PVD (Physical Vapor Deposition) coating is a sophisticated surface finishing technique that enhances the properties of metals at a molecular level. It is widely used for its durability, corrosion resistance, and aesthetic appeal. The thickness of PVD coatings typically ranges from 0.25 microns to 5 microns, depending on the application and desired properties. This thin yet robust coating makes PVD ideal for applications requiring precision, such as cutting tools, where it preserves sharpness and reduces wear. The process operates at relatively low temperatures, minimizing thermal damage to the substrate, and produces coatings with high hardness and wear resistance. PVD coatings are also environmentally friendly, making them a sustainable choice for various industries.
Key Points Explained:
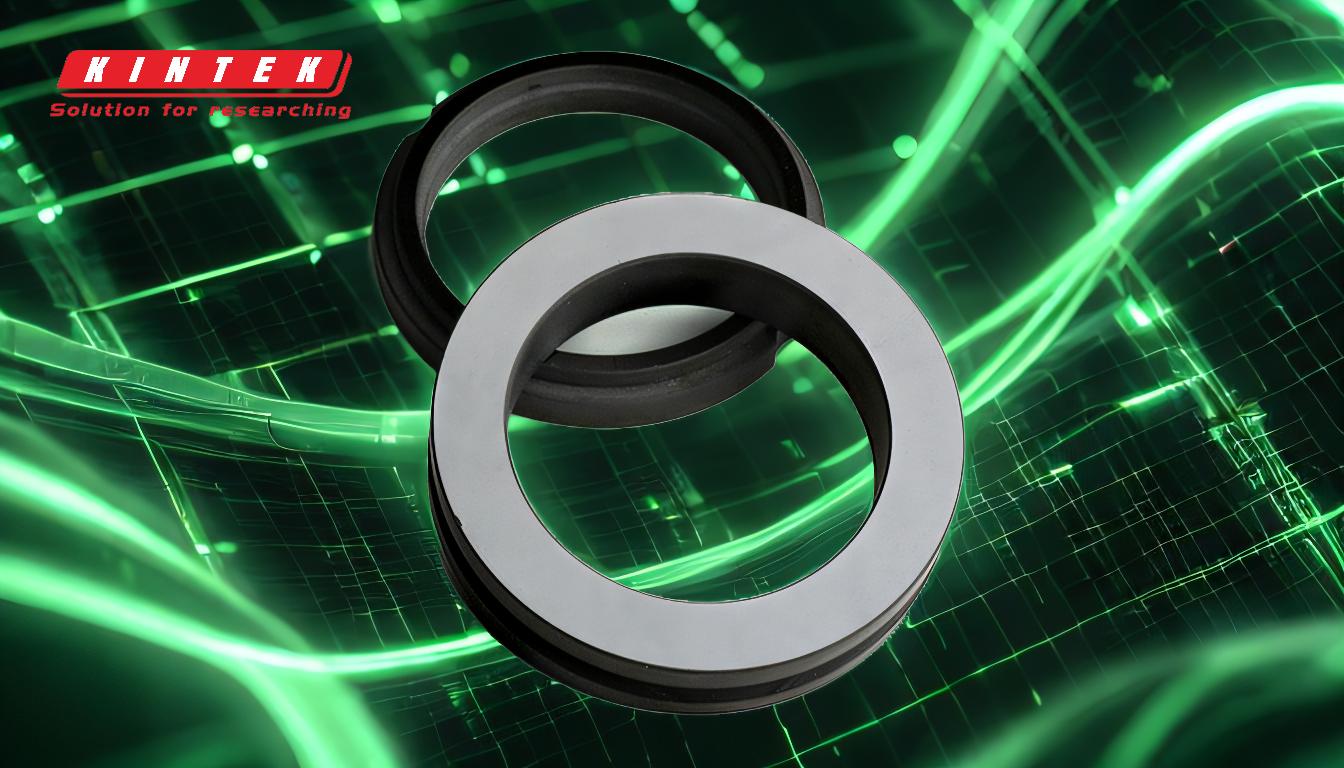
-
Range of PVD Coating Thickness
- PVD coatings are extremely thin, typically ranging from 0.25 microns to 5 microns.
- This thickness is sufficient to provide significant improvements in hardness, wear resistance, and corrosion protection without adding bulk to the substrate.
- The precise thickness depends on the application, with thinner coatings (0.25–1 micron) used for precision tools and thicker coatings (up to 5 microns) for enhanced durability in harsh environments.
-
Advantages of Thin PVD Coatings
- Preservation of Sharpness: For cutting tools, the thinness of PVD coatings (3–5 microns) ensures that the sharpness of the blade is maintained, reducing cutting force and heat generation during use.
- Compressive Stress Formation: The cooling process during PVD coating creates compressive stress, which helps prevent crack formation and expansion, making it suitable for interrupted cutting processes like milling.
- Low-Temperature Operation: PVD coatings are applied at temperatures around 500 °C, which minimizes the risk of thermal damage to the substrate, preserving its structural integrity.
-
Durability and Longevity
- PVD coatings are highly durable, with a lifespan ranging from 10 years to hundreds of years, depending on factors such as substrate material, coating thickness, and environmental conditions.
- This longevity makes PVD coatings cost-effective for long-term applications, such as in aerospace, automotive, and medical industries.
-
Environmental and Operational Benefits
- Fast Deposition Speed: PVD vacuum coating machines deposit coatings quickly, improving production efficiency.
- Environmentally Friendly: The process uses physical means rather than chemical reactions, reducing environmental impact.
- Versatility: PVD is suitable for coating a wide range of materials, including stainless steel, carbide, and complex tools, offering flexibility in application.
-
Applications of PVD Coatings
- Aesthetic Finishes: PVD coatings are used to create visually appealing surfaces with various colors and textures, making them popular in consumer products like watches and jewelry.
- Industrial Tools: The high hardness and wear resistance of PVD coatings make them ideal for cutting tools, molds, and other components subjected to high stress.
- Corrosion Resistance: The thin yet durable coating provides excellent protection against corrosion and oxidation, extending the life of components in harsh environments.
In summary, PVD coating is a versatile and efficient technology that provides a thin, durable, and environmentally friendly solution for enhancing the properties of metals. Its ability to operate at low temperatures, form compressive stress, and offer a wide range of thicknesses makes it suitable for diverse applications, from precision tools to decorative finishes.
Summary Table:
Aspect | Details |
---|---|
Thickness Range | 0.25–5 microns, depending on application and desired properties. |
Key Advantages | - Preserves sharpness in tools |
- Forms compressive stress
- Low-temperature operation (500°C) | | Durability | Lifespan of 10 years to hundreds of years, depending on conditions. | | Environmental Benefits| Fast deposition, eco-friendly, and versatile for various materials. | | Applications | Precision tools, decorative finishes, corrosion-resistant components. |
Interested in enhancing your materials with PVD coatings? Contact us today to learn more!