Artificial graphite is manufactured through a series of controlled processes that transform carbon-rich materials into high-purity graphite. The process typically involves the selection of raw materials, carbonization, graphitization, and post-treatment. Raw materials such as petroleum coke or coal tar pitch are first carbonized at high temperatures to remove volatile components, leaving behind a carbon-rich residue. This residue is then graphitized at even higher temperatures, often exceeding 2500°C, to rearrange the carbon atoms into the crystalline structure of graphite. The final product may undergo additional treatments like purification or coating to enhance its properties. The use of advanced equipment, such as a graphite furnace, is critical in achieving the high temperatures required for graphitization.
Key Points Explained:
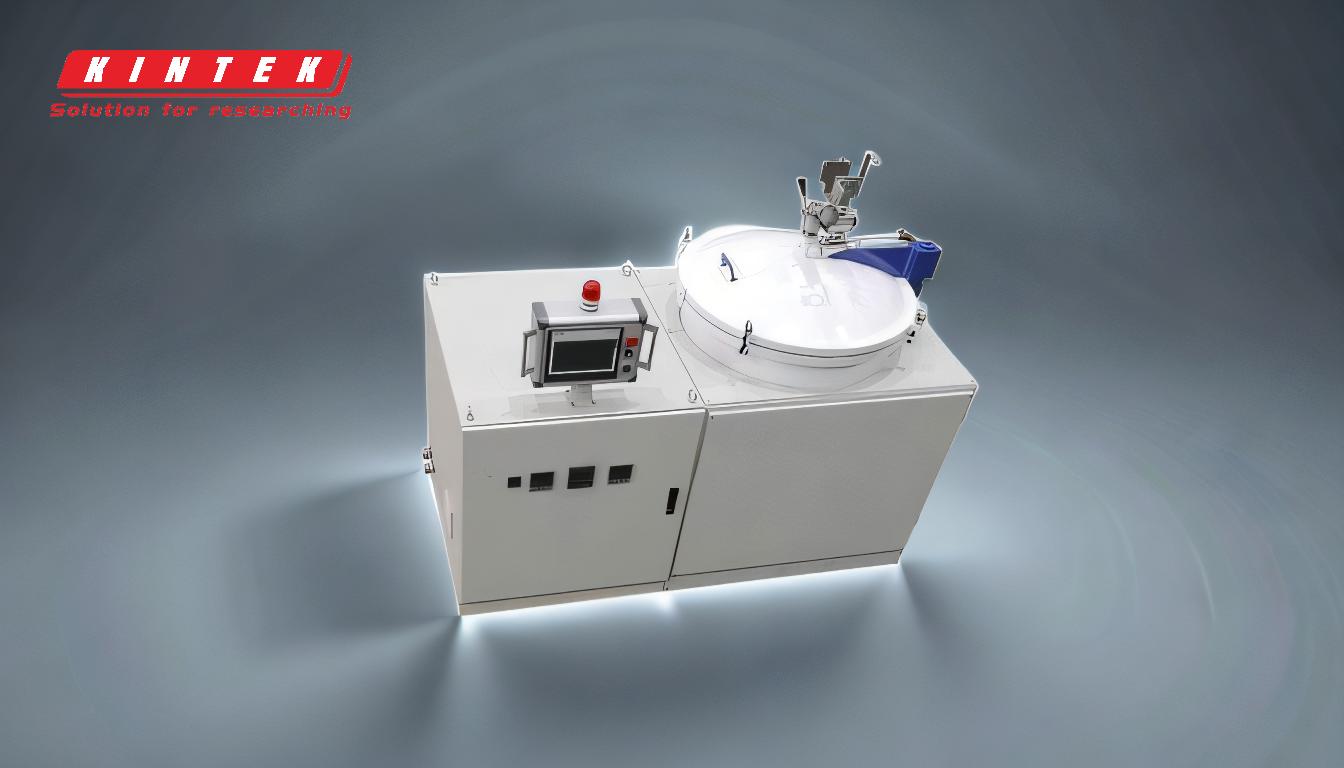
-
Raw Material Selection:
- The manufacturing process begins with the selection of high-quality carbon-rich raw materials. Common choices include petroleum coke, coal tar pitch, and natural graphite. These materials are chosen for their high carbon content and low impurity levels, which are essential for producing high-purity artificial graphite.
-
Carbonization:
- The selected raw materials are subjected to carbonization, a process that involves heating the materials to temperatures between 500°C and 1200°C in an oxygen-free environment. This step removes volatile components such as hydrogen, oxygen, and nitrogen, leaving behind a carbon-rich residue. The carbonization process is crucial for increasing the carbon content and preparing the material for graphitization.
-
Graphitization:
- Graphitization is the core step in the manufacturing process, where the carbonized material is heated to extremely high temperatures, typically between 2500°C and 3000°C. This is often done in a specialized graphite furnace, which can withstand and maintain these extreme temperatures. During graphitization, the carbon atoms rearrange into a crystalline graphite structure, giving the material its characteristic properties such as high thermal conductivity, electrical conductivity, and lubricity.
-
Post-Treatment:
- After graphitization, the artificial graphite may undergo additional treatments to enhance its properties. These treatments can include purification to remove any remaining impurities, coating to improve surface properties, or machining to achieve specific shapes and sizes. Post-treatment processes are tailored to meet the requirements of the intended application, whether it be for use in batteries, electrodes, or other industrial applications.
-
Quality Control:
- Throughout the manufacturing process, rigorous quality control measures are implemented to ensure the final product meets the desired specifications. This includes monitoring the temperature and atmosphere during carbonization and graphitization, as well as testing the final product for properties such as purity, density, and electrical conductivity.
-
Applications of Artificial Graphite:
- Artificial graphite is used in a wide range of applications due to its unique properties. It is commonly used in the production of electrodes for electric arc furnaces, as a moderator in nuclear reactors, and in the manufacture of lithium-ion batteries. Its high thermal and electrical conductivity, along with its chemical stability, make it an essential material in many high-tech industries.
In summary, the artificial manufacturing of graphite is a complex process that involves careful selection of raw materials, precise control of high-temperature treatments, and rigorous quality control. The use of specialized equipment like a graphite furnace is essential in achieving the high temperatures required for graphitization, ensuring the production of high-quality artificial graphite for various industrial applications.
Summary Table:
Step | Description | Temperature Range | Key Outcome |
---|---|---|---|
Raw Material Selection | High-quality carbon-rich materials like petroleum coke or coal tar pitch are chosen. | - | High carbon content and low impurities. |
Carbonization | Heating raw materials to 500°C–1200°C in an oxygen-free environment. | 500°C–1200°C | Volatile components removed, leaving a carbon-rich residue. |
Graphitization | Heating carbonized material to 2500°C–3000°C in a graphite furnace. | 2500°C–3000°C | Carbon atoms rearrange into a crystalline graphite structure. |
Post-Treatment | Purification, coating, or machining to enhance properties. | - | Improved purity, surface properties, and tailored shapes for applications. |
Quality Control | Rigorous testing for purity, density, and electrical conductivity. | - | Ensures final product meets specifications. |
Applications | Used in electrodes, nuclear reactors, and lithium-ion batteries. | - | High thermal/electrical conductivity and chemical stability. |
Need high-quality artificial graphite for your industry? Contact us today to learn more about our advanced manufacturing solutions!