The thickness of PVD TiN coatings typically ranges from 0.25 to 12 microns, with most applications falling between 1 to 5 microns. This thin yet durable coating enhances material properties such as hardness, wear resistance, and corrosion resistance without significantly altering the substrate's appearance or dimensions. The precise thickness depends on the application, with thinner coatings (0.25–5 microns) often used for jewelry or precision tools, while thicker coatings (up to 12 microns) may be employed for industrial or heavy-duty applications. PVD TiN coatings are known for their metallic gold appearance, high purity (>99%), and ability to operate at lower temperatures, reducing thermal damage to the substrate.
Key Points Explained:
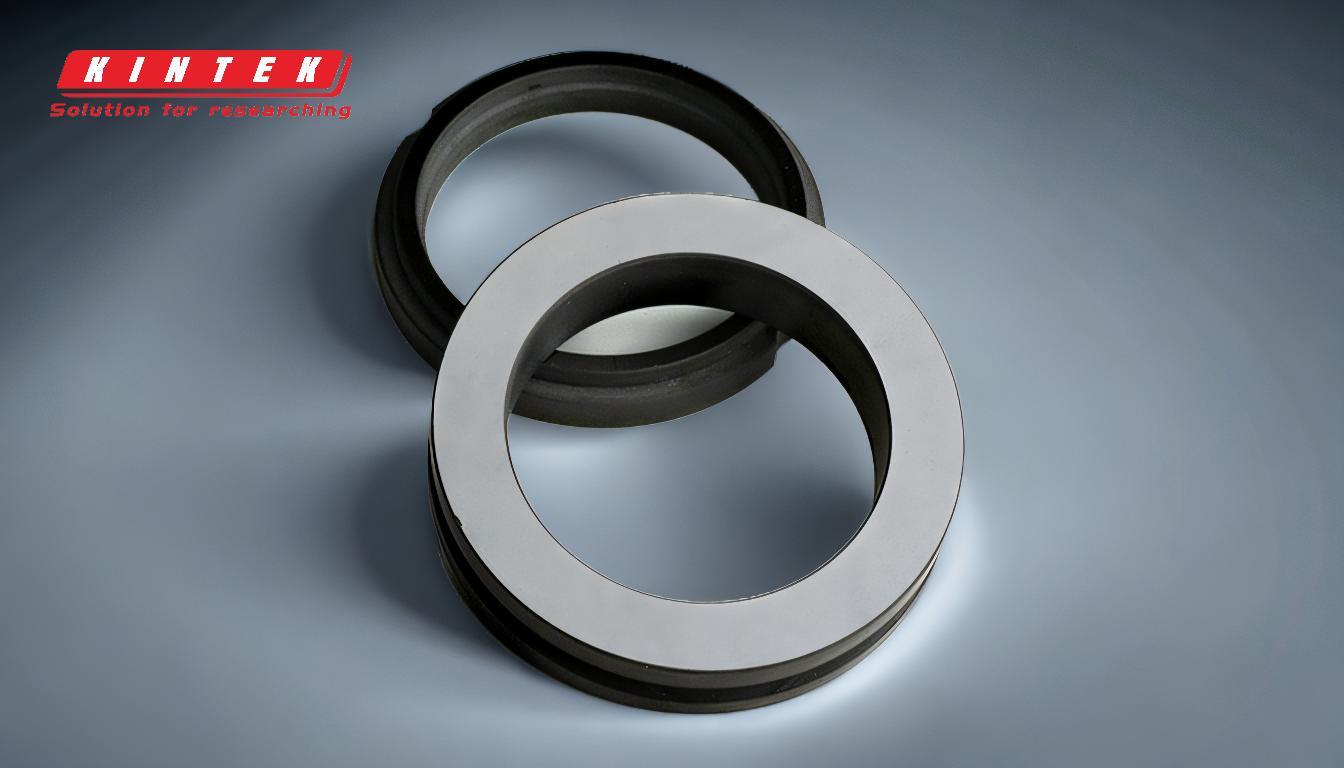
-
Thickness Range of PVD TiN Coatings
- PVD TiN coatings typically range from 0.25 to 12 microns, with most applications using 1 to 5 microns.
- This range ensures the coating is thin enough to preserve the substrate's dimensions while providing enhanced surface properties.
- Thinner coatings (0.25–5 microns) are common for precision tools and jewelry, while thicker coatings (up to 12 microns) are used for industrial applications requiring greater durability.
-
Typical Applications and Thickness
- Jewelry: Coating thickness is usually between 0.25 to 5 microns, which is significantly thinner than a human hair (70 microns).
- Precision Tools: Coatings of 1 to 5 microns are common, as they preserve the sharpness of cutting edges and reduce friction during use.
- Industrial Components: Thicker coatings (up to 12 microns) may be used for components exposed to harsh conditions, such as high wear or corrosion.
-
Benefits of Thin PVD TiN Coatings
- Enhanced Properties: The thin coating improves hardness, wear resistance, and corrosion resistance without altering the substrate's appearance or dimensions.
- Lower Operating Temperatures: PVD processes operate at around 500 °C, reducing the risk of thermal damage to the substrate.
- Compressive Stress Formation: During cooling, PVD coatings form compressive stress, which helps prevent crack formation and expansion, making them ideal for interrupted cutting processes like milling.
-
Process and Composition
- PVD TiN coatings are applied through vacuum deposition, ensuring high purity (>99%) and uniform thickness.
- The process is characterized by fast deposition speed, low deposition temperature, and environmentally friendly physical means, making it suitable for coating precision and complex tools.
-
Comparison to Other Coatings
- PVD coatings are significantly thinner than many other coating methods, which often results in better performance for precision applications.
- The thinness of PVD coatings (0.5–5 microns) ensures they do not alter the specifications of engineered parts, unlike thicker coatings that may affect dimensions or tolerances.
-
Appearance and Aesthetic Applications
- PVD TiN coatings have a metallic gold appearance, making them popular for decorative applications like jewelry and watches.
- Despite their thinness, these coatings provide a durable and attractive finish that resists tarnishing and wear.
-
Versatility and Suitability
- PVD TiN coatings are suitable for a wide range of substrates, including stainless steel, carbide, and other metals.
- The ability to form ceramic and composite coatings with high hardness and wear resistance makes PVD TiN a versatile choice for both functional and aesthetic applications.
In summary, the thickness of PVD TiN coatings is tailored to the specific application, balancing durability, performance, and aesthetics. Whether for precision tools, jewelry, or industrial components, the thin yet robust nature of PVD TiN coatings makes them a preferred choice for enhancing material properties without compromising the substrate's integrity.
Summary Table:
Application | Thickness Range (microns) | Key Benefits |
---|---|---|
Jewelry | 0.25–5 | Enhances appearance, durability, and resistance to tarnishing. |
Precision Tools | 1–5 | Preserves sharpness, reduces friction, and improves wear resistance. |
Industrial Components | Up to 12 | Provides enhanced durability for harsh conditions like wear and corrosion. |
General Benefits | Improves hardness, wear resistance, and corrosion resistance without altering dimensions. |
Need help choosing the right PVD TiN coating thickness for your project? Contact our experts today!