Brazing and welding are both widely used joining techniques, but they differ significantly in terms of strength, application, and process. Brazing uses a filler metal to join components without melting the base materials, making it suitable for applications requiring precision and minimal thermal distortion. Welding, on the other hand, involves melting the base materials to form a joint, resulting in stronger and more heat-resistant bonds. While brazed joints can be as strong as the base metals in certain applications, they generally have reduced strength and heat resistance compared to welded joints. The choice between brazing and welding depends on the specific requirements of the project, such as material compatibility, joint strength, and thermal considerations.
Key Points Explained:
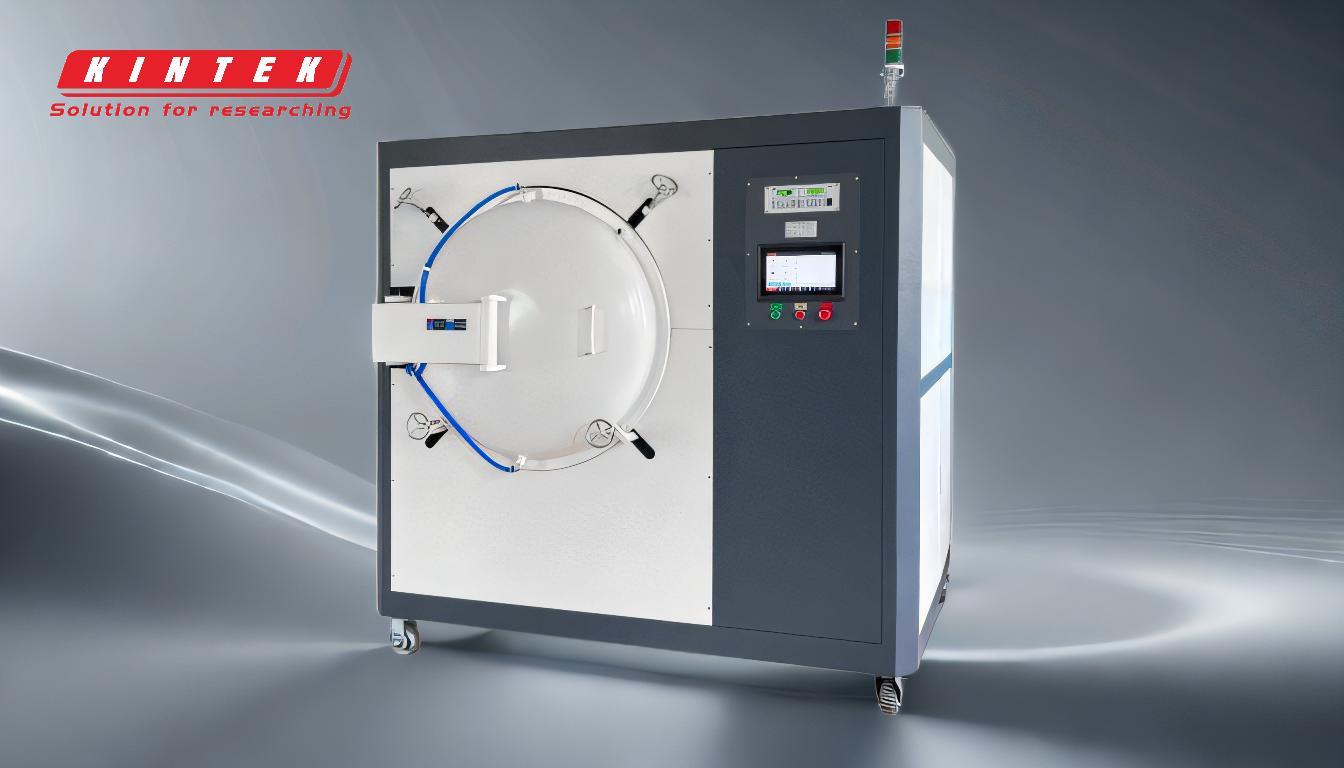
-
Strength Comparison Between Brazing and Welding:
- Brazed joints are strong and can achieve strength comparable to the base metals in certain applications, especially when the joint design and filler material are optimized.
- Welded joints, however, are typically stronger because they involve melting and fusing the base materials, creating a metallurgical bond that is more robust and heat-resistant.
- Brazing is often preferred for applications where thermal distortion must be minimized, but it may not be suitable for high-stress or high-temperature environments where welding excels.
-
Thermal Distortion and Heat-Affected Zone (HAZ):
- Brazing produces less thermal distortion compared to welding because it uniformly heats the entire assembly, avoiding localized high temperatures that can cause warping or distortion in the base metal.
- Welding, due to its high heat input, creates a significant heat-affected zone (HAZ), which can lead to metallurgical changes, such as hardening or cracking, especially in materials like cast iron.
- Brazing is advantageous for small repairs or delicate components where minimizing thermal distortion is critical.
-
Temperature and Filler Materials:
- Brazing occurs at higher temperatures, typically above 840°F (450°C), using filler metals that melt at lower temperatures than the base materials.
- Soldering, a similar process, uses filler metals with even lower melting points (below 840°F) and is generally weaker than brazing.
- The choice of filler material in brazing can significantly impact the joint's strength, corrosion resistance, and thermal performance.
-
Applications and Industry Use:
- Brazing is widely used in industries such as cookware, automotive, and HVAC systems due to its ability to create strong, leak-proof joints with minimal thermal distortion.
- Welding is preferred for structural applications, heavy machinery, and high-temperature environments where joint strength and durability are paramount.
- The decision to use brazing or welding depends on the specific requirements of the project, including material compatibility, joint design, and operational conditions.
-
Advantages and Limitations of Brazing:
- Advantages of brazing include reduced risk of cracking, minimal thermal distortion, and the ability to join dissimilar metals.
- Limitations include reduced strength and heat resistance compared to welding, making it less suitable for high-stress or high-temperature applications.
- Brazing is particularly useful for small cast iron repairs, where welding might cause cracking or other metallurgical issues.
In summary, while brazing offers several advantages, such as reduced thermal distortion and the ability to join dissimilar metals, it generally does not match the strength and heat resistance of welded joints. The choice between brazing and welding should be based on the specific needs of the application, including strength requirements, material compatibility, and thermal considerations.
Summary Table:
Aspect | Brazing | Welding |
---|---|---|
Strength | Comparable to base metals in optimized designs | Stronger due to metallurgical bond |
Thermal Distortion | Minimal, uniform heating reduces warping | Significant due to high heat input and HAZ |
Temperature | Above 840°F (450°C), uses lower-melting filler metals | Melts base materials, higher heat required |
Applications | Cookware, automotive, HVAC (minimal distortion, leak-proof joints) | Structural, heavy machinery, high-temperature environments |
Advantages | Minimal distortion, joins dissimilar metals, reduced cracking risk | Superior strength, durability, heat resistance |
Limitations | Reduced strength and heat resistance compared to welding | Higher risk of thermal distortion and metallurgical changes |
Need help choosing between brazing and welding? Contact our experts today for tailored advice!