The cost of PVD (Physical Vapor Deposition) coating can vary significantly depending on several factors, including the size of the parts being coated, the type of material being used, the complexity of the coating process, and the specific requirements of the coating (such as thickness, durability, and finish). While the provided reference mentions that the PVD coating process typically takes about half an hour to an hour for each coating, with larger pieces potentially taking up to 2 hours, this information alone does not directly answer the cost question. However, the time required for the process can indirectly influence the cost, as longer processing times can lead to higher labor and operational expenses.
Key Points Explained:
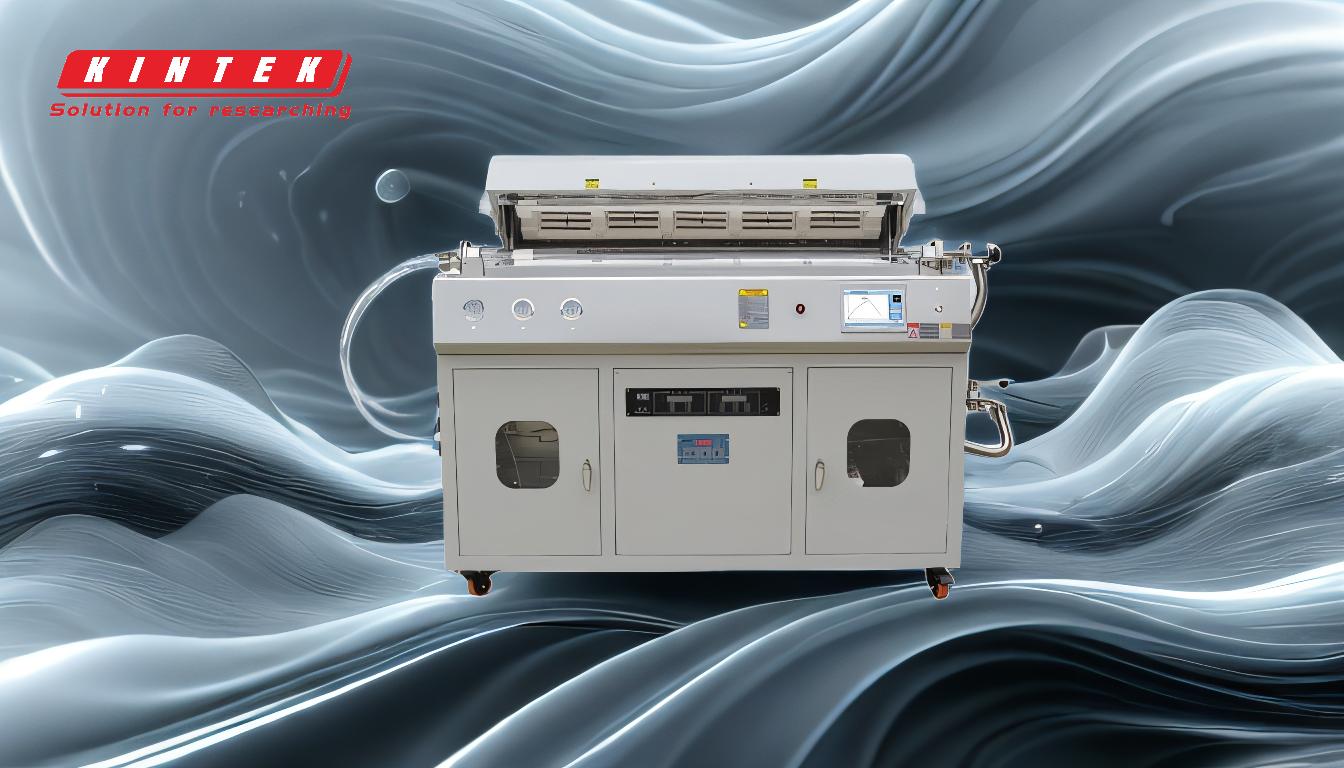
-
Factors Influencing PVD Coating Costs:
- Size of the Parts: Larger parts require more material and time, which can increase the cost. The reference mentions that larger pieces may take up to 2 hours to complete, which would likely result in higher costs compared to smaller parts that take less time.
- Material Type: Different materials used in the PVD process (e.g., titanium, chromium, or aluminum) have varying costs. Some materials may be more expensive due to their rarity or the complexity involved in their application.
- Coating Complexity: More complex coatings, such as those requiring multiple layers or specific finishes (e.g., matte, glossy, or textured), can increase the cost due to the additional steps and precision required.
- Coating Requirements: Specific requirements like thickness, durability, and finish quality can also affect the cost. For example, a thicker coating or one that requires a high level of durability may involve more material and processing time, leading to higher costs.
-
Indirect Cost Factors:
- Labor Costs: The time required for the PVD coating process, as mentioned in the reference, can influence labor costs. Longer processing times mean more labor hours, which can increase the overall cost.
- Operational Costs: The energy consumption and maintenance of the PVD equipment can also contribute to the cost. Longer processing times can lead to higher energy usage and more frequent maintenance, which can add to the overall expense.
-
Estimating PVD Coating Costs:
- Per-Part Cost: In some cases, PVD coating costs are calculated on a per-part basis. This can range from a few dollars for small, simple parts to several hundred dollars for larger, more complex pieces.
- Bulk Discounts: Some companies may offer discounts for large orders, as the fixed costs (like setup and equipment maintenance) can be spread over a larger number of parts, reducing the per-unit cost.
- Custom Quotes: For precise cost estimates, it is often necessary to obtain a custom quote from a PVD coating service provider. They will consider all the factors mentioned above to provide an accurate cost estimate.
-
Comparison with Other Coating Methods:
- PVD vs. CVD: PVD coating is generally more expensive than Chemical Vapor Deposition (CVD) due to the higher precision and quality of the coatings. However, PVD coatings often offer better performance in terms of durability and finish, which can justify the higher cost.
- PVD vs. Electroplating: PVD coatings are typically more expensive than electroplating, but they offer superior adhesion, durability, and resistance to corrosion, making them a preferred choice for high-performance applications.
In summary, the cost of PVD coating is influenced by a variety of factors, including the size and complexity of the parts, the materials used, and the specific requirements of the coating. While the reference provides insight into the time required for the PVD process, this is just one of many factors that contribute to the overall cost. For an accurate estimate, it is best to consult with a PVD coating service provider who can take all relevant factors into account.
Summary Table:
Factor | Impact on Cost |
---|---|
Size of Parts | Larger parts require more material and time, increasing costs. |
Material Type | Rare or complex materials (e.g., titanium) can raise costs. |
Coating Complexity | Multiple layers or specific finishes add to the cost. |
Coating Requirements | Thicker or more durable coatings increase material and processing expenses. |
Labor Costs | Longer processing times lead to higher labor expenses. |
Operational Costs | Energy usage and equipment maintenance contribute to overall costs. |
Bulk Discounts | Large orders may qualify for reduced per-unit costs. |
Custom Quotes | Accurate estimates require consultation with a PVD coating provider. |
Need a precise cost estimate for your PVD coating project? Contact our experts today for a custom quote!