Choosing the right sieve size is crucial for accurate particle size analysis and efficient material separation. The process involves understanding the material properties, the required particle size distribution, and the compatibility of the sieve with the sieving machine. Sieve sizes are typically defined by mesh numbers or aperture sizes, with finer sieves measured by the number of openings per linear inch. Additionally, factors like the type of material, sample size, and the capabilities of the sieving machine (such as filling capacity and sieve diameter) must be considered to ensure optimal performance and accurate results.
Key Points Explained:
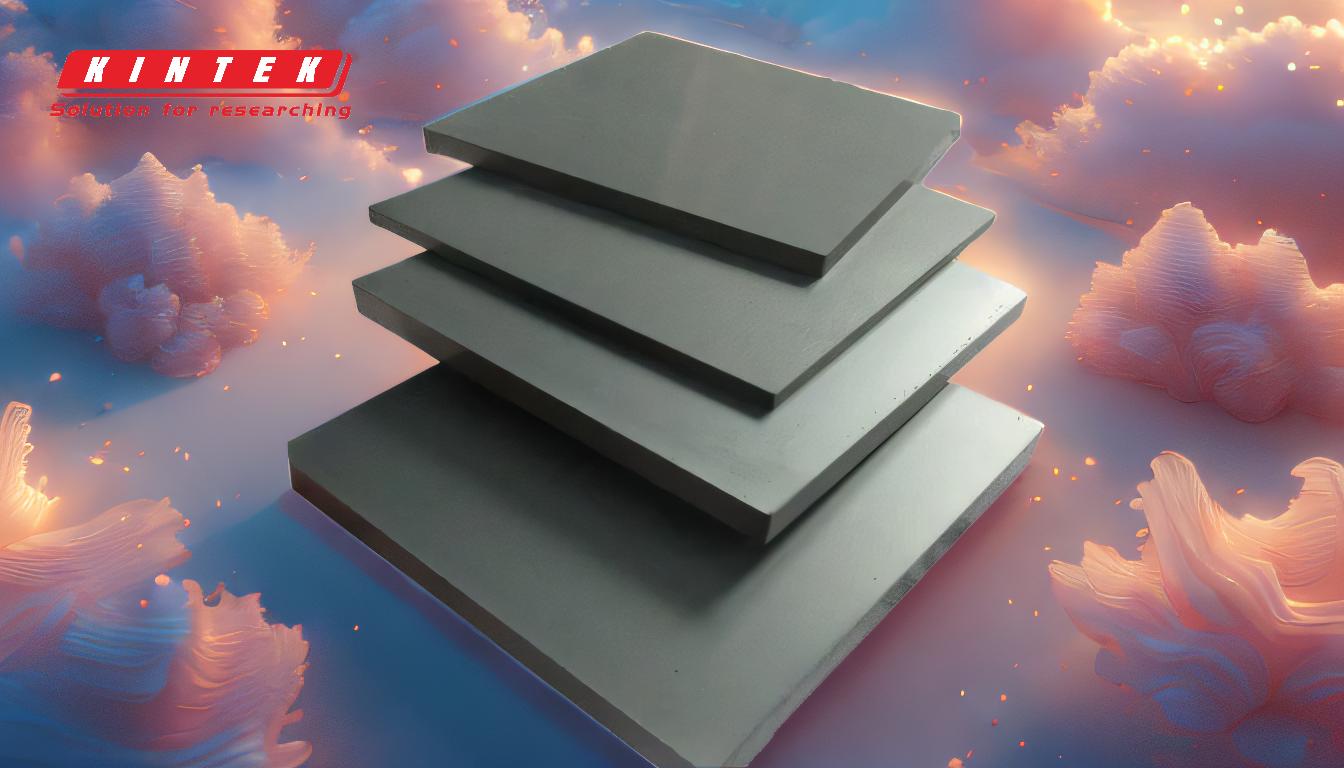
-
Understanding Sieve Size Standards:
- Sieve sizes are defined using either imperial (inch) or metric (millimeter) units. For apertures 1/4 inch (6.3 mm) or larger, sieve sizes are typically specified in inches. Finer sieves are described by mesh numbers, which indicate the number of openings per linear inch. For example, a No. 4 Sieve has four openings per inch.
- This standardization ensures consistency in particle size analysis across different applications and industries.
-
Material Characteristics:
- The type of material being tested is a critical factor in selecting the appropriate sieve size. Coarse materials like aggregates require larger sieve openings, while fine materials such as flour or powders need finer sieves with smaller apertures.
- Understanding the particle size distribution of the material helps in choosing the right sieve sizes to achieve the desired separation and analysis.
-
Sieve Shaker Compatibility:
- The diameter of the sieves must match the specifications of the sieve shaker. Different shakers are designed to accommodate specific sieve diameters, and using incompatible sizes can lead to inaccurate results or damage to the equipment.
- The sieve shaker should also be selected based on the material type and particle size. For example, shakers designed for fine powders may not be suitable for coarse aggregates.
-
Filling Capacity:
- The filling capacity of the sieving machine must align with the sample size. Overloading the sieve can lead to inefficient separation and clogging, while underloading may result in insufficient material for accurate analysis.
- Ensure that the sieving machine can handle the required capacity for your specific application to maintain optimal performance.
-
Frame Material Considerations:
- The material of the sieve frame affects its durability and suitability for different applications. Common materials include stainless steel, brass, and plastic. Stainless steel is preferred for its durability and resistance to corrosion, making it suitable for harsh environments.
- The choice of frame material should be based on practical considerations such as cost, longevity, and the specific requirements of the application.
-
Application-Specific Requirements:
- Different industries and applications may have unique requirements for sieve sizes and equipment. For example, the construction industry may prioritize sieves for coarse aggregates, while the food industry may focus on fine sieves for powders.
- Always consider the end-use and regulatory standards when selecting sieve sizes and equipment.
By carefully evaluating these factors, you can select the appropriate sieve size and equipment to ensure accurate and efficient particle size analysis for your specific needs.
Summary Table:
Factor | Key Considerations |
---|---|
Sieve Size Standards | Imperial (inch) or metric (mm) units; mesh numbers for finer sieves. |
Material Characteristics | Coarse materials need larger openings; fine materials require smaller apertures. |
Sieve Shaker Compatibility | Match sieve diameter and shaker specifications; consider material type and particle size. |
Filling Capacity | Align sample size with machine capacity to avoid overloading or underloading. |
Frame Material | Choose stainless steel, brass, or plastic based on durability and application needs. |
Application Requirements | Consider industry-specific standards and end-use requirements. |
Need help selecting the right sieve size for your application? Contact our experts today for personalized guidance!