Diamond-like Carbon (DLC) is a highly versatile and effective coating due to its unique combination of properties, including high hardness, low coefficient of friction, chemical resistance, and biocompatibility. It is widely used in industries such as automotive, machinery, optics, and biomedical applications. DLC coatings can be deposited at relatively low temperatures, making them suitable for a variety of substrates, and they exhibit excellent adhesion when paired with appropriate bonding layers. Their ability to enhance sliding properties, wear resistance, and corrosion resistance makes them a valuable choice for both functional and decorative applications. Overall, DLC is considered a good coating for many demanding environments.
Key Points Explained:
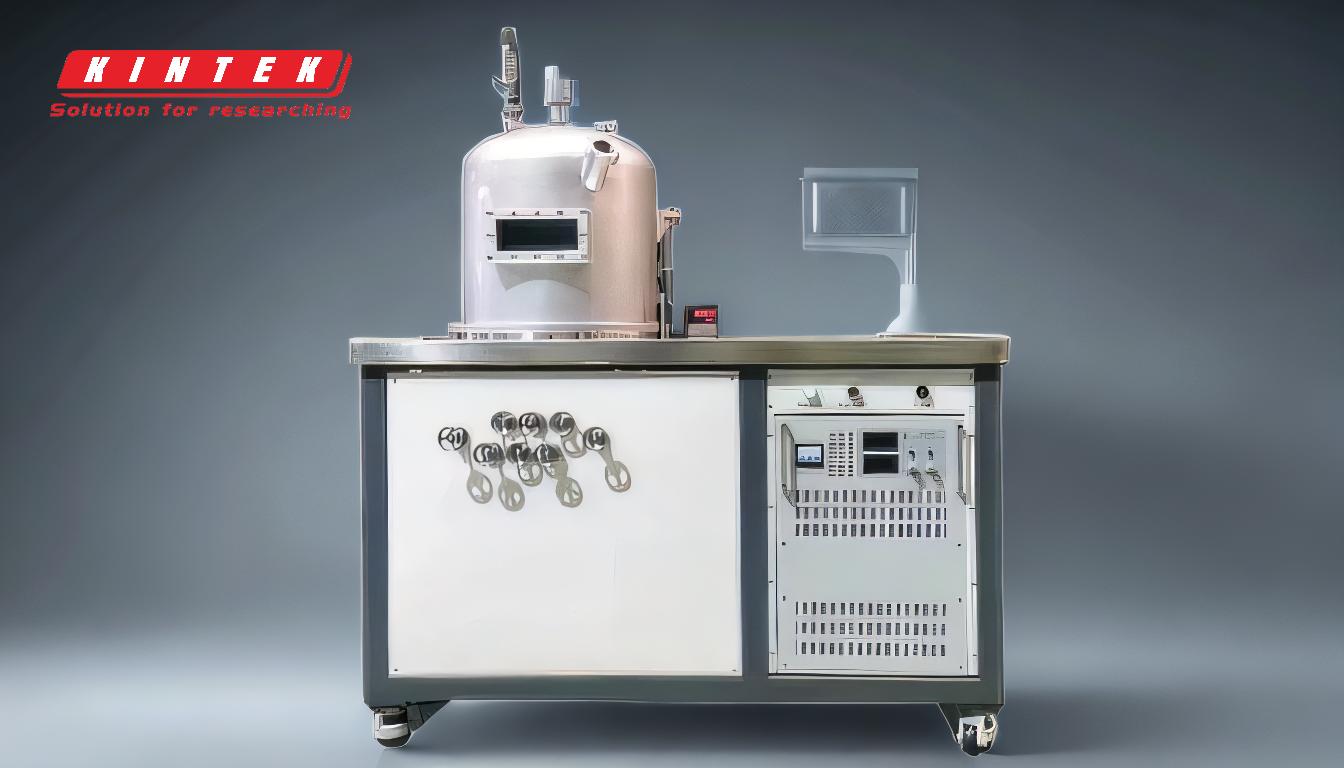
-
Unique Properties of DLC:
- DLC combines the hardness of diamond (1500–3000 HV) with the lubricity of graphite, making it highly durable and low-friction.
- It has a low coefficient of friction (COF), which is beneficial for sliding and wear-resistant applications.
- DLC coatings are chemically resistant and biocompatible, making them suitable for biomedical and corrosive environments.
-
Deposition and Adhesion:
- DLC can be deposited at relatively low temperatures (around 300 °C), which is advantageous for heat-sensitive substrates.
- Adhesion is enhanced by using bonding layers, such as silicon-based films produced by PACVD, especially on steel and hard metal substrates.
-
Applications Across Industries:
- Automotive and Machinery: DLC is used in power trains, bearings, camshafts, and other components to reduce friction and improve energy efficiency.
- Optical and Magnetic Components: It serves as a protective coating for optical components and magnetic memory discs, offering wear resistance and precision.
- Biomedical: DLC is used in prostheses and other medical devices due to its biocompatibility and wear resistance.
- Decorative and Functional: DLC coatings are used in watches and other decorative applications, combining luxury with functional benefits like hardness and scratch resistance.
-
Types of DLC:
- DLC films come in various forms, such as ta-C (tetrahedral amorphous carbon), a-C (amorphous carbon), and H-terminated DLC, each tailored for specific applications.
- The presence of both Sp3 (diamond-like) and Sp2 (graphite-like) carbon bonds contributes to their unique properties.
-
Advantages Over Other Coatings:
- High hardness and low friction make DLC superior in wear-resistant applications compared to many traditional coatings.
- Its ability to be precisely controlled in terms of thickness and refractive index makes it ideal for optical and sensing applications.
- The low-temperature deposition process expands its applicability to a wider range of materials.
-
Limitations and Considerations:
- While DLC has excellent adhesion with proper bonding layers, achieving consistent adhesion on all substrates can be challenging.
- The cost of DLC coatings may be higher than some alternatives, but this is often justified by their superior performance and longevity.
In summary, DLC is a highly effective and versatile coating that offers significant advantages in terms of hardness, friction reduction, and chemical resistance. Its applications span multiple industries, and its ability to be deposited at low temperatures with strong adhesion makes it a practical choice for many substrates. However, careful consideration of substrate compatibility and cost is necessary when selecting DLC for specific applications.
Summary Table:
Key Properties | Applications | Advantages |
---|---|---|
High hardness (1500–3000 HV) | Automotive and machinery | Superior wear resistance |
Low coefficient of friction | Optical and magnetic components | Enhanced sliding properties |
Chemical resistance | Biomedical devices | Biocompatibility and corrosion resistance |
Low-temperature deposition | Decorative applications | Precise control for optical/sensing uses |
Learn how DLC coatings can elevate your product performance—contact our experts today!