Diamond-Like Carbon (DLC) coating is applied using a process that involves the use of hydrocarbons, which are compounds of hydrogen and carbon. These elements are introduced into a plasma environment where they remain attached until they exit the plasma and disperse onto the surface of the substrate. Upon reaching the surface, they recombine to form a hard, durable coating. This process is typically carried out in a vacuum chamber using techniques similar to Physical Vapor Deposition (PVD), which includes steps like vaporization, reaction, and deposition. The resulting DLC coating is known for its high hardness, low coefficient of friction, and excellent performance in corrosive environments.
Key Points Explained:
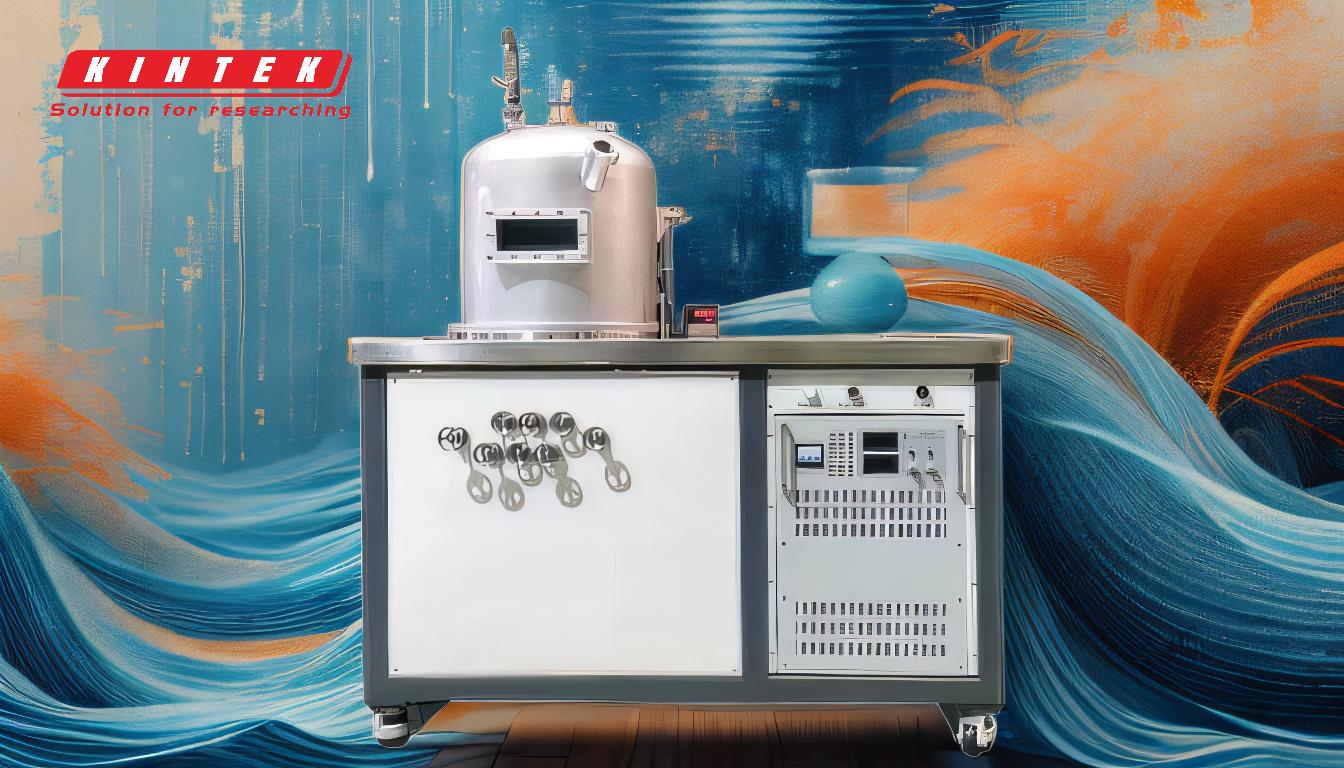
-
Introduction of Hydrocarbons:
- Process: Hydrocarbons, which are compounds of hydrogen and carbon, are introduced into a plasma environment.
- Mechanism: These elements remain attached while in the plasma but disperse onto the substrate surface upon exiting the plasma.
- Outcome: The dispersed elements recombine on the surface to form a hard, durable coating.
-
Plasma Environment:
- Role: The plasma environment is crucial for the initial attachment and subsequent dispersion of the hydrocarbon elements.
- Function: It ensures that the hydrocarbons are in a state where they can effectively coat the substrate upon exiting the plasma.
-
Recombination on Surface:
- Process: Once the hydrocarbons exit the plasma, they spray around the surface like rain.
- Mechanism: The elements recombine on the substrate surface to form the DLC coating.
- Characteristics: This recombination results in a coating with high hardness and other desirable properties.
-
Similarity to PVD Process:
- Steps: The DLC coating process shares similarities with the PVD process, which includes vaporization, reaction, and deposition.
- Vaporization: The target material is converted into its vapor phase.
- Reaction: The properties of the coating, such as hardness and color, are determined during this phase.
- Deposition: The vapor condenses to form a thin film on the substrate.
-
Vacuum Chamber:
- Environment: The process is carried out in a vacuum chamber to create a high-vacuum environment.
-
Steps:
- Placement: The target material is placed in the vacuum chamber.
- Evacuation: The chamber is evacuated to create a high-vacuum environment.
- Bombardment: The target material is bombarded with electrons, ions, or photons to vaporize it.
- Condensation: The vaporized material condenses on the substrate to form a thin film.
- Purging: The chamber is purged with inert gas to remove residual vapors.
-
Properties of DLC Coating:
- Hardness: The coating is known for its high hardness, which is a result of the recombination of carbon and hydrogen elements.
- Friction: It has a low coefficient of friction, making it ideal for applications requiring smooth sliding properties.
- Corrosion Resistance: The coating performs well in corrosive environments, enhancing the durability of the substrate.
-
Applications:
- Functional: DLC coatings are used to enhance sliding properties in various mechanical applications.
- Decorative: They can also be used for decorative purposes, providing a black finish with special hardness characteristics.
-
Bonding Characteristics:
- Sp3 Bonds: These are diamond-like carbon bonds, contributing to the high hardness of the coating.
- Sp2 Bonds: These are graphite-like carbon bonds, which contribute to the low friction properties.
By understanding these key points, one can appreciate the complexity and effectiveness of the DLC coating process, which combines advanced material science with precise engineering techniques to produce coatings with superior properties.
Summary Table:
Key Aspect | Details |
---|---|
Hydrocarbons | Compounds of hydrogen and carbon introduced into a plasma environment. |
Plasma Environment | Ensures attachment and dispersion of hydrocarbons onto the substrate. |
Recombination on Surface | Hydrocarbons recombine to form a hard, durable DLC coating. |
PVD Process Similarity | Involves vaporization, reaction, and deposition in a vacuum chamber. |
Properties of DLC | High hardness, low friction, and excellent corrosion resistance. |
Applications | Functional (sliding properties) and decorative (black finish with hardness). |
Bonding Characteristics | Sp3 (diamond-like) and Sp2 (graphite-like) bonds for hardness and friction. |
Interested in DLC coatings for your applications? Contact us today to learn more!