Vacuum pressure measurement is a critical process in various scientific, industrial, and engineering applications. It involves determining the pressure levels in a vacuum environment, which can range from atmospheric pressure down to ultra-high vacuum conditions. The measurement is typically performed using specialized instruments such as vacuum gauges, which are designed to operate effectively within specific pressure ranges. These instruments utilize different principles, including mechanical, thermal, and ionization techniques, to accurately measure pressure. Understanding the methods and instruments used for vacuum pressure measurement is essential for ensuring proper system performance and achieving desired experimental or operational outcomes.
Key Points Explained:
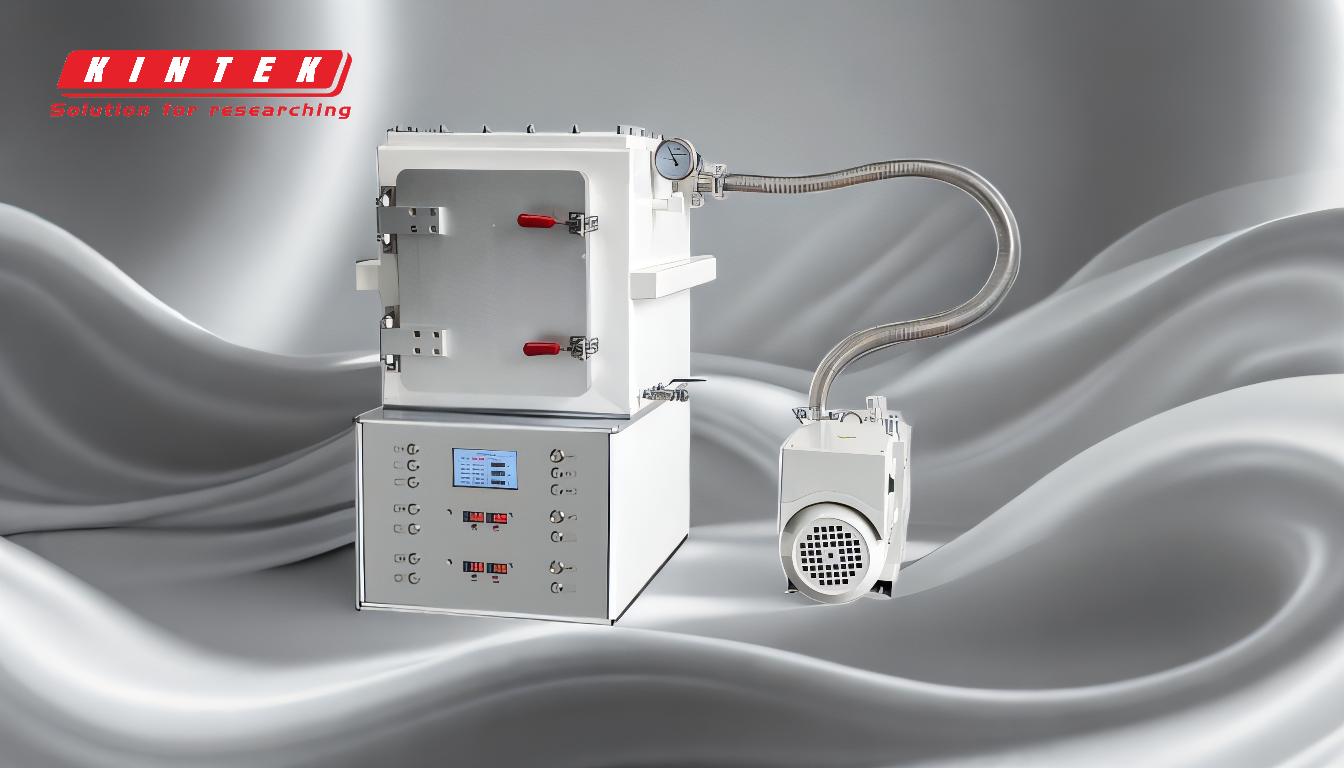
-
Definition of Vacuum Pressure:
- Vacuum pressure refers to the pressure below atmospheric pressure, typically measured in units such as Pascals (Pa), Torr, or millibar (mbar).
