Porosity in aluminum oxide, particularly in contexts like welding or material fabrication, can significantly affect the material's structural integrity and performance. To decrease porosity, it is crucial to focus on surface preparation, material handling, and process optimization. Thorough cleaning of the aluminum surface, either mechanically or chemically, is a foundational step to remove oxide layers and contaminants that contribute to porosity. Additionally, controlling environmental factors, such as humidity and temperature, and optimizing the fabrication process can further reduce porosity.
Key Points Explained:
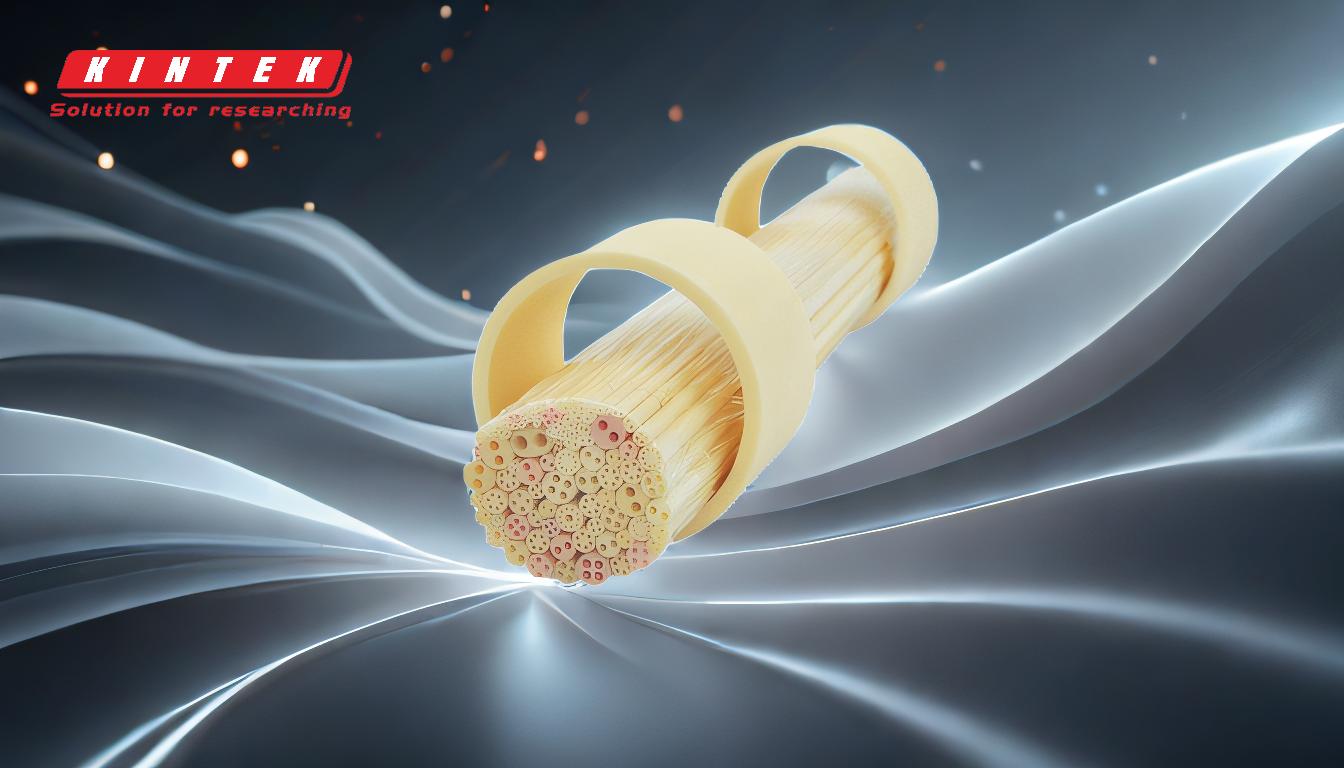
-
Surface Cleaning and Preparation:
- Mechanical Cleaning: Techniques like grinding, sanding, or brushing can effectively remove the oxide layer and surface contaminants. This ensures a clean surface for welding or fabrication, reducing the likelihood of porosity.
- Chemical Cleaning: Chemical etching or cleaning solutions can dissolve the oxide layer and other impurities. This method is particularly effective for intricate or hard-to-reach areas.
-
Material Handling and Storage:
- Proper storage of aluminum materials in a dry, controlled environment prevents moisture absorption, which can lead to porosity during welding or fabrication.
- Handling materials with clean gloves or tools minimizes the introduction of contaminants.
-
Environmental Control:
- Humidity Control: High humidity can introduce moisture into the welding process, leading to hydrogen-induced porosity. Using dehumidifiers or working in controlled environments can mitigate this risk.
- Temperature Management: Maintaining optimal temperatures during welding or fabrication prevents thermal stresses that can cause porosity.
-
Process Optimization:
- Welding Parameters: Adjusting welding parameters such as current, voltage, and travel speed can minimize porosity. For example, using higher currents can improve penetration and reduce the likelihood of gas entrapment.
- Shielding Gas: Using high-purity shielding gases, such as argon, and ensuring proper gas flow rates can protect the weld pool from atmospheric contamination.
-
Post-Processing Techniques:
- Heat Treatment: Post-weld heat treatment can help reduce residual stresses and close micro-porosities, improving the overall density of the material.
- Surface Finishing: Techniques like polishing or coating can further enhance the material's surface integrity and reduce porosity-related defects.
By addressing these key areas, porosity in aluminum oxide can be significantly decreased, leading to stronger and more reliable materials.
Summary Table:
Key Area | Strategies |
---|---|
Surface Cleaning | - Mechanical: Grinding, sanding, brushing - Chemical: Etching, cleaning solutions |
Material Handling | - Store in dry, controlled environments - Use clean gloves/tools for handling |
Environmental Control | - Control humidity with dehumidifiers - Maintain optimal temperatures |
Process Optimization | - Adjust welding parameters (current, voltage) - Use high-purity shielding gases |
Post-Processing | - Heat treatment to reduce stress - Surface finishing (polishing, coating) |
Need help reducing porosity in your aluminum oxide materials? Contact our experts today for tailored solutions!