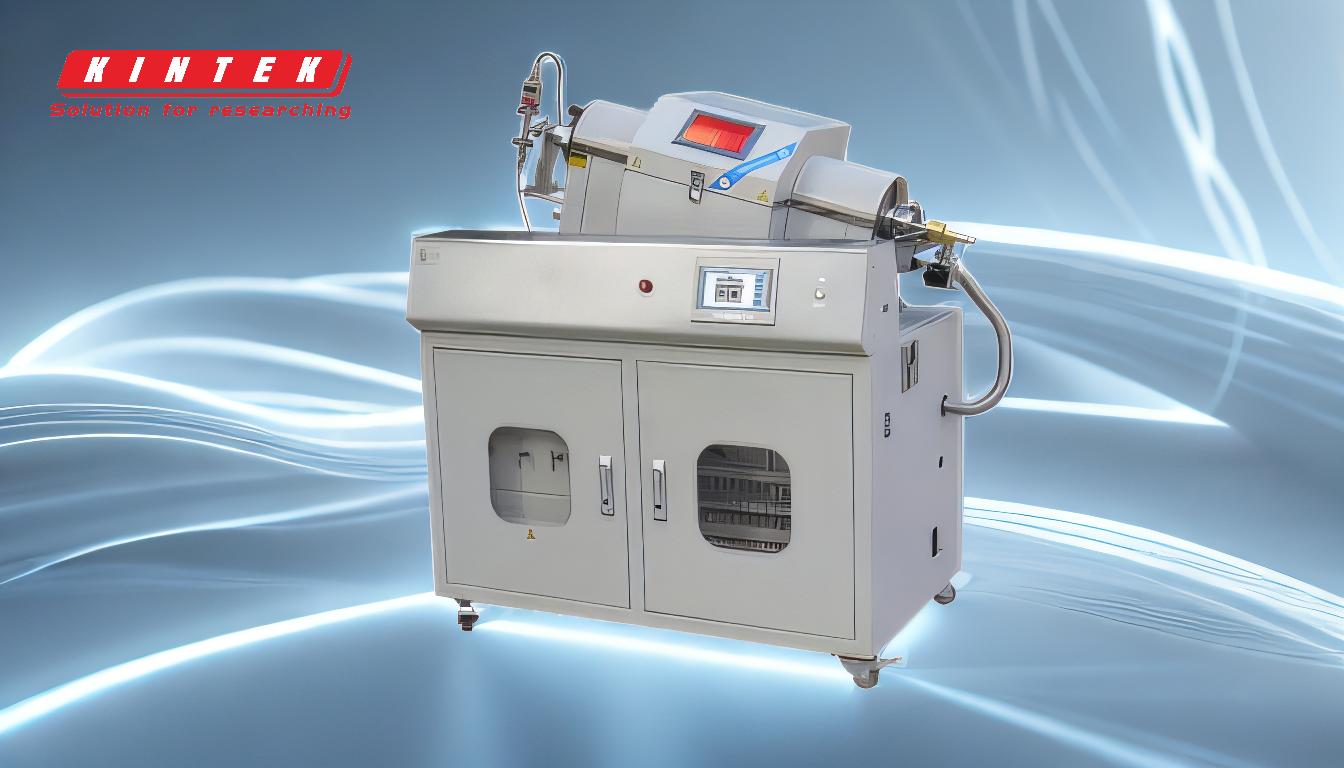
-
Process Mechanisms:
-
Chemical Deposition (CVD):
- Involves chemical reactions between gaseous precursors to form a solid film on the substrate.
- Requires high temperatures to activate the chemical reactions, often leading to the formation of corrosive gaseous byproducts.
- Examples include thermal CVD, plasma-enhanced CVD (PECVD), and atomic layer deposition (ALD).
-
Physical Deposition (PVD):
- Involves the physical transfer of material from a source (e.g., sputtering or evaporation) to the substrate.
- Does not rely on chemical reactions, allowing deposition at lower temperatures.
- Examples include sputtering, evaporation, and electron beam physical vapor deposition (EBPVD).
-
Chemical Deposition (CVD):
-
Temperature Requirements:
-
CVD:
- Typically requires high temperatures (often above 500°C) to facilitate chemical reactions and film growth.
- High temperatures can limit the types of substrates that can be used, as some materials may degrade or warp under such conditions.
-
PVD:
- Can be performed at much lower temperatures, making it suitable for heat-sensitive substrates.
- Lower temperatures also reduce the risk of substrate damage or deformation.
-
CVD:
-
Film Purity and Impurities:
-
CVD:
- The chemical reactions involved can introduce impurities into the film, especially if the precursors or reaction conditions are not carefully controlled.
- Corrosive byproducts may also form, requiring additional steps to manage waste and ensure safety.
-
PVD:
- Generally produces films with higher purity since the process is based on physical transfer rather than chemical reactions.
- No corrosive byproducts are generated, simplifying waste management and reducing safety concerns.
-
CVD:
-
Deposition Rates:
-
CVD:
- Typically offers higher deposition rates compared to PVD, making it suitable for applications requiring thick films.
- However, the rate can vary depending on the specific CVD technique and process parameters.
-
PVD:
- Generally has lower deposition rates, although techniques like EBPVD can achieve rates ranging from 0.1 to 100 μm/min.
- The lower rates are often offset by the ability to produce high-quality, uniform films.
-
CVD:
-
Material Utilization Efficiency:
-
CVD:
- Material utilization efficiency can be lower due to the formation of byproducts and potential waste of precursor gases.
-
PVD:
- Techniques like EBPVD offer very high material utilization efficiency, making them cost-effective for certain applications.
-
CVD:
-
Applications:
-
CVD:
- Commonly used in semiconductor manufacturing, coating of tools, and production of thin films for optical and electronic devices.
- Suitable for applications requiring high-temperature stability and complex chemical compositions.
-
PVD:
- Widely used in the production of thin films for microelectronics, optics, and decorative coatings.
- Ideal for applications requiring high-purity films and compatibility with heat-sensitive substrates.
-
CVD:
By understanding these key differences, equipment and consumable purchasers can make informed decisions about which deposition method best suits their specific needs, balancing factors such as temperature requirements, film purity, deposition rates, and material efficiency.
Summary Table:
Aspect | Chemical Deposition (CVD) | Physical Deposition (PVD) |
---|---|---|
Process Mechanism | Relies on chemical reactions between gaseous precursors to form a solid film on the substrate. | Involves physical transfer of material from a source to the substrate (e.g., sputtering). |
Temperature | High temperatures (often >500°C) required, limiting substrate compatibility. | Lower temperatures, suitable for heat-sensitive substrates. |
Film Purity | Potential impurities due to chemical reactions; corrosive byproducts may form. | Higher purity films; no corrosive byproducts. |
Deposition Rates | Higher rates, suitable for thick films. | Lower rates, but produces high-quality, uniform films. |
Material Efficiency | Lower efficiency due to byproducts and wasted precursor gases. | High efficiency, especially with techniques like EBPVD. |
Applications | Semiconductor manufacturing, tool coatings, optical/electronic devices. | Microelectronics, optics, decorative coatings, and heat-sensitive substrates. |
Need help choosing the right deposition method for your application? Contact our experts today!