The production and installation of a continuous pyrolysis plant, such as one used for biochar production, involves a significant timeline. The production period for such a plant is approximately 100 working days, while the installation period takes about 60 working days. This means that from the start of production to the completion of installation, the total time required is around 160 working days. This timeline is crucial for planning and scheduling in projects involving biochar pyrolysis.
Key Points Explained:
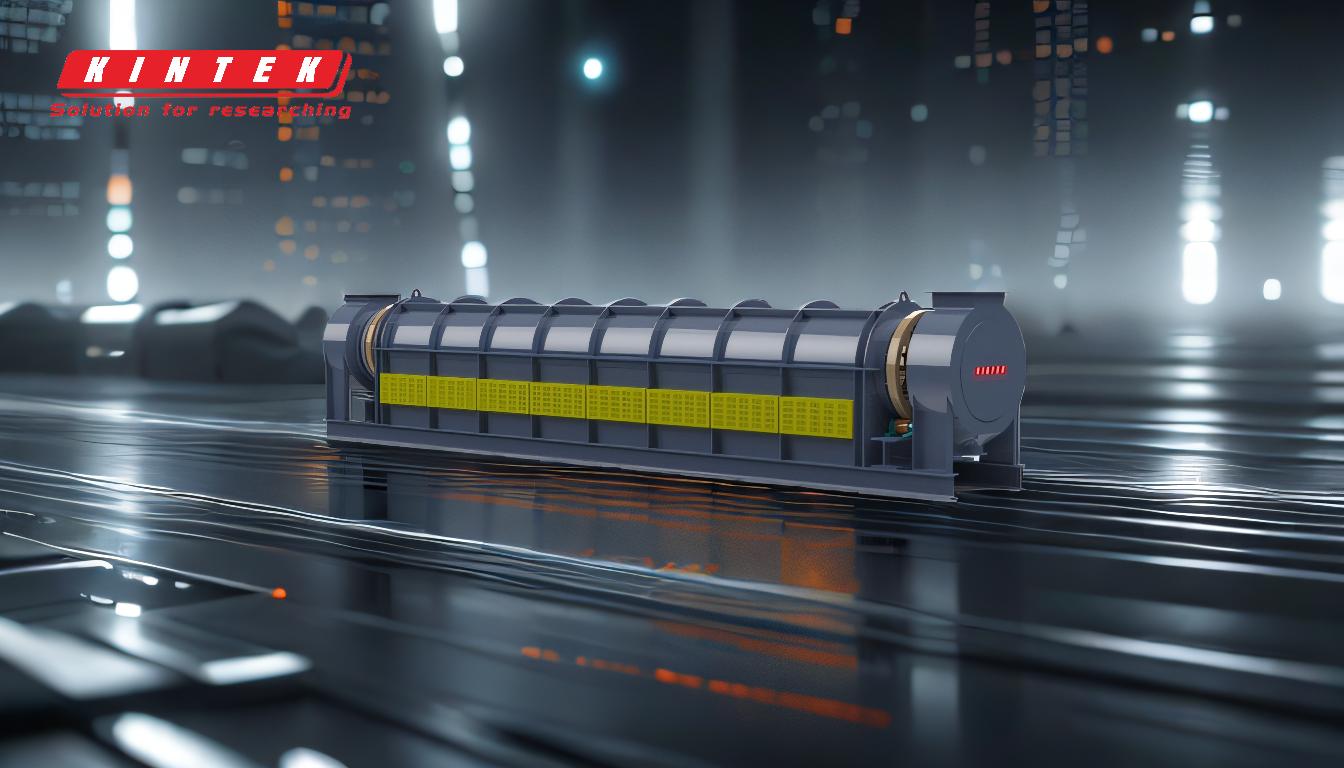
-
Production Period:
- The production period for a continuous pyrolysis plant is about 100 working days. This duration includes the manufacturing of all components, assembly, and initial testing to ensure the plant meets operational standards.
- This phase is critical as it involves the fabrication of specialized equipment designed to handle high temperatures and the chemical processes involved in pyrolysis.
-
Installation Period:
- The installation period is approximately 60 working days. This phase involves the physical setup of the plant at the designated site, including the installation of reactors, condensers, and other necessary equipment.
- Installation also includes the integration of control systems and safety mechanisms, which are essential for the efficient and safe operation of the pyrolysis plant.
-
Total Timeline:
- Combining both production and installation, the total time required is around 160 working days. This timeline is important for project planning, especially in industries where time is a critical factor.
- Understanding this timeline helps in coordinating with suppliers, contractors, and other stakeholders to ensure a smooth transition from production to operational phases.
-
Considerations for Biochar Pyrolysis:
- When considering biochar pyrolysis, it's important to note that the pyrolysis process itself can vary in duration depending on the feedstock and desired properties of the biochar.
- However, the focus here is on the production and installation of the pyrolysis plant, which is a prerequisite for any biochar production activity.
By understanding these key points, stakeholders can better plan and manage the timeline for setting up a continuous pyrolysis plant, ensuring that all phases are executed efficiently and effectively.
Summary Table:
Phase | Duration | Key Activities |
---|---|---|
Production | 100 days | Manufacturing, assembly, and testing of pyrolysis plant components. |
Installation | 60 days | Setup of reactors, condensers, control systems, and safety mechanisms. |
Total Timeline | 160 days | Combined production and installation for a fully operational pyrolysis plant. |
Ready to streamline your biochar pyrolysis project? Contact us today for expert guidance and support!