The thickness of the film in e-beam evaporation is influenced by several factors, including the geometry of the evaporation chamber, the pressure in the vacuum chamber, and the substrate temperature. These factors can cause variations in film thickness due to nonuniform deposition caused by collisions with residual gases and the movement of evaporated atoms. Proper control of these factors, such as maintaining a high degree of vacuum and heating the substrate, can help achieve a more uniform and high-quality thin film. The thickness can range widely depending on the specific conditions and parameters of the evaporation process.
Key Points Explained:
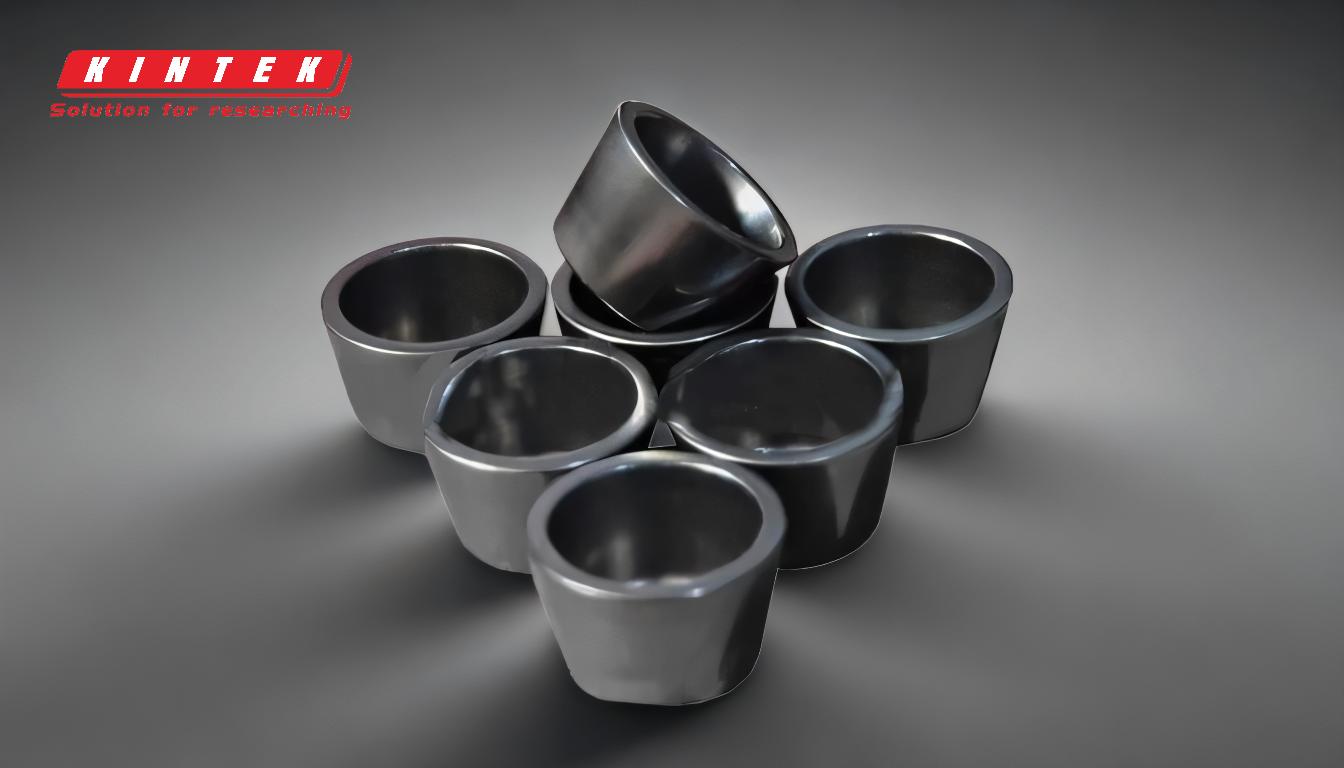
-
Influence of Evaporation Chamber Geometry:
- The geometry of the evaporation chamber plays a significant role in determining the thickness of the film. Nonuniform deposition can occur due to the varying distances and angles between the source material and different parts of the substrate. This can lead to thicker films in some areas and thinner films in others.
-
Impact of Vacuum Chamber Pressure:
- The pressure inside the vacuum chamber affects the free path of the source material molecules. A higher degree of vacuum reduces the number of collisions with residual gases, which can otherwise cause nonuniformity in film thickness. Lower pressure also minimizes the inclusion of impurities, leading to a purer and more uniform film.
-
Role of Substrate Temperature:
- The temperature of the substrate is crucial for the formation of a uniform film. Heating the substrate ensures that the evaporated atoms have enough energy to move freely and form a more uniform layer. Substrate temperatures above 150 °C can improve adhesion between the film and the substrate, contributing to better film quality and uniformity.
-
Effect of Source Material and Evaporation Rate:
- The molecular weight and evaporation rate of the source material also influence the film thickness. Different materials will have different deposition rates, and the evaporation rate must be carefully controlled to achieve the desired thickness. Higher deposition rates at a given vacuum pressure can improve film purity by minimizing the inclusion of gaseous impurities.
-
Importance of Substrate Surface Preparation:
- The preparation of the substrate surface is essential for achieving a uniform film thickness. A rough or uneven substrate surface can lead to nonuniform deposition, while a smooth and properly prepared surface promotes even film formation.
-
Variability Due to Process Parameters:
- The thickness of the film can vary significantly depending on specific process parameters such as the duration of the evaporation process, the power applied to the electron beam, and the mass of the source material. These parameters must be carefully controlled to achieve the desired film thickness and quality.
By understanding and controlling these factors, it is possible to achieve a more uniform and high-quality thin film through e-beam evaporation. The thickness of the film can range widely, but with proper process control, it can be tailored to meet specific requirements.
Summary Table:
Factor | Impact on Film Thickness |
---|---|
Evaporation Chamber Geometry | Nonuniform deposition due to varying distances and angles between source and substrate. |
Vacuum Chamber Pressure | Higher vacuum reduces collisions with residual gases, improving film uniformity and purity. |
Substrate Temperature | Heating above 150 °C enhances atom mobility, adhesion, and film uniformity. |
Source Material & Evaporation Rate | Molecular weight and evaporation rate affect deposition rates and film purity. |
Substrate Surface Preparation | Smooth surfaces promote uniform deposition; rough surfaces cause nonuniformity. |
Process Parameters | Duration, power, and source material mass must be controlled for desired thickness. |
Need help optimizing your e-beam evaporation process? Contact our experts today for tailored solutions!