Thin films are formed through a variety of deposition techniques, which can be broadly categorized into chemical and physical methods. These techniques allow for precise control over the thickness, composition, and properties of the films, making them suitable for a wide range of applications, from semiconductors to flexible solar cells and OLEDs. The main methods include chemical vapor deposition (CVD), physical vapor deposition (PVD), and other specialized techniques like spin coating, sputtering, and atomic layer deposition (ALD). Each method has its own advantages and is chosen based on the specific requirements of the application.
Key Points Explained:
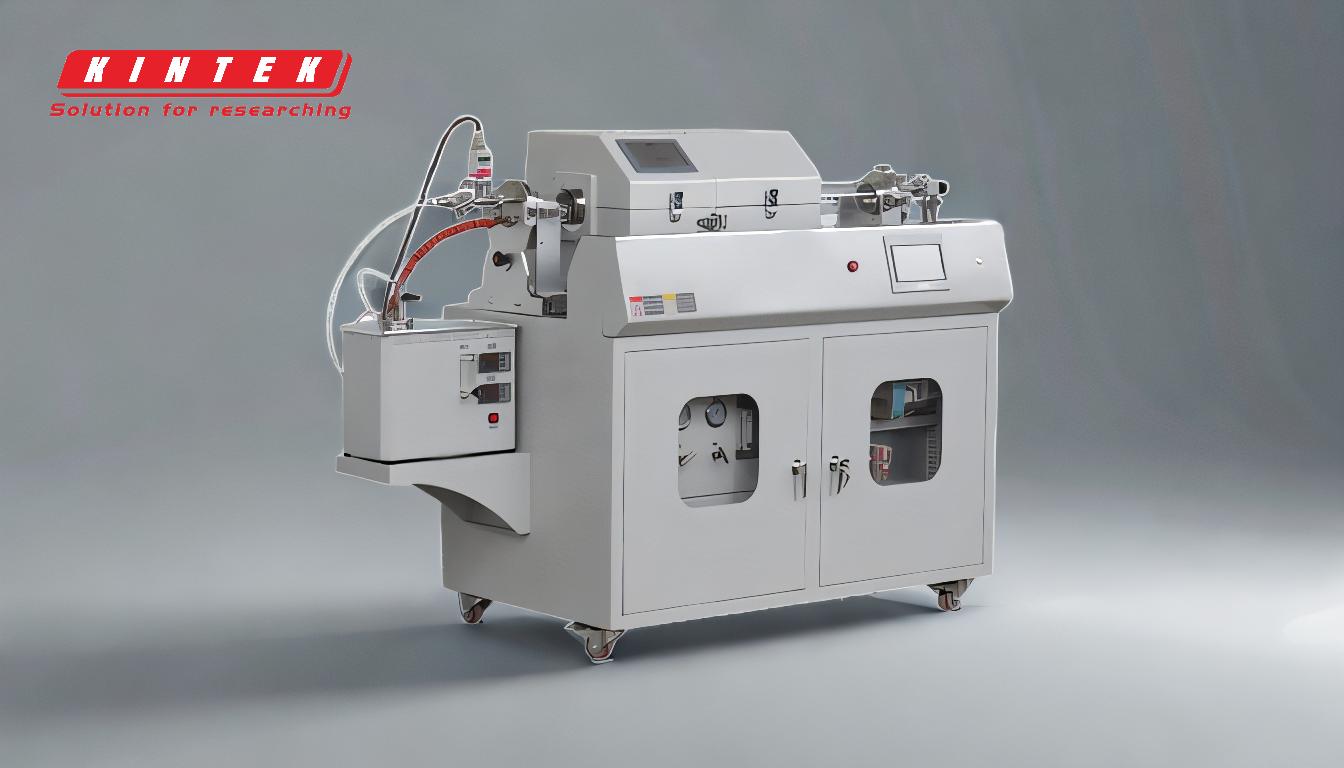
-
Chemical Deposition Methods:
- Chemical Vapor Deposition (CVD): This method involves the use of chemical reactions to produce high-purity thin films. Precursor gases are introduced into a reaction chamber, where they react on the substrate surface to form the desired film. Variants like Plasma-Enhanced CVD (PECVD) use plasma to enhance the reaction at lower temperatures.
