The power consumption of an induction furnace, such as an IGBT induction furnace, is a critical factor for both operational efficiency and cost management. On average, a steel induction furnace consumes approximately 625 kWh per ton of material processed. However, this value can vary depending on factors like furnace design, material type, operating temperature, and process efficiency. Understanding these variables is essential for optimizing energy usage and minimizing costs.
Key Points Explained:
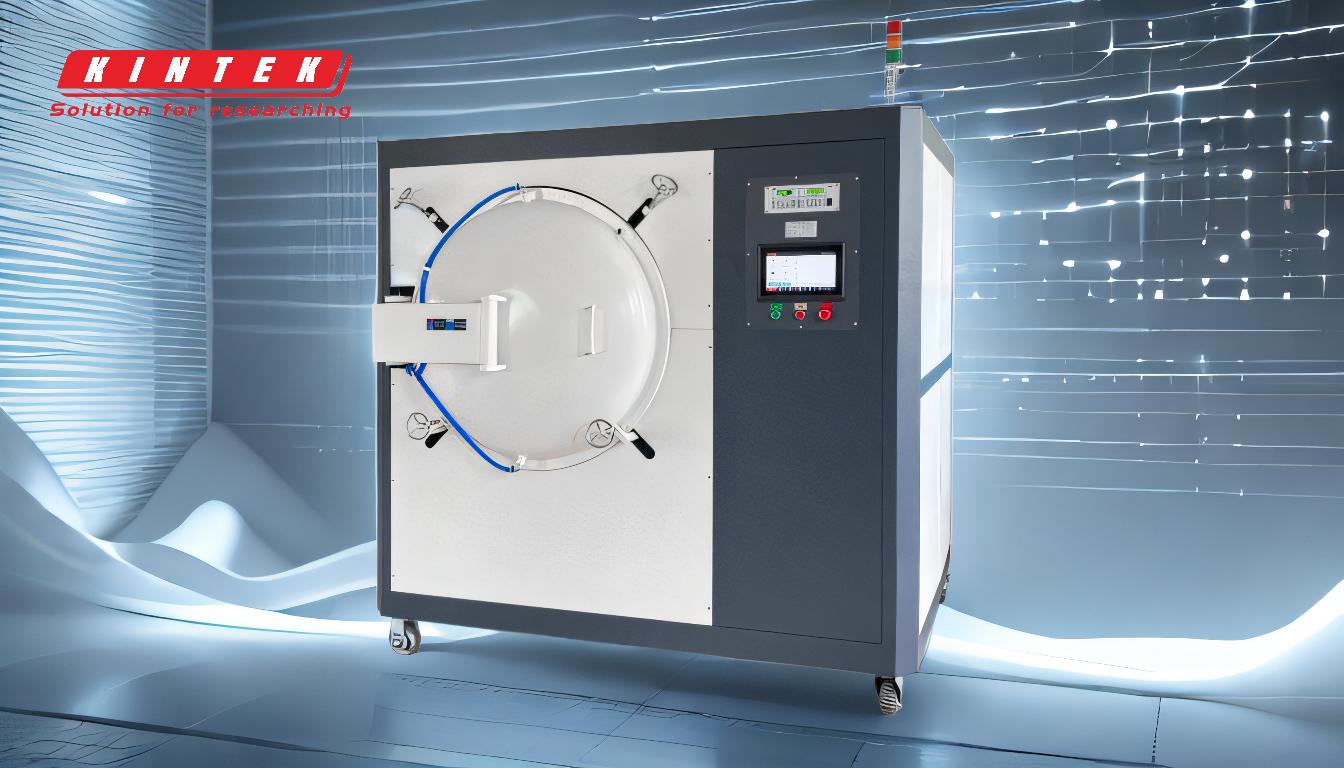
-
Standard Power Consumption:
- The average power consumption for a steel induction furnace is 625 kWh/ton. This is a benchmark value that provides a general idea of energy requirements for melting steel.
- This figure is based on the energy needed to heat and melt the material, accounting for heat losses and furnace inefficiencies.
-
Factors Influencing Power Consumption:
- Furnace Design: Modern IGBT induction furnaces are more energy-efficient compared to older models. They use advanced power electronics to reduce energy waste.
- Material Type: Different materials have varying melting points and specific heat capacities. For example, melting aluminum requires less energy than steel due to its lower melting point.
- Operating Temperature: Higher temperatures increase energy consumption. Maintaining precise temperature control can help optimize energy use.
- Process Efficiency: Factors like insulation quality, coil design, and power supply stability impact overall efficiency. Poor insulation or inefficient coils can lead to higher energy losses.
-
Energy Efficiency Improvements:
- Upgrading to an IGBT induction furnace can significantly reduce power consumption. IGBT technology offers better control over power output and reduces harmonic distortion, leading to lower energy losses.
- Implementing energy recovery systems, such as capturing waste heat, can further improve efficiency.
- Regular maintenance of the furnace, including coil cleaning and insulation checks, ensures optimal performance and minimizes energy waste.
-
Cost Implications:
- Energy consumption directly impacts operational costs. At 625 kWh/ton, the cost of electricity becomes a significant portion of the overall production expense.
- By improving efficiency and reducing power consumption, businesses can achieve substantial cost savings over time.
-
Environmental Considerations:
- Lower energy consumption not only reduces costs but also minimizes the environmental footprint of the furnace operation. This is increasingly important for companies aiming to meet sustainability goals.
By understanding these key points, purchasers and operators of induction furnaces can make informed decisions to optimize energy usage, reduce costs, and improve overall efficiency.
Summary Table:
Aspect | Details |
---|---|
Standard Consumption | 625 kWh/ton for steel melting |
Key Factors | Furnace design, material type, operating temperature, process efficiency |
Efficiency Tips | Upgrade to IGBT furnaces, implement energy recovery, regular maintenance |
Cost Impact | High electricity costs at 625 kWh/ton; efficiency improvements save money |
Environmental Benefit | Lower energy use reduces carbon footprint and supports sustainability goals |
Ready to optimize your induction furnace's energy use? Contact us today for expert advice!