PVD (Physical Vapor Deposition) coatings are renowned for their exceptional durability, making them a top choice for applications requiring long-lasting protection and performance. These coatings can last anywhere from 10 years to hundreds of years, depending on factors such as the substrate material, coating thickness, and application conditions. PVD coatings are highly resistant to corrosion, scratches, and oxidation, and their hardness and thinness contribute to their longevity. They are considered the most durable coating available today, outperforming traditional finishes in terms of quality and lifespan. The durability of PVD coatings is further enhanced by their robust temperature tolerance, impact strength, and resistance to abrasion, making them ideal for demanding environments.
Key Points Explained:
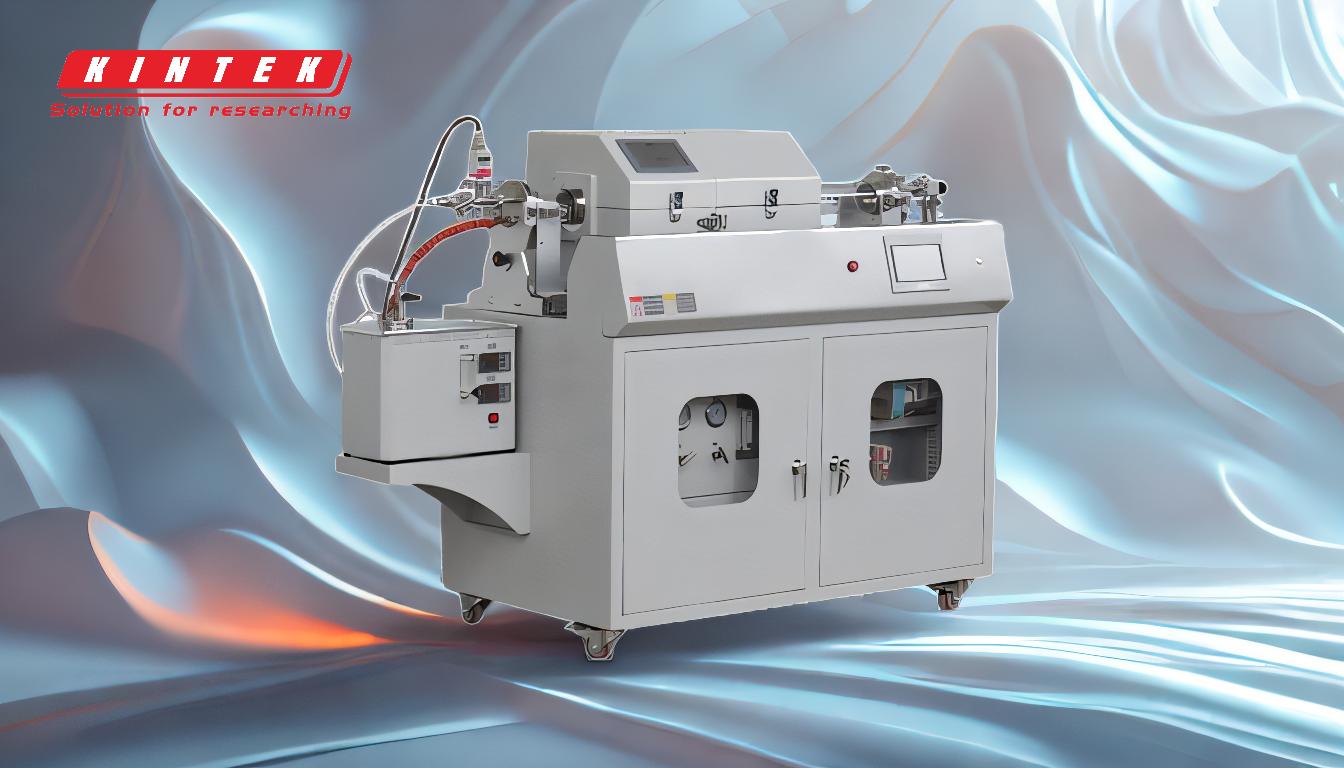
-
Durability and Lifespan:
- PVD coatings are extremely durable and can last from 10 years to hundreds of years, depending on factors like the substrate material, coating thickness, and application conditions.
- Their durability is attributed to their superior hardness and resistance to corrosion, scratches, and oxidation, which ensure they outlast traditional finishes.
-
Factors Influencing Durability:
- Substrate Material: The properties of the underlying substrate significantly impact the performance of PVD coatings. For example, a TiN (Titanium Nitride) coating on a Ti-6Al-4V alloy can increase the fatigue limit by 22% and endurance by 7%.
- Coating Thickness: PVD coatings are very thin, ranging from 0.5 microns to five microns. This thinness makes them difficult to remove and contributes to their durability.
- Application Conditions: The environment in which the coating is used (e.g., temperature, exposure to corrosive substances) also affects its lifespan.
-
Superior Hardness:
- PVD coatings are super-hard, making them the most durable coating available today. This hardness enhances their resistance to wear and tear, ensuring they maintain their integrity over time.
-
Resistance to Environmental Factors:
- Corrosion and Oxidation Resistance: PVD coatings are highly resistant to corrosion and oxidation, making them suitable for harsh environments.
- Abrasion Resistance: Their excellent abrasion resistance ensures they can withstand mechanical wear, further extending their lifespan.
-
Replication of Original Finish:
- PVD coatings can replicate the original finish of materials with minimal effort, maintaining the aesthetic appeal while providing enhanced durability.
-
Applications in Demanding Environments:
- Due to their robust temperature tolerance, impact strength, and resistance to abrasion and corrosion, PVD coatings are ideal for demanding applications where durability is critical.
In summary, PVD coatings are a highly durable and long-lasting solution, offering superior protection and performance compared to traditional finishes. Their durability is influenced by factors such as substrate material, coating thickness, and application conditions, and they excel in resisting corrosion, scratches, and abrasion. These properties make PVD coatings a reliable choice for a wide range of demanding applications.
Summary Table:
Aspect | Details |
---|---|
Lifespan | 10 years to hundreds of years |
Key Durability Factors | Substrate material, coating thickness, application conditions |
Hardness | Super-hard, enhancing wear and tear resistance |
Resistance | Corrosion, scratches, oxidation, and abrasion |
Thickness | 0.5 to 5 microns, contributing to durability |
Applications | Ideal for demanding environments requiring robust protection |
Upgrade your materials with PVD coatings—contact us today to learn more!