Diamond-like carbon (DLC) coatings are ultra-thin, high-performance films used in various applications due to their exceptional hardness, low friction, and wear resistance. The thickness of DLC coatings typically ranges from 0.25 microns (250 nanometers) to 5 microns (5000 nanometers), depending on the application and deposition method. These coatings are applied using physical vapor deposition (PVD) techniques, ensuring minimal alteration to the engineered parts' specifications while enhancing their surface properties. The thinness of DLC coatings allows them to improve durability, reduce friction, and maintain the material's appearance without adding significant bulk.
Key Points Explained:
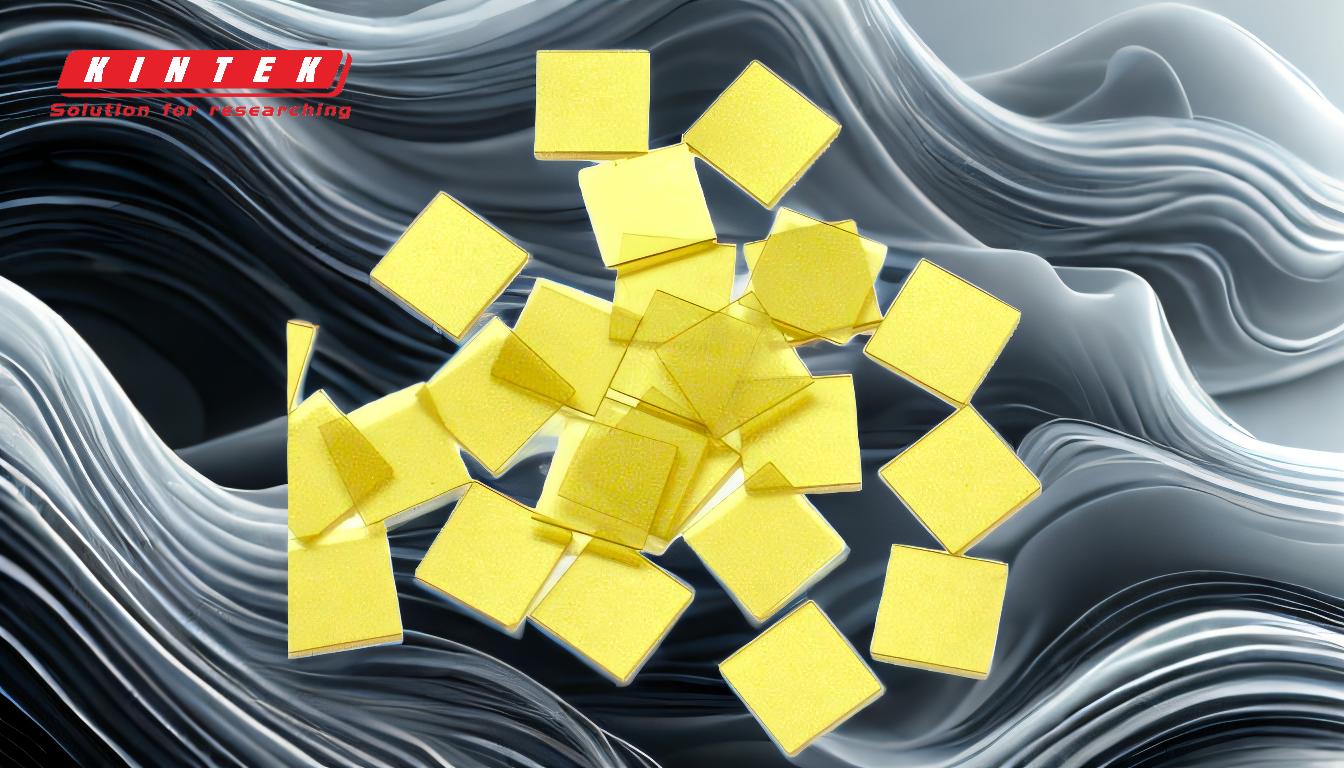
-
Typical Thickness Range of DLC Coatings
- DLC coatings are thin films, with thicknesses typically ranging from 0.25 microns to 5 microns.
- For reference:
- 1 micron = 0.001 millimeters or 1000 nanometers.
- A red blood cell is about 8 microns in diameter, and a human hair is around 80 microns thick.
- This ultra-thin nature ensures that the coatings do not alter the dimensions or specifications of the underlying material.
-
Application-Specific Thickness Variations
- The thickness of DLC coatings can vary based on the intended application:
- Decorative applications (e.g., stainless steel sheets) often use thinner coatings, around 0.25 to 0.5 microns.
- Functional applications (e.g., wear protection, friction reduction) may require thicker coatings, ranging from 2 to 5 microns.
- The choice of thickness depends on factors such as the required durability, hardness, and surface finish.
- The thickness of DLC coatings can vary based on the intended application:
-
Deposition Methods and Control
- DLC coatings are applied using Physical Vapor Deposition (PVD) techniques.
- The deposition process allows precise control over the coating's thickness, grain size, and surface roughness by adjusting parameters such as gas phase composition and deposition time.
- This customization ensures that the coating meets the specific performance requirements of the application.
-
Benefits of Thin DLC Coatings
- Despite their thinness, DLC coatings provide significant advantages:
- High hardness: Enhances wear resistance and durability.
- Low friction: Reduces energy loss and improves efficiency in moving parts.
- Chemical inertness: Provides resistance to corrosion and chemical degradation.
- Smooth surface finish: Improves appearance and reduces surface roughness.
- These properties make DLC coatings ideal for applications in industries such as automotive, aerospace, medical devices, and consumer electronics.
- Despite their thinness, DLC coatings provide significant advantages:
-
Comparison to Other Coatings
- DLC coatings are thinner than many traditional coatings but offer superior performance due to their unique properties.
- For example, while traditional hard coatings like chromium or titanium nitride may be thicker, DLC coatings provide better friction reduction and wear resistance at a fraction of the thickness.
-
Importance of Thickness in Engineering Applications
- The thinness of DLC coatings is critical in engineering applications where maintaining precise dimensions is essential.
- Thicker coatings could alter the fit, form, or function of precision components, whereas DLC coatings enhance performance without compromising these factors.
-
Future Trends in DLC Coating Technology
- Advances in deposition techniques are enabling even thinner and more uniform DLC coatings, expanding their use in micro- and nano-scale applications.
- Research is also focused on optimizing the deposition process to further enhance the coatings' properties, such as adhesion strength and thermal stability.
In summary, the thickness of diamond-like carbon coatings is a critical factor that determines their performance and suitability for specific applications. By carefully controlling the deposition process, manufacturers can tailor the coating's thickness to meet the exact requirements of their application, ensuring optimal performance and durability.
Summary Table:
Aspect | Details |
---|---|
Typical Thickness | 0.25 to 5 microns |
Applications | Decorative (0.25-0.5 microns), Functional (2-5 microns) |
Deposition Method | Physical Vapor Deposition (PVD) |
Key Benefits | High hardness, low friction, chemical inertness, smooth surface finish |
Industries | Automotive, aerospace, medical devices, consumer electronics |
Comparison to Others | Thinner than traditional coatings, superior friction and wear resistance |
Optimize your application with DLC coatings—contact our experts today for tailored solutions!