- It is often expressed as absolute pressure, which is measured relative to a perfect vacuum, or gauge pressure, which is measured relative to atmospheric pressure.
-
Types of Vacuum Gauges:
- Mechanical Gauges: These include instruments like Bourdon gauges and diaphragm gauges, which measure pressure by detecting the physical deformation of a mechanical element. They are suitable for measuring relatively higher vacuum pressures.
- Thermal Gauges: Instruments such as Pirani gauges and thermocouple gauges measure pressure based on the thermal conductivity of gases. They are effective in the medium vacuum range.
- Ionization Gauges: These gauges, including hot cathode and cold cathode types, measure pressure by ionizing gas molecules and detecting the resulting ion current. They are used for high and ultra-high vacuum measurements.
-
Measurement Principles:
- Mechanical Deformation: Mechanical gauges rely on the deformation of a sensing element, such as a Bourdon tube or diaphragm, which changes shape in response to pressure differences.
- Thermal Conductivity: Thermal gauges measure the heat loss from a heated element, which varies with the pressure and type of gas present in the vacuum.
- Ionization: Ionization gauges ionize gas molecules using an electric field or electron beam and measure the resulting ion current, which is proportional to the gas pressure.
-
Calibration and Accuracy:
- Vacuum gauges require regular calibration to ensure accurate measurements. Calibration is typically performed using known pressure standards or reference gauges.
- Factors such as temperature, gas composition, and gauge sensitivity can affect measurement accuracy, so these must be carefully controlled and accounted for during calibration.
-
Applications of Vacuum Pressure Measurement:
- Scientific Research: Vacuum pressure measurement is essential in fields such as physics, chemistry, and materials science, where experiments are often conducted under controlled vacuum conditions.
- Industrial Processes: Industries such as semiconductor manufacturing, vacuum coating, and food packaging rely on precise vacuum pressure measurement to ensure product quality and process efficiency.
- Space Simulation: Vacuum chambers used for testing spacecraft components require accurate pressure measurement to simulate the conditions of outer space.
-
Challenges in Vacuum Pressure Measurement:
- Range Limitations: Different gauges are optimized for specific pressure ranges, so selecting the appropriate gauge for a given application is crucial.
- Gas Dependency: The response of some gauges, particularly thermal and ionization types, can vary depending on the type of gas present in the vacuum.
- Environmental Factors: Temperature fluctuations, vibrations, and electromagnetic interference can affect gauge performance and measurement accuracy.
-
Future Trends in Vacuum Pressure Measurement:
- Miniaturization: Advances in microfabrication techniques are leading to the development of smaller, more compact vacuum gauges suitable for portable and space-constrained applications.
- Digital Integration: Modern vacuum gauges are increasingly incorporating digital interfaces and connectivity features, allowing for remote monitoring and data logging.
- Enhanced Sensitivity: Ongoing research aims to improve the sensitivity and accuracy of vacuum gauges, particularly for ultra-high vacuum applications, through innovations in sensor technology and signal processing.
By understanding the principles, instruments, and challenges associated with vacuum pressure measurement, professionals can make informed decisions when selecting and using vacuum gauges for their specific applications. This knowledge is crucial for achieving accurate and reliable pressure measurements in a wide range of scientific and industrial contexts.
Summary Table:
Aspect | Details |
---|---|
Definition | Pressure below atmospheric, measured in Pascals (Pa), Torr, or millibar (mbar). |
Types of Gauges | Mechanical (Bourdon, diaphragm), Thermal (Pirani, thermocouple), Ionization (hot/cold cathode). |
Measurement Principles | Mechanical deformation, thermal conductivity, ionization. |
Applications | Scientific research, semiconductor manufacturing, space simulation. |
Challenges | Range limitations, gas dependency, environmental factors. |
Future Trends | Miniaturization, digital integration, enhanced sensitivity. |
Need help selecting the right vacuum gauge for your application? Contact our experts today!