- Sol-Gel: This technique involves the transition of a solution (sol) into a gel-like state, which is then dried and sintered to form a thin film. It is commonly used for creating oxide films.
- Dip Coating and Spin Coating: These methods involve immersing or spinning a substrate in a solution, which is then dried to form a thin film. Spin coating is particularly useful for creating uniform films with controlled thickness.
-
Physical Deposition Methods:
-
Physical Vapor Deposition (PVD): This category includes techniques where a solid material is vaporized in a vacuum and then deposited onto a substrate. Common PVD methods include:
- Sputtering: A target material is bombarded with ions, causing atoms to be ejected and deposited onto the substrate.
- Thermal Evaporation: The material is heated to its evaporation point in a vacuum, and the vapor condenses on the substrate.
- Electron Beam Evaporation: An electron beam is used to heat the material, causing it to evaporate and deposit onto the substrate.
- Molecular Beam Epitaxy (MBE): This is a highly controlled form of evaporation used to grow high-quality crystalline films, layer by layer.
- Pulsed Laser Deposition (PLD): A high-power laser pulse is used to ablate material from a target, which is then deposited onto the substrate.
-
Physical Vapor Deposition (PVD): This category includes techniques where a solid material is vaporized in a vacuum and then deposited onto a substrate. Common PVD methods include:
-
Hybrid and Specialized Techniques:
- Atomic Layer Deposition (ALD): This technique allows for the deposition of films one atomic layer at a time, providing exceptional control over thickness and composition. It is particularly useful for creating ultra-thin films with high uniformity.
- Magnetron Sputtering: A variation of sputtering that uses magnetic fields to enhance the ionization of the sputtering gas, increasing the deposition rate and improving film quality.
- Drop Casting and Oil Bathing: These are simpler techniques where a solution is dropped onto a substrate or the substrate is immersed in a solution, followed by drying to form a thin film.
-
Applications and Considerations:
- Semiconductors: Techniques like CVD and MBE are commonly used in semiconductor manufacturing due to their ability to produce high-purity and high-quality films.
- Flexible Electronics: Methods like spin coating and PVD are used to create thin films for flexible solar cells and OLEDs, where flexibility and uniformity are critical.
- Optical Coatings: Sputtering and evaporation are often used to create thin films for optical applications, such as anti-reflective coatings and mirrors.
-
Control and Precision:
- Thickness Control: Techniques like ALD and spin coating offer precise control over film thickness, which is crucial for applications requiring specific optical, electrical, or mechanical properties.
- Composition Control: Methods like CVD and MBE allow for precise control over the chemical composition of the film, enabling the creation of complex multi-layer structures.
In summary, the formation of thin films involves a variety of deposition techniques, each with its own set of advantages and applications. The choice of method depends on the desired film properties, such as thickness, composition, and uniformity, as well as the specific requirements of the application.
Summary Table:
Category | Techniques | Key Features |
---|---|---|
Chemical Deposition | CVD, Sol-Gel, Dip Coating, Spin Coating | High-purity films, uniform thickness, oxide film creation |
Physical Deposition | Sputtering, Thermal Evaporation, Electron Beam Evaporation, MBE, PLD | Vacuum-based, precise layer-by-layer growth, high-quality crystalline films |
Hybrid Techniques | ALD, Magnetron Sputtering, Drop Casting, Oil Bathing | Atomic-level control, enhanced deposition rates, simple and cost-effective |
Applications | Semiconductors, Flexible Electronics, Optical Coatings | High-purity, flexibility, anti-reflective coatings |
Control & Precision | Thickness Control (ALD, Spin Coating), Composition Control (CVD, MBE) | Precise thickness and composition for optical, electrical, and mechanical needs |
Need help selecting the right thin film deposition technique for your application? Contact our experts today!