Aluminium brazing is a highly effective and widely used joining process, particularly in industries where lightweight, corrosion resistance, and thermal conductivity are critical. It involves joining aluminium components using a filler metal with a lower melting point than the base metal, typically in a controlled environment like a furnace. This method is suitable for a variety of applications, from automotive and aerospace to medical and industrial equipment. Below, we explore the key aspects of aluminium brazing, its advantages, and its applications.
Key Points Explained:
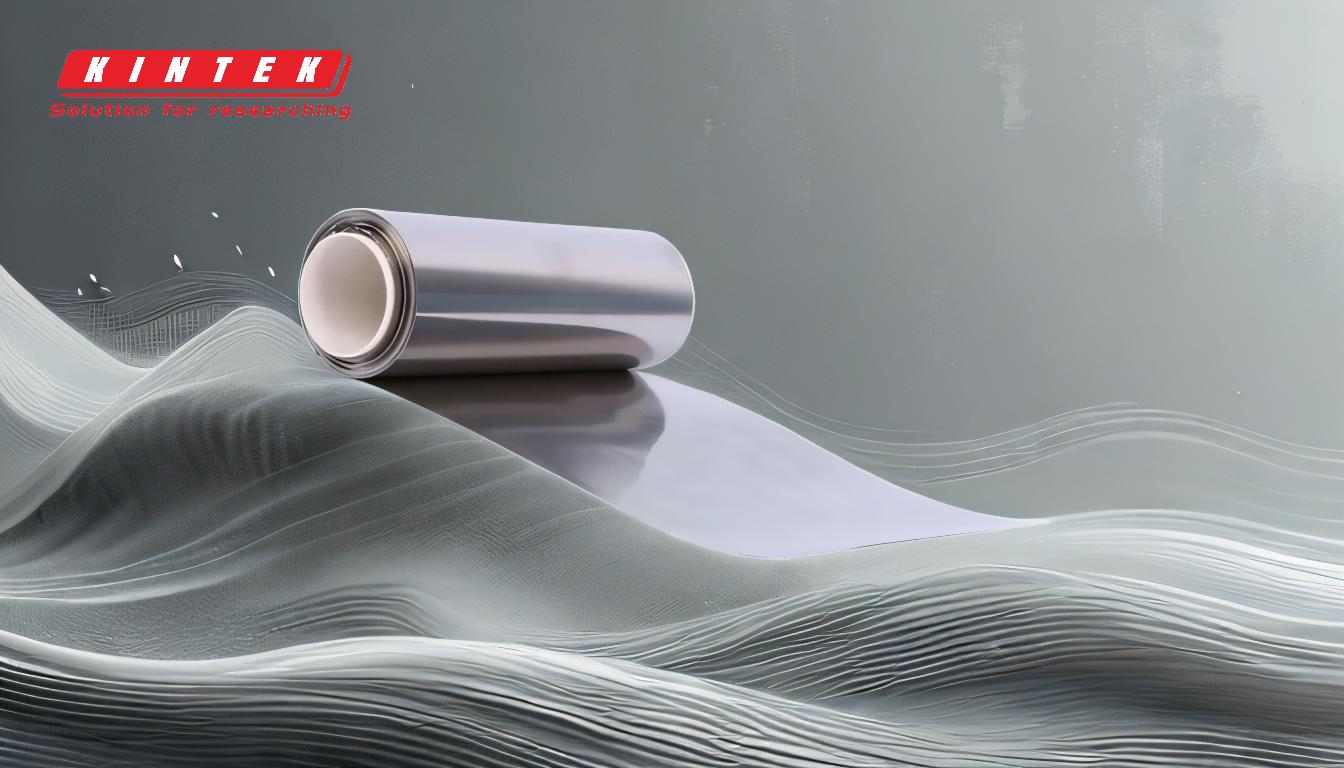
-
What is Aluminium Brazing?
- Aluminium brazing is a metal-joining process where a filler metal is used to bond aluminium components. The filler metal melts at a lower temperature than the base metal, ensuring the structural integrity of the parts while creating a strong, leak-proof joint.
- This process is typically performed in a controlled environment, such as a furnace, to ensure consistent heating and cooling, which minimizes distortion and oxidation.
-
Advantages of Aluminium Brazing
- Lightweight and Strong Joints: Aluminium brazing produces joints that are both lightweight and strong, making it ideal for applications where weight reduction is critical, such as in aerospace and automotive industries.
- Corrosion Resistance: The joints created through brazing are highly resistant to corrosion, which is essential for components exposed to harsh environments, such as offshore and petrochemical applications.
- Thermal Conductivity: Aluminium's high thermal conductivity is preserved in brazed joints, making it suitable for heat exchangers and other thermal management systems.
- Versatility: Aluminium brazing can be used to join complex geometries and thin-walled components, which are common in industries like electronics and medical equipment.
-
Applications of Aluminium Brazing
- Automotive Components: Aluminium brazing is widely used in the automotive industry for manufacturing heat exchangers, radiators, and air conditioning systems. The lightweight nature of aluminium helps improve fuel efficiency.
- Aerospace and Space Applications: In aerospace, brazed aluminium components are used for their strength-to-weight ratio and resistance to extreme temperatures.
- Medical and Scientific Equipment: The precision and cleanliness of furnace brazing make it suitable for medical devices and scientific instruments.
- Industrial and Petrochemical: Aluminium brazing is used in industrial gas turbines, nuclear components, and offshore equipment due to its corrosion resistance and durability.
- Electronics: The process is employed in the production of electronic devices where thermal management and lightweight materials are crucial.
-
Challenges and Considerations
- Surface Preparation: Proper cleaning and surface preparation are critical to ensure strong, defect-free joints. Any contamination can weaken the bond.
- Temperature Control: Brazing requires precise temperature control to avoid melting the base metal or creating weak joints.
- Filler Metal Selection: Choosing the right filler metal is essential to achieve the desired mechanical and thermal properties in the final product.
-
Furnace Brazing for Aluminium
- Furnace brazing is one of the most common methods for aluminium brazing. It provides a controlled environment with uniform heating, which is essential for achieving consistent results.
- This method is particularly suitable for high-volume production and complex assemblies, such as heat exchangers and hydraulic fittings.
In summary, aluminium brazing is an excellent joining method for a wide range of applications, offering advantages such as lightweight, corrosion resistance, and thermal conductivity. Its use in industries like automotive, aerospace, and medical equipment highlights its versatility and reliability. While it requires careful preparation and precise control, the benefits of aluminium brazing make it a preferred choice for many engineering and manufacturing challenges.
Summary Table:
Aspect | Details |
---|---|
Process | Uses a filler metal with a lower melting point than the base metal. |
Advantages | Lightweight, strong, corrosion-resistant, excellent thermal conductivity. |
Applications | Automotive, aerospace, medical, industrial, and electronics industries. |
Key Considerations | Surface preparation, temperature control, and filler metal selection. |
Common Method | Furnace brazing for uniform heating and high-volume production. |
Interested in aluminium brazing for your projects? Contact our experts today to learn more!