The cost of DLC (Diamond-Like Carbon) coating varies significantly depending on several factors, including the type of DLC coating, the size and complexity of the part being coated, the required thickness, and the specific application. Generally, prices can range from $50 to $500 per part or more, with more complex or larger parts costing more due to the additional preparation and coating time required. High-performance applications, such as those in the automotive or aerospace industries, may also incur higher costs due to the need for specialized equipment and stringent quality control measures.
Key Points Explained:
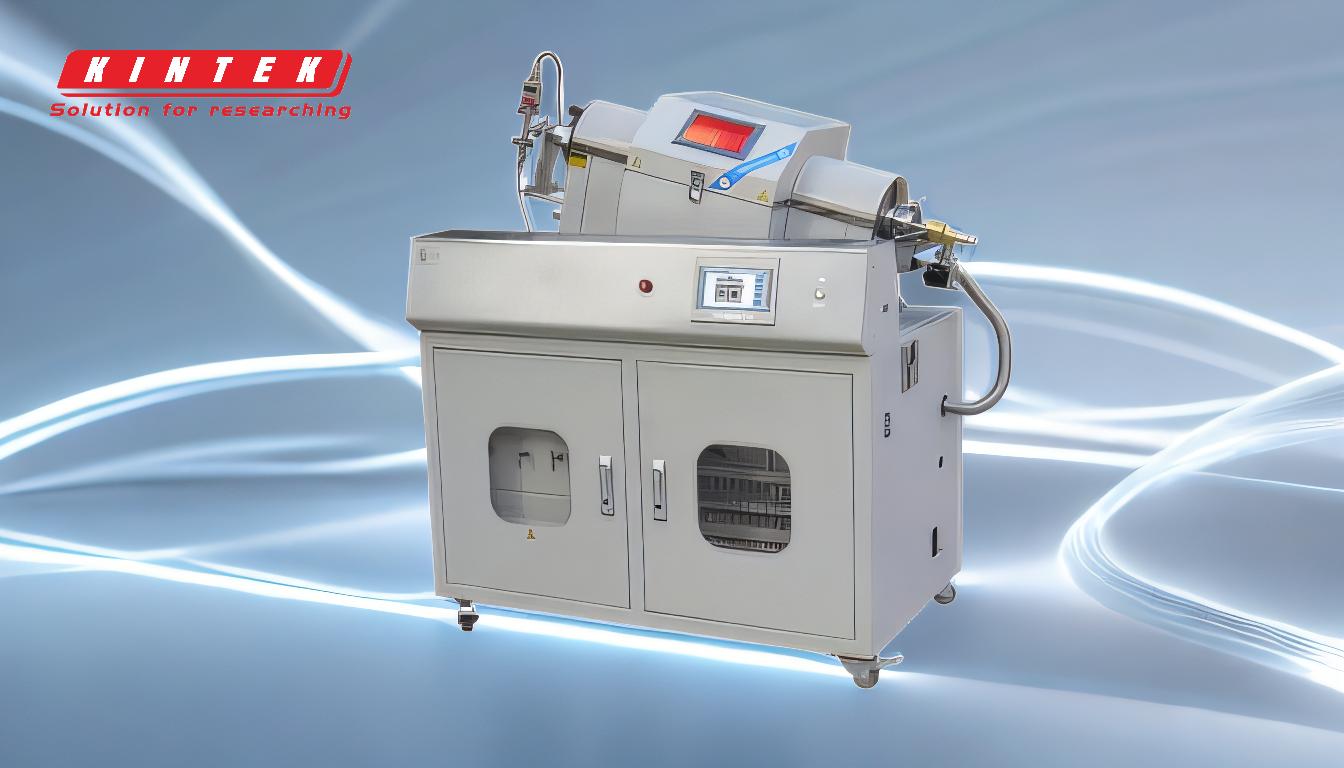
-
Types of DLC Coatings and Their Impact on Cost:
- DLC coatings come in various forms, such as hydrogenated (a-C:H) and hydrogen-free (ta-C) coatings, each with different properties and applications.
- The choice of coating type affects the cost because some types require more complex deposition processes or specialized equipment.
- For example, ta-C coatings, which are harder and more wear-resistant, may cost more due to the advanced techniques needed to deposit them.
-
Size and Complexity of the Part:
- Larger parts or those with complex geometries require more coating material and longer processing times, which increases the cost.
- Parts with intricate designs may also need additional preparation, such as masking or surface treatment, to ensure uniform coating application.
-
Coating Thickness and Performance Requirements:
- The thickness of the DLC coating can influence the cost. Thicker coatings require more material and longer deposition times.
- High-performance applications, such as those requiring extreme wear resistance or low friction, may demand thicker or multi-layered coatings, further increasing the cost.
-
Application-Specific Costs:
- The industry and specific application of the coated part play a significant role in determining the cost. For instance, automotive and aerospace applications often require higher-quality coatings with stricter performance criteria, leading to higher costs.
- Custom applications or those requiring specialized testing and quality assurance may also incur additional expenses.
-
Volume and Batch Size:
- The cost per part can decrease with larger batch sizes due to economies of scale. Coating multiple parts in a single run can reduce the overall cost per unit.
- However, small batches or one-off custom jobs may be more expensive on a per-part basis due to setup and preparation costs.
-
Geographical and Supplier Variations:
- The cost of DLC coating can vary based on the geographical location of the supplier and the local market conditions.
- Different suppliers may offer varying levels of service, quality, and expertise, which can affect pricing. It's essential to choose a reputable supplier with experience in the specific type of DLC coating required.
-
Additional Costs to Consider:
- Surface preparation, such as cleaning, polishing, or etching, may be necessary before applying the DLC coating, adding to the overall cost.
- Post-coating treatments, such as heat treatment or additional quality testing, can also increase expenses.
- Shipping and handling costs, especially for large or delicate parts, should be factored into the total cost.
In summary, the cost of DLC coating is influenced by a variety of factors, including the type of coating, part size and complexity, thickness requirements, application specifics, batch size, and supplier location. Understanding these factors can help in making informed decisions when selecting a DLC coating service.
Summary Table:
Factor | Impact on Cost |
---|---|
Type of DLC Coating | Hydrogenated (a-C:H) or hydrogen-free (ta-C); ta-C is costlier due to advanced techniques. |
Part Size & Complexity | Larger or intricate parts require more material and preparation, increasing costs. |
Coating Thickness | Thicker or multi-layered coatings cost more due to material and time requirements. |
Application | High-performance industries (e.g., automotive, aerospace) incur higher costs. |
Batch Size | Larger batches reduce per-part costs; small or custom jobs are more expensive. |
Supplier Location | Costs vary by geography and supplier expertise. |
Additional Costs | Surface prep, post-coating treatments, and shipping add to the total cost. |
Need a precise quote for your DLC coating project? Contact us today to discuss your requirements!