Film thickness in evaporation is controlled through a combination of factors, including the temperature of the evaporant, the deposition rate, the distance between the evaporant and the substrate, and the geometry of the evaporation chamber. Additionally, vacuum pressure, substrate temperature, and surface preparation play critical roles in ensuring uniform and high-quality film deposition. Techniques such as electron beam evaporation, multi-source evaporation, and reaction evaporation further allow for precise control over film characteristics. Proper management of these variables ensures that the desired film thickness and properties are achieved.
Key Points Explained:
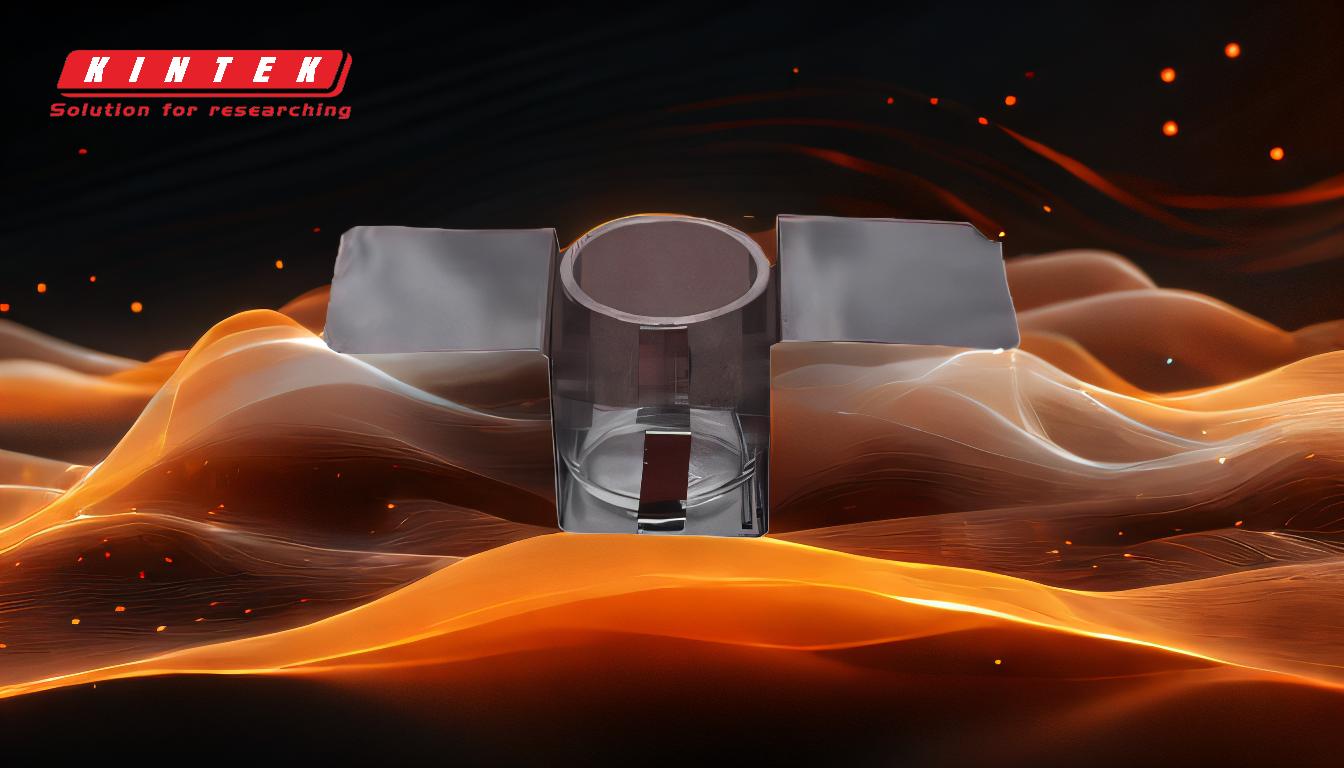
-
Temperature of the Evaporant:
- The temperature of the evaporant directly influences the rate at which the material vaporizes. Higher temperatures increase the evaporation rate, leading to faster deposition. However, excessively high temperatures can cause non-uniform deposition or damage the substrate. Precise temperature control is essential to achieve the desired film thickness and quality.
-
Deposition Rate:
- The deposition rate refers to how quickly the evaporated material is deposited onto the substrate. A higher deposition rate can improve film purity by minimizing the inclusion of gaseous impurities. However, too high a rate can lead to poor film adhesion and non-uniform thickness. Adjusting the deposition rate is a key method for controlling film thickness.
-
Distance Between Evaporant and Substrate:
- The distance between the evaporant source and the substrate affects the uniformity and thickness of the deposited film. A shorter distance can lead to thicker films but may also cause non-uniformity due to the geometry of the evaporation chamber. Conversely, a longer distance may result in thinner, more uniform films but can reduce deposition efficiency.
-
Vacuum Pressure:
- The pressure inside the vacuum chamber plays a critical role in film deposition. A higher degree of vacuum (lower pressure) improves the mean free path of the evaporant molecules, reducing collisions with residual gases and minimizing impurities in the film. This leads to better film quality and more uniform thickness.
-
Substrate Temperature:
- The temperature of the substrate influences the mobility of the deposited atoms. Heating the substrate above 150 °C can improve film adhesion and uniformity by providing sufficient energy for the atoms to move and form a stable film. Substrate temperature control is particularly important for achieving high-quality thin films.
-
Substrate Surface Preparation:
- The surface condition of the substrate affects film uniformity and adhesion. A rough or contaminated substrate surface can lead to non-uniform deposition and poor film quality. Proper cleaning and preparation of the substrate surface are essential for achieving the desired film thickness and properties.
-
Evaporation Techniques:
- Various evaporation techniques can be employed to achieve specific film characteristics:
- Electron Beam Evaporation: Uses a focused electron beam to heat the evaporant, allowing precise control over the evaporation process.
- Multi-Source Evaporation: Utilizes multiple evaporation sources to deposit different materials simultaneously, enabling the creation of composite films.
- Instant Evaporation: Rapidly heats multi-element materials to achieve specific film compositions.
- Laser Evaporation: Uses high-power laser pulses to vaporize the material, providing rapid and localized heating.
- Reaction Evaporation: Introduces reactive gases into the chamber to form compound films during deposition.
- Various evaporation techniques can be employed to achieve specific film characteristics:
-
Geometry of the Evaporation Chamber:
- The design and geometry of the evaporation chamber influence the distribution and uniformity of the deposited film. Collisions with residual gases and the spatial arrangement of the evaporant and substrate can lead to thickness variations. Optimizing the chamber geometry is essential for achieving uniform film thickness.
By carefully controlling these factors, manufacturers can achieve precise control over film thickness and ensure the production of high-quality thin films with the desired properties.
Summary Table:
Factor | Role in Film Thickness Control |
---|---|
Temperature of the Evaporant | Higher temperatures increase evaporation rate but require precise control to avoid non-uniformity. |
Deposition Rate | Higher rates improve purity but must be balanced to ensure uniform thickness and adhesion. |
Distance Between Evaporant and Substrate | Shorter distances increase thickness; longer distances improve uniformity but reduce efficiency. |
Vacuum Pressure | Lower pressure reduces impurities, improving film quality and uniformity. |
Substrate Temperature | Heating above 150 °C enhances adhesion and uniformity. |
Substrate Surface Preparation | Proper cleaning ensures uniform deposition and high-quality films. |
Evaporation Techniques | Techniques like electron beam and multi-source evaporation enable precise control over film properties. |
Geometry of the Evaporation Chamber | Optimized chamber design ensures uniform film thickness distribution. |
Ready to achieve precise film thickness control? Contact our experts today to optimize your evaporation